PVD (Physical Vapor Deposition) vacuum coating is a sophisticated thin-film deposition process conducted under vacuum conditions. It involves vaporizing a solid material, often referred to as the target, and depositing it onto a substrate to create a thin, durable, and high-performance coating. This process is widely used across industries such as aerospace, automotive, medical, and decorative applications due to its ability to enhance properties like wear resistance, hardness, and aesthetic appeal. PVD coatings are environmentally friendly, durable, and capable of significantly extending the lifespan of products.
Key Points Explained:
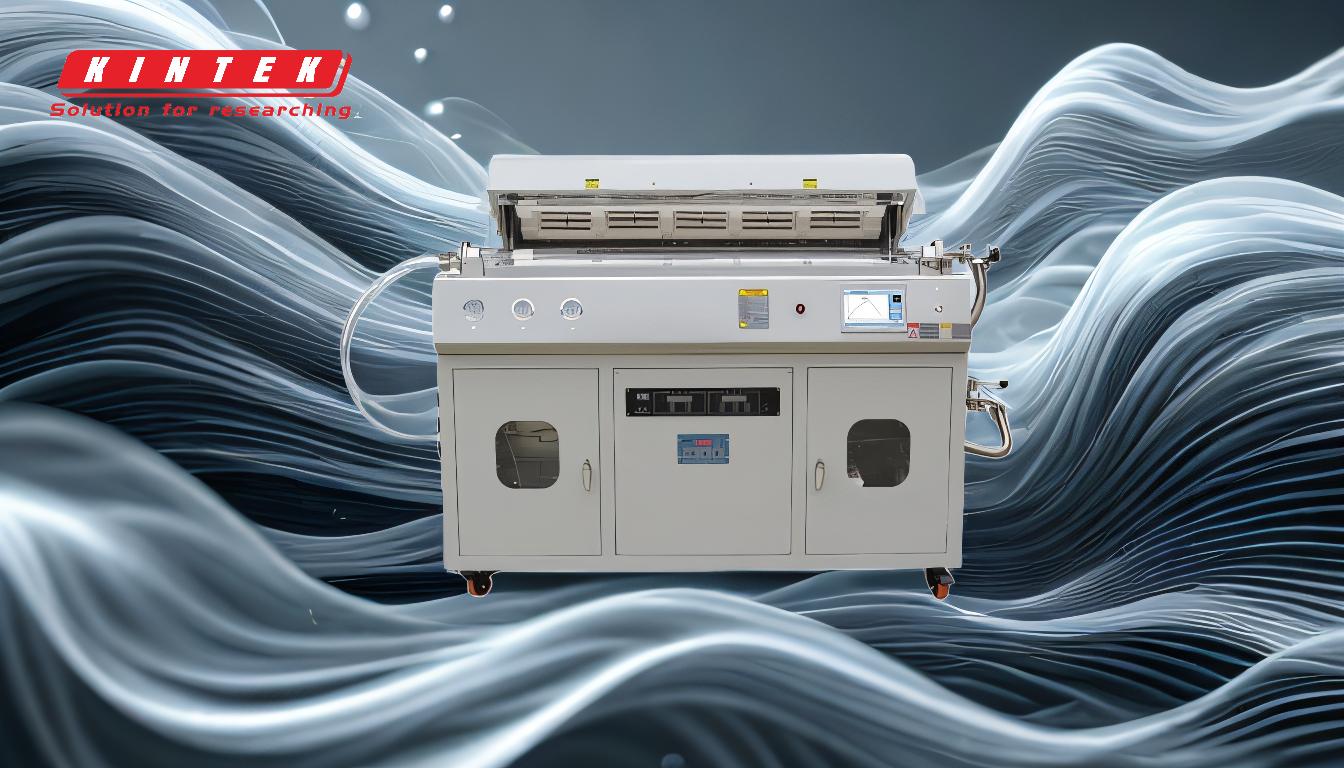
-
What is PVD Vacuum Coating?
- PVD vacuum coating is a process where a solid material is vaporized in a vacuum chamber and then deposited onto a substrate to form a thin film. The coating is typically only a few nanometers to micrometers thick but offers significant improvements in durability, hardness, and resistance to wear and oxidation. This process is widely used in industries requiring high-performance coatings, such as automotive, aerospace, and medical devices.
-
How Does PVD Coating Work?
- The PVD process involves several key steps:
- Ablation: A solid target material is bombarded with a high-energy source (e.g., electron beam or sputtering) to vaporize it.
- Transport: The vaporized atoms travel through the vacuum chamber.
- Reaction: In some cases, the vaporized atoms react with gases (e.g., nitrogen or oxygen) to form compounds like nitrides or oxides.
- Deposition: The atoms or compounds are deposited onto the substrate, forming a thin, uniform coating.
- The process is conducted in a vacuum to ensure purity and precision.
- The PVD process involves several key steps:
-
Applications of PVD Coating
- PVD coatings are versatile and used in a wide range of industries:
- Automotive: Used for coating wheels, pistons, and other components to improve durability and reduce friction.
- Aerospace: Enhances the performance of engine components and other critical parts.
- Medical: Applied to surgical tools and implants to improve biocompatibility and wear resistance.
- Decorative: Used in jewelry, door hardware, and other decorative items to enhance aesthetic appeal and durability.
- Industrial: Extends the lifespan of tools like drill bits and cutting implements.
- PVD coatings are versatile and used in a wide range of industries:
-
Advantages of PVD Coating
- Durability: PVD coatings are extremely hard and resistant to wear, making them ideal for high-stress applications.
- Environmental Friendliness: Unlike traditional chrome plating, PVD does not produce toxic substances, making it a greener alternative.
- Versatility: Can be applied to a wide range of materials, including metals, glass, and plastics.
- Aesthetic Appeal: Provides a high-quality finish with options for various colors and textures.
- Longevity: Can extend the lifespan of products by up to 10 times, with some coatings lasting over 25 years.
-
Types of PVD Coating Processes
- Electron-beam PVD: Uses a high-speed electron beam to vaporize the target material, which is then deposited onto the substrate. This method requires the substrate to be rotated for even coating.
- Sputtering: Involves bombarding the target material with ions to dislodge atoms, which are then deposited onto the substrate.
- Thermal Evaporation: The target material is heated until it vaporizes, and the vapor is deposited onto the substrate.
-
Environmental and Economic Benefits
- PVD coating is a sustainable alternative to traditional coating methods. It reduces the need for hazardous chemicals and produces minimal waste. Additionally, the extended lifespan of coated products reduces the frequency of replacements, leading to cost savings and reduced environmental impact.
-
Future Trends in PVD Coating
- As industries continue to prioritize sustainability and performance, PVD coating technology is expected to evolve. Innovations may include more efficient energy use, advanced materials for coatings, and expanded applications in emerging fields like renewable energy and electronics.
In summary, PVD vacuum coating is a highly effective and environmentally friendly method for applying thin, durable films to a variety of substrates. Its versatility, durability, and aesthetic benefits make it a preferred choice across multiple industries.
Summary Table:
Aspect | Details |
---|---|
Process | Vaporizes solid material in a vacuum, depositing it onto a substrate. |
Applications | Automotive, aerospace, medical, decorative, and industrial sectors. |
Advantages | Durability, environmental friendliness, versatility, and aesthetic appeal. |
Types of Processes | Electron-beam PVD, sputtering, thermal evaporation. |
Environmental Benefits | Reduces hazardous chemicals, minimal waste, and extended product lifespan. |
Interested in how PVD vacuum coating can benefit your industry? Contact us today to learn more!