Sintering in dentistry is a critical process used to transform milled dental materials, such as zirconia, into strong, durable restorations like crowns, bridges, or frameworks. This process involves heating the material to high temperatures without melting it, which binds the particles together and enhances the material's hardness and structural integrity. Dental sintering furnaces are specialized equipment designed to achieve these high temperatures, ensuring the final restoration meets the required strength and aesthetic standards. Sintering is particularly useful for materials with high melting points, as it avoids the need for liquefaction while improving material properties like density and surface finish.
Key Points Explained:
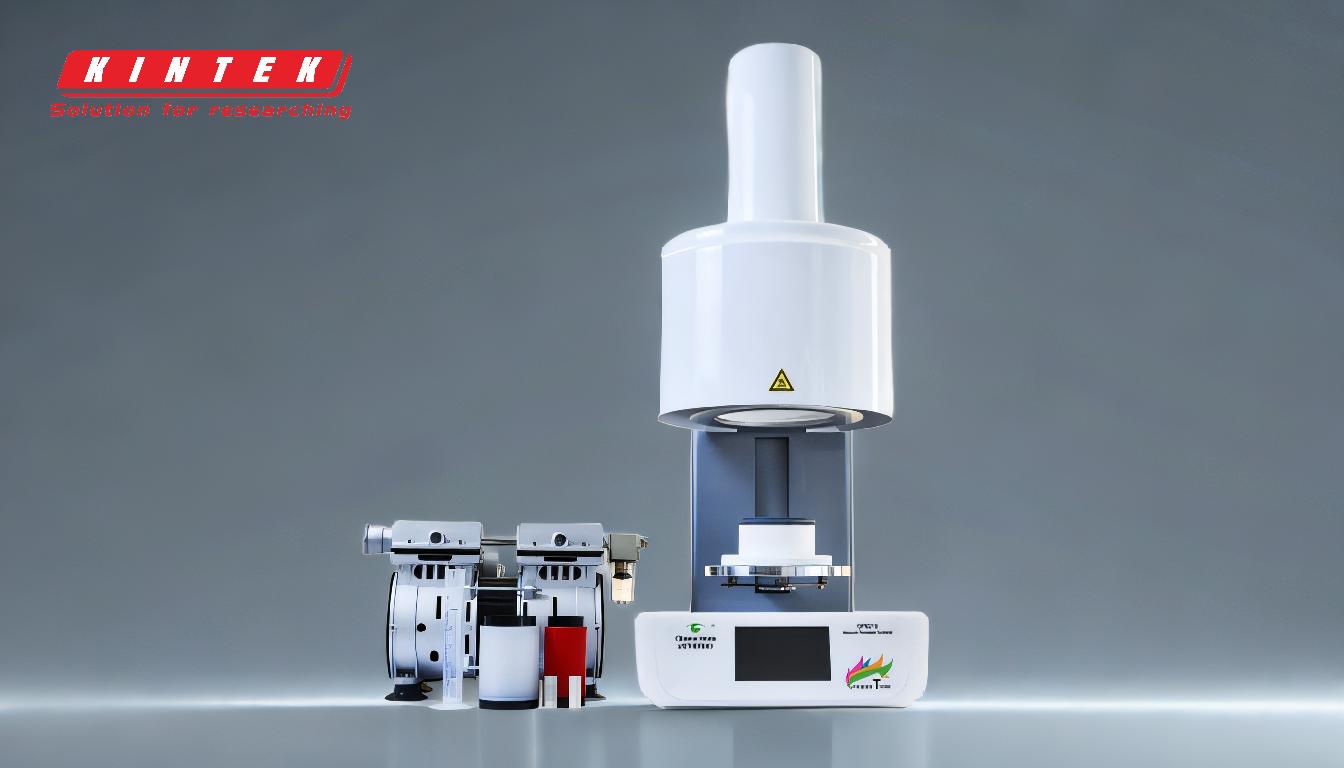
-
Definition of Sintering:
- Sintering is a thermal process where powdered or porous materials are heated to form a solid structure without reaching melting temperatures.
- In dentistry, this process is used to harden materials like zirconia, which are milled into dental restorations such as crowns, bridges, or frameworks.
-
Purpose of Sintering in Dentistry:
- Enhances Material Properties: Sintering improves the hardness, strength, and durability of dental materials, making them suitable for long-term use in the mouth.
- Reduces Porosity: The process reduces surface porosity, which enhances the material's resistance to wear and tear and improves its aesthetic appearance.
- Binds Particles Together: Sintering fuses the particles of the material, creating a cohesive and dense structure.
-
Role of Dental Sintering Furnaces:
- Dental sintering furnaces are specialized equipment designed to reach the high temperatures required for sintering zirconia and other dental materials.
- These furnaces ensure precise temperature control, which is crucial for achieving the desired material properties and avoiding defects.
-
Materials Used in Sintering:
- Zirconia: A popular material in dentistry due to its high strength, biocompatibility, and aesthetic properties. Sintering transforms milled zirconia into a dense, durable restoration.
- Other High-Melting-Point Metals: Sintering is also used for metals that are difficult to melt, as it allows for the creation of custom shapes and forms without requiring liquefaction.
-
Applications in Dentistry:
- Crowns and Bridges: Sintering is used to create strong, long-lasting crowns and bridges that can withstand the forces of chewing and biting.
- Frameworks: Dental frameworks for partial dentures or implant-supported restorations are often sintered to ensure they are robust and fit precisely.
- 3D Printing: Sintering is employed in some 3D printing processes to create custom dental restorations layer by layer, offering greater control and consistency.
-
Advantages of Sintering:
- Energy Efficiency: Sintering does not require melting, which saves energy compared to traditional melting processes.
- Precision and Control: The process allows for precise control over the final properties of the material, ensuring high-quality restorations.
- Versatility: Sintering can be used for a wide range of materials and applications, making it a versatile technique in dentistry.
-
Considerations for Equipment Purchasers:
- Temperature Range: Ensure the sintering furnace can reach the high temperatures required for the materials you plan to use.
- Precision and Uniformity: Look for furnaces with precise temperature control and uniform heating to avoid defects in the final restoration.
- Capacity and Size: Consider the size and capacity of the furnace to ensure it meets your production needs.
- Ease of Use: Choose a furnace with user-friendly controls and automation features to streamline the sintering process.
In summary, sintering is a vital process in modern dentistry, enabling the creation of strong, durable, and aesthetically pleasing dental restorations. Dental sintering furnaces play a crucial role in this process, providing the high temperatures and precision needed to achieve optimal results. For equipment purchasers, understanding the key features and considerations of sintering furnaces is essential for selecting the right equipment to meet their clinical and production needs.
Summary Table:
Key Aspect | Details |
---|---|
Definition | Heating powdered materials to form a solid structure without melting. |
Purpose | Enhances hardness, strength, and durability; reduces porosity. |
Role of Sintering Furnaces | Provides high temperatures and precise control for optimal results. |
Materials | Zirconia, high-melting-point metals. |
Applications | Crowns, bridges, frameworks, 3D-printed restorations. |
Advantages | Energy-efficient, precise, versatile. |
Equipment Considerations | Temperature range, precision, capacity, ease of use. |
Discover the right sintering furnace for your dental lab—contact us today to learn more!