Pyrolysis oil, a product derived from the thermal decomposition of organic materials like biomass or waste tires, holds significant economic and industrial value. Its worth is influenced by factors such as feedstock composition, production process, market demand, and regional policies. Currently, waste tire pyrolysis oil is priced at approximately $500 per ton, with prices on the rise, making it a lucrative product. However, its value is also tied to its complex chemical composition, which includes oxygenated compounds, polymers, and water, making it corrosive and challenging to handle. The economics of pyrolysis oil production are further shaped by local feedstock availability, plant scale, and technology type, with production costs ranging between 75 and 300 EUR per ton. Despite its potential, the lack of standardized quality benchmarks and its hazardous properties pose challenges to its broader adoption.
Key Points Explained:
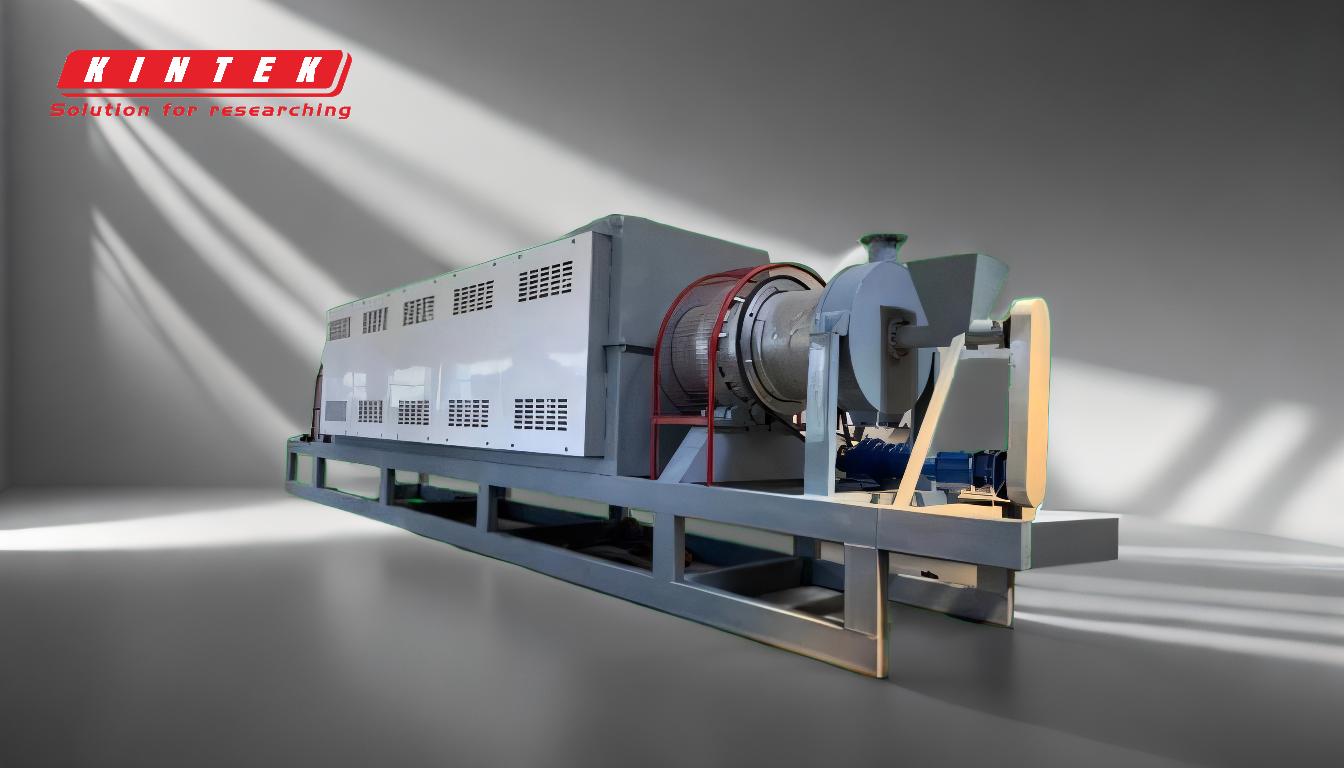
-
Factors Influencing Pyrolysis Oil Production:
- The quality and quantity of pyrolysis oil depend on the feedstock composition, process temperature, residence time, and particle size. These factors determine the thermal decomposition efficiency and the resulting product characteristics.
-
Market Value of Pyrolysis Oil:
- Waste tire pyrolysis oil is currently valued at around $500 per ton, with increasing market demand. This makes it a profitable product, especially in regions with restrictive landfill policies or a focus on resource conservation.
-
Composition and Properties of Pyrolysis Oil:
- Pyrolysis oil is a dark brown liquid emulsion containing oxygenated organic compounds, polymers, and water. It has a high oxygen content (up to 40% by weight) and a complex mixture of chemicals, ranging from low molecular weight compounds like formaldehyde to high molecular weight phenols. Its corrosive nature, acrid smell, and potential health risks (e.g., genetic defects and cancer) limit its direct use.
-
Standards and Quality Challenges:
- There are few established standards for pyrolysis oil, with ASTM being one of the few organizations providing guidelines. The lack of standardized benchmarks complicates its commercial adoption and integration into existing industrial processes.
-
Production Costs and Economic Viability:
- The cost of producing pyrolysis oil depends on feedstock pre-treatment, plant scale, and technology type. Studies suggest production costs range from 75 to 300 EUR per ton, assuming feedstock costs between 0 and 100 EUR per ton. Smaller-scale mobile units are particularly attractive in areas with reliable feedstock sources.
-
Yield Variations:
- The yield of pyrolysis oil, gas, and residue varies based on the type and percentage of plastic in the feedstock, as well as ash and soil content. Typically, pyrolysis oil yields range from 50% to 80%, gas yields from 20% to 35%, and residue yields from 3% to 30%.
-
Regional and Policy Influences:
- Pyrolysis technologies are more economically viable in regions with restrictive landfill policies (e.g., the EU and California) or a focus on local resource utilization (e.g., Asia and Africa). These factors drive demand for pyrolysis oil as a sustainable alternative.
In summary, pyrolysis oil's worth is multifaceted, influenced by its production process, market dynamics, and regional policies. While it offers significant economic potential, challenges related to its composition, handling, and standardization must be addressed to fully realize its value.
Summary Table:
Aspect | Details |
---|---|
Market Value | ~$500 per ton (waste tire pyrolysis oil), with rising demand |
Composition | Oxygenated compounds, polymers, water; corrosive and challenging to handle |
Production Costs | 75–300 EUR per ton, depending on feedstock, plant scale, and technology |
Yield Variations | Oil: 50–80%, Gas: 20–35%, Residue: 3–30% |
Regional Influences | Viable in regions with restrictive landfill policies or resource focus |
Challenges | Lack of standardization, hazardous properties, and handling difficulties |
Learn more about pyrolysis oil's potential and how it can benefit your business—contact us today!