A quenching furnace is a specialized piece of equipment used in metallurgical processes to rapidly cool a workpiece from a high temperature, typically to achieve desired material properties such as increased hardness or strength. This process, known as quenching, is crucial in the heat treatment of metals like steel, where rapid cooling transforms the microstructure into martensite, a hard and brittle phase. Quenching furnaces are often paired with other types of furnaces, such as batch furnaces or roller hearth furnaces, and require precise temperature control to ensure uniform heating and avoid defects. Advanced quenching furnaces, such as vacuum gas quenching furnaces, operate in a vacuum environment, using inert gases to cool the workpiece, which prevents oxidation and contamination, making them ideal for high-precision parts like alloys and stainless steel.
Key Points Explained:
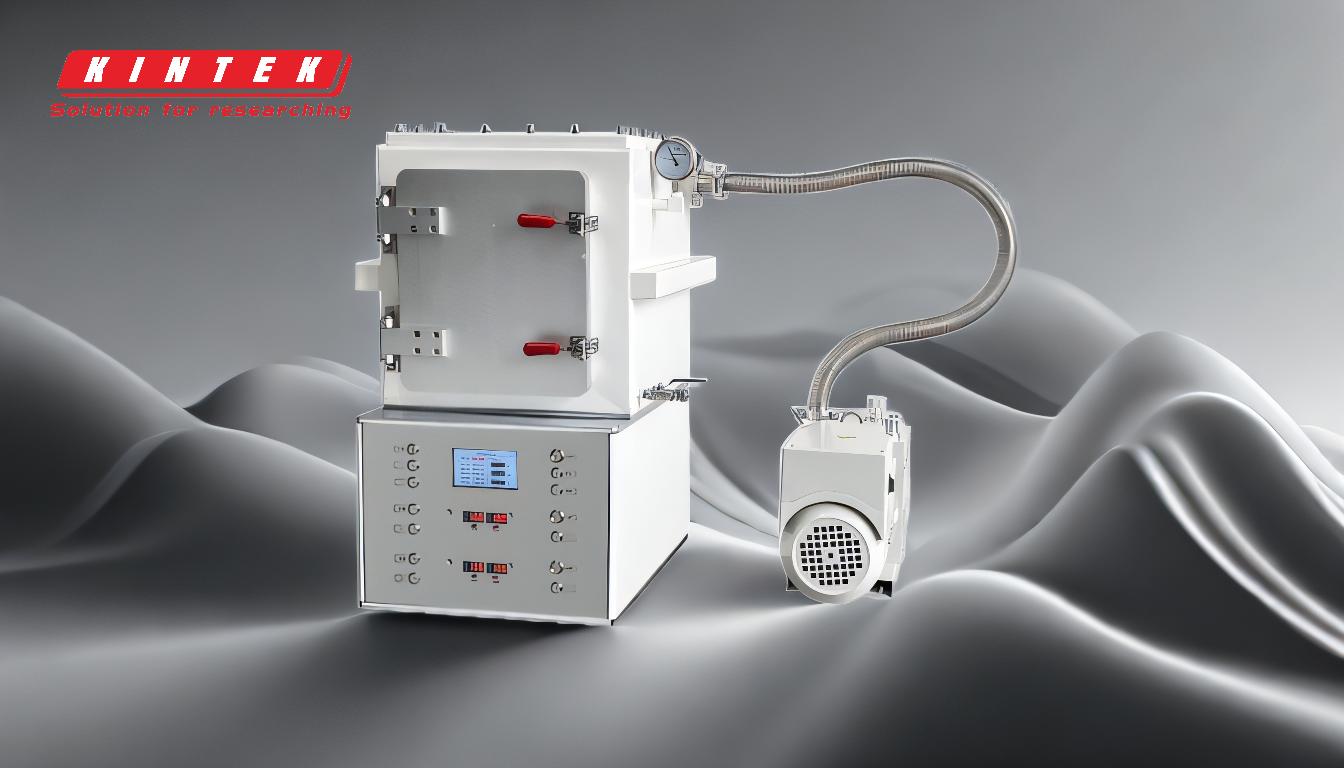
-
Definition and Purpose of Quenching Furnaces:
- A quenching furnace is designed to rapidly cool metals from high temperatures to achieve specific material properties, such as hardness and strength.
- The process of quenching is essential in heat treatment, particularly for steels, where it transforms the microstructure into martensite.
-
Cooling Methods in Quenching:
- Traditional quenching uses cooling mediums like water or oil to rapidly lower the temperature of the workpiece.
- Advanced quenching methods, such as those used in vacuum sintering furnaces, employ inert gases (e.g., nitrogen or argon) to cool the workpiece in a controlled environment, preventing oxidation and contamination.
-
Types of Quenching Furnaces:
- Batch Furnaces with Quenching: These are commonly used for small to medium-sized workpieces, where the furnace is loaded, heated, and then quenched in a separate chamber.
- Roller Hearth and Pusher Furnaces: These are continuous furnaces used for larger-scale operations, where workpieces move through the furnace and are quenched at the end of the heating cycle.
- Vacuum Gas Quenching Furnaces: These are advanced systems that operate in a vacuum environment, using high-pressure inert gases for quenching. They are ideal for high-precision parts like alloys, stainless steel, and titanium.
-
Key Features of Vacuum Gas Quenching Furnaces:
- Temperature Range: Capable of operating up to 2400°F (1315°C), making them suitable for a wide range of materials.
- Vacuum Levels: Achieve ultimate vacuum levels in the 10^-6 torr range, ensuring a contamination-free environment.
- Modular Design: Features a modular hot zone for easy maintenance and customization.
- Gas Quench Pressure: Offers selectable gas quench pressures from 2 bar to 10 bar, allowing precise control over the cooling process.
-
Applications of Quenching Furnaces:
- Quenching furnaces are used in various industries, including automotive, aerospace, and tool manufacturing, to enhance the mechanical properties of metal components.
- Vacuum gas quenching furnaces are particularly suited for high-precision parts, such as mold steels, high-speed steels, and titanium alloys, where oxidation and contamination must be minimized.
-
Advantages of Vacuum Quenching:
- Oxidation Prevention: The vacuum environment eliminates the risk of oxidation, ensuring a clean and bright surface finish.
- Uniform Cooling: Inert gas quenching provides uniform cooling, reducing the risk of distortion or cracking in the workpiece.
- Versatility: Supports multiple heat treatment processes, including quenching, annealing, and sintering, making it a versatile tool in metallurgical applications.
-
Operational Process of Quenching:
- In traditional quenching, the workpiece is heated in the furnace and then rapidly immersed in a cooling medium, such as water or oil.
- In vacuum gas quenching, the workpiece is heated in a vacuum, and inert gas is introduced to absorb heat and cool the workpiece rapidly. The gas is then recirculated after cooling.
-
Vertical vs. Horizontal Quenching Furnaces:
- Vertical Quenching Furnaces: Ideal for large, long workpieces like shafts or plates, as they minimize deformation during the quenching process.
- Horizontal Quenching Furnaces: Suitable for smaller or more compact workpieces, offering flexibility in handling and processing.
By understanding these key points, a purchaser can make informed decisions about the type of quenching furnace that best suits their needs, ensuring optimal performance and quality in their heat treatment processes.
Summary Table:
Aspect | Details |
---|---|
Purpose | Rapidly cools metals to achieve hardness, strength, and martensite formation. |
Cooling Methods | Traditional (water/oil) or advanced (inert gas in vacuum environment). |
Types | Batch, roller hearth, pusher, and vacuum gas quenching furnaces. |
Key Features | Temperature up to 2400°F, vacuum levels to 10^-6 torr, modular design. |
Applications | Automotive, aerospace, tool manufacturing, and high-precision parts. |
Advantages | Prevents oxidation, ensures uniform cooling, and supports multiple processes. |
Operational Process | Heating followed by rapid cooling in water, oil, or inert gas. |
Vertical vs. Horizontal | Vertical for large workpieces; horizontal for compact parts. |
Discover the perfect quenching furnace for your needs—contact our experts today!