Spark Plasma Sintering (SPS) is a modern sintering technique that employs a high pulsed DC current to heat and consolidate powder materials. It is known by several alternative names, including Pulsed Electric Current Sintering (PECS), Plasma Activated Sintering (PAS), Field Assisted Sintering Technology (FAST), and Electric Pulse Assisted Consolidation (EPAC). These names reflect different aspects of the process, such as the use of electric current, plasma activation, or field assistance, but they all refer to the same fundamental technique. The method is widely used in academia and industry for its ability to produce dense materials with fine microstructures at relatively low temperatures and short processing times.
Key Points Explained:
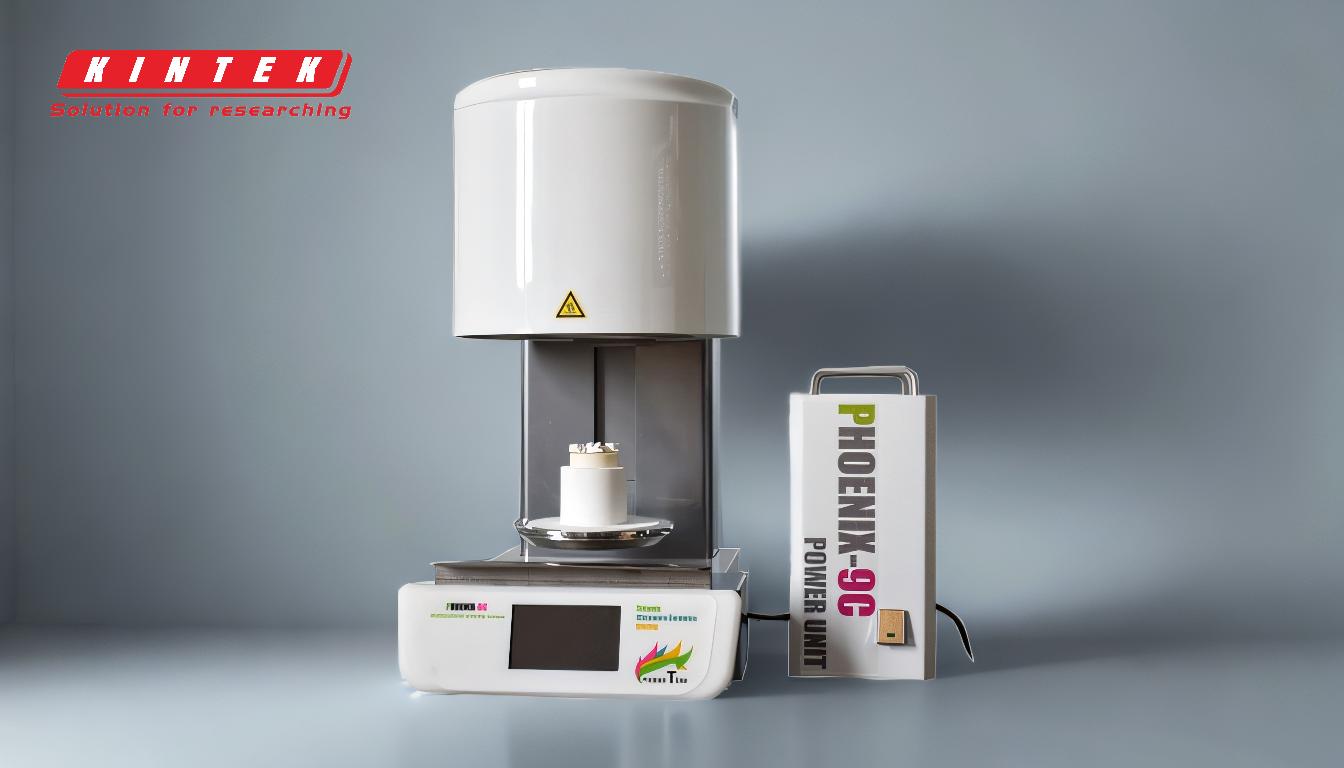
-
Spark Plasma Sintering (SPS) Overview:
- SPS is a sintering technique that uses a high pulsed DC current to heat and consolidate powder materials.
- It involves loading a powder compact into a die/punch setup, where the electric current passes through the material, generating heat and facilitating densification.
-
Alternative Names for SPS:
- Pulsed Electric Current Sintering (PECS): This name emphasizes the use of a pulsed electric current to achieve sintering. The pulsed nature of the current helps in controlling the heating rate and achieving uniform densification.
- Plasma Activated Sintering (PAS): This term highlights the role of plasma activation in the sintering process. The electric current can generate plasma at the particle surfaces, enhancing the sintering kinetics.
- Field Assisted Sintering Technology (FAST): This name underscores the application of an external field (electric field) to assist in the sintering process. The field aids in the rapid heating and consolidation of the powder compact.
- Electric Pulse Assisted Consolidation (EPAC): This term is often used in academic contexts and refers to the use of electric pulses to assist in the consolidation of powder materials. The pulses help in achieving high-density materials with controlled microstructures.
-
Significance of Different Names:
- The various names for SPS reflect different perspectives on the process, focusing on aspects such as the electric current, plasma activation, or field assistance.
- Despite the different names, all these terms refer to the same fundamental technique, which is characterized by the use of a pulsed DC current to achieve rapid and efficient sintering.
-
Applications and Advantages:
- SPS is widely used in both academia and industry for the production of advanced materials, including ceramics, metals, and composites.
- The technique offers several advantages, such as lower sintering temperatures, shorter processing times, and the ability to produce materials with fine microstructures and enhanced properties.
-
Conclusion:
- Spark Plasma Sintering is a versatile and efficient sintering technique known by various names, including PECS, PAS, FAST, and EPAC. These names reflect different aspects of the process but all refer to the same fundamental method of using a pulsed DC current to achieve rapid and controlled sintering of powder materials.
Summary Table:
Aspect | Details |
---|---|
Alternative Names | PECS, PAS, FAST, EPAC |
Key Feature | Uses pulsed DC current for rapid heating and consolidation |
Applications | Ceramics, metals, composites |
Advantages | Lower temperatures, shorter processing times, fine microstructures |
Learn more about how Spark Plasma Sintering can revolutionize your material production—contact us today!