Sintering of powdered metals and ceramics is a critical manufacturing process used to create dense, strong, and durable materials from powdered forms. It involves heating the powder compact (or "green" part) below its melting point in a controlled environment, such as a sintering furnace, to bond the particles together through diffusion and grain growth. This process is widely used in industries like automotive, aerospace, and electronics to produce components with precise shapes and properties. Sintering can occur in various environments, including vacuum, controlled atmosphere, or hot press conditions, depending on the material and desired outcome. The process enhances the mechanical, thermal, and electrical properties of the final product by eliminating porosity and improving particle bonding.
Key Points Explained:
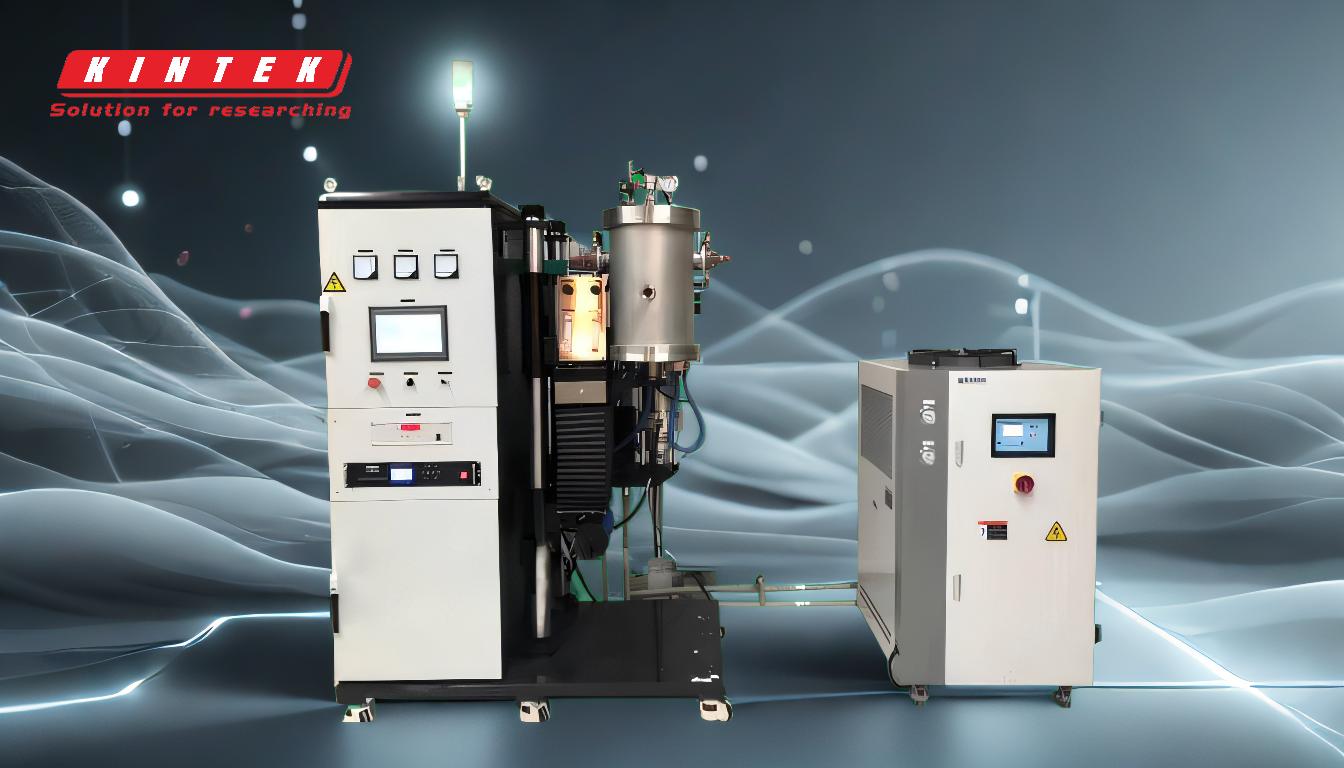
-
Definition and Purpose of Sintering:
- Sintering is a thermal process used to bond powdered metals or ceramics into a solid, dense material without melting the entire mass. It is essential for achieving high strength, hardness, and dimensional accuracy in manufactured parts.
- The process is widely used in powder metallurgy and ceramic manufacturing to produce complex shapes and components with tailored properties.
-
Steps in the Sintering Process:
- Powder Preparation: Metal or ceramic powders are selected and mixed with binders or lubricants to improve flowability and compaction.
- Compaction: The powder is pressed into a "green" part using mechanical or hydraulic presses. This step gives the part its initial shape and strength.
- Sintering: The green part is heated in a sintering furnace at temperatures below the melting point of the material. During this stage, particles bond through diffusion, and the part shrinks as porosity is reduced.
-
Types of Sintering Furnaces:
- Vacuum Sintering Furnace: Operates in a vacuum environment to prevent oxidation and contamination. Ideal for materials sensitive to oxygen, such as titanium or certain ceramics.
- Atmosphere Sintering Furnace: Uses controlled atmospheres (e.g., nitrogen, argon) to protect the material and enhance sintering quality. Commonly used for metals like stainless steel and copper.
- Hot Press Sintering Furnace: Combines high temperature and pressure to accelerate densification. Suitable for advanced ceramics and composite materials.
-
Key Mechanisms in Sintering:
- Diffusion: Atoms migrate across particle boundaries, leading to bonding and densification.
- Grain Growth: Particles grow larger as smaller grains merge, improving mechanical properties.
- Pore Elimination: Porosity decreases as particles rearrange and bond, resulting in a denser material.
-
Applications of Sintering:
- Metals: Used to produce gears, bearings, and structural components in automotive and aerospace industries.
- Ceramics: Applied in manufacturing cutting tools, insulators, and biomedical implants.
- Composites: Enables the production of advanced materials with tailored properties for specific applications.
-
Advantages of Sintering:
- Cost-Effective: Reduces material waste and allows for near-net-shape manufacturing.
- Versatility: Suitable for a wide range of materials, including metals, ceramics, and composites.
- Enhanced Properties: Improves strength, hardness, and wear resistance of the final product.
-
Challenges and Considerations:
- Temperature Control: Precise heating is required to avoid melting or incomplete sintering.
- Atmosphere Management: Proper control of the furnace environment is crucial to prevent contamination or oxidation.
- Material Selection: The choice of powder composition and binder affects the sintering outcome and final properties.
By understanding the sintering process and the role of a sintering furnace, manufacturers can optimize production parameters to achieve high-quality components with desired properties. This process is indispensable in modern manufacturing, offering a balance of precision, efficiency, and material performance.
Summary Table:
Aspect | Details |
---|---|
Definition | Thermal process to bond powdered metals/ceramics without melting. |
Key Steps | Powder Preparation, Compaction, Sintering in a furnace. |
Furnace Types | Vacuum, Atmosphere, Hot Press Sintering Furnaces. |
Key Mechanisms | Diffusion, Grain Growth, Pore Elimination. |
Applications | Gears, bearings, cutting tools, biomedical implants, and more. |
Advantages | Cost-effective, versatile, enhances strength and wear resistance. |
Challenges | Temperature control, atmosphere management, material selection. |
Optimize your manufacturing process with sintering—contact our experts today for tailored solutions!