Sputtering in semiconductor manufacturing is a Physical Vapor Deposition (PVD) technique used to deposit thin films of materials onto substrates, such as silicon wafers. This process involves bombarding a target material with high-energy ions, typically from an inert gas like argon, which ejects atoms from the target. These ejected atoms then travel through a vacuum and deposit onto the substrate, forming a thin, uniform film. Sputtering is widely used in semiconductor production due to its ability to produce high-purity coatings with excellent adhesion and uniformity. It is particularly valuable for depositing metals like gold, which are essential for the electrical and thermal conductivity of semiconductor components.
Key Points Explained:
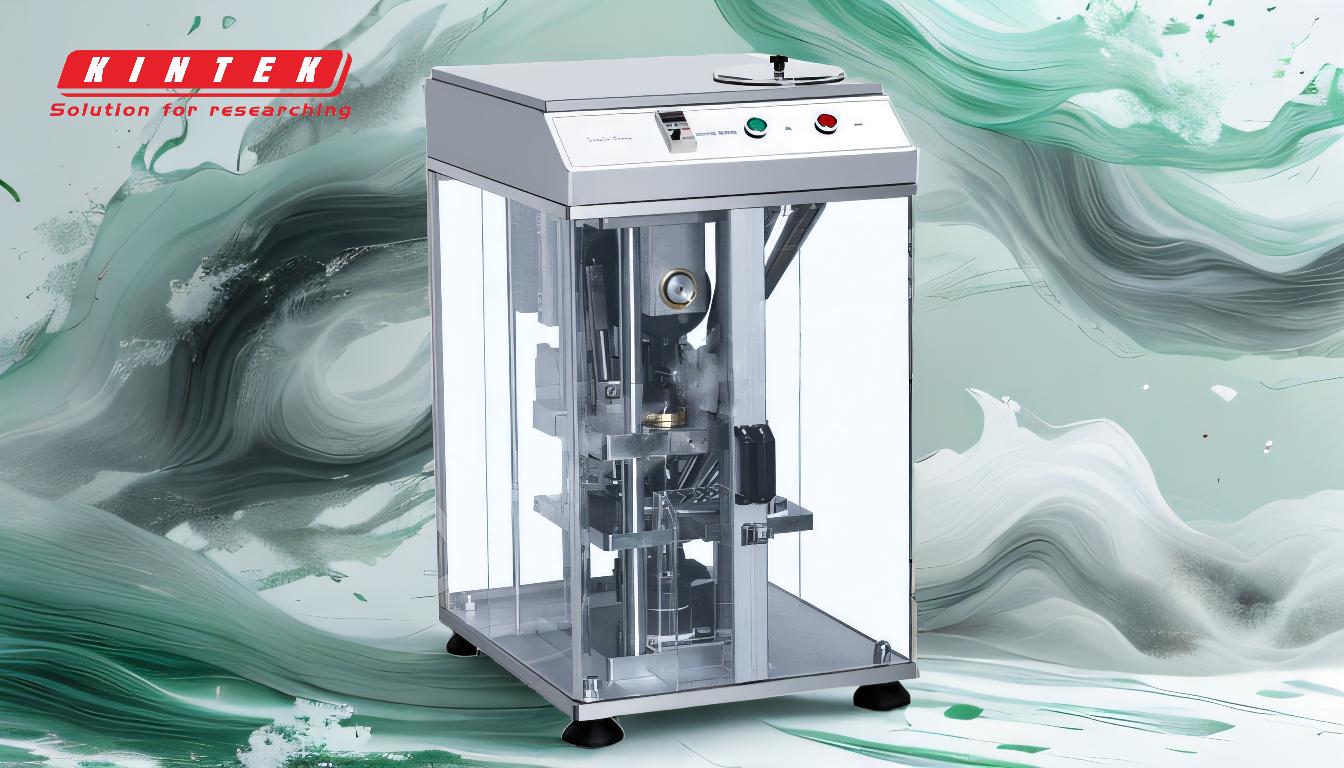
-
Definition of Sputtering:
- Sputtering is a PVD process where atoms are ejected from a solid target material due to bombardment by high-energy ions. These ejected atoms then deposit onto a substrate, forming a thin film. This method is widely used in semiconductor manufacturing to create precise and high-quality coatings.
-
Mechanism of Sputtering:
- The process begins by creating a vacuum in the reaction chamber to remove impurities and moisture.
- An inert gas, typically argon, is introduced into the chamber and ionized by applying a high voltage.
- The ionized argon atoms are accelerated toward the negatively charged target material, colliding with it and ejecting atoms from the target.
- These ejected atoms travel through the vacuum and deposit onto the substrate, forming a thin film.
-
Key Steps in the Sputtering Process:
- Vacuum Creation: The chamber is evacuated to a pressure of around 1 Pa to eliminate contaminants.
- Inert Gas Introduction: Argon gas is introduced to create a low-pressure atmosphere.
- Heating: The chamber is heated to temperatures between 150°C and 750°C to facilitate the process.
- Magnetic Field Creation: Tools are placed between the target and an electromagnet to generate a magnetic field, enhancing the efficiency of ion bombardment.
- Ionization and Bombardment: A high voltage is applied to ionize the argon gas, and the target is negatively charged to attract the positively charged argon ions, which then collide with the target, ejecting atoms.
- Film Deposition: The ejected atoms deposit onto the substrate, forming a thin film.
-
Applications in Semiconductor Manufacturing:
- Sputtering is extensively used in the semiconductor industry to deposit thin films of metals like gold, which are crucial for the electrical and thermal conductivity of semiconductor components.
- The process allows for the application of extremely pure, single-atom-thick coatings, which are essential for meeting the high technical requirements of semiconductor production.
-
Advantages of Sputtering:
- High Purity: Sputtering can produce films with extremely high purity, which is critical for semiconductor applications.
- Uniformity: The process allows for the deposition of very uniform and consistent thin films.
- Versatility: Sputtering can be used to deposit a wide variety of materials, including metals, ceramics, and alloys, onto different types of substrates.
- Adhesion: Films deposited via sputtering typically have excellent adhesion to the substrate, ensuring durability and reliability.
-
Challenges and Considerations:
- Cost: While sputtering is generally cost-effective, the need for high-purity targets and precise control of process parameters can increase costs.
- Complexity: The process requires sophisticated equipment and careful control of conditions such as pressure, temperature, and voltage.
- Material Limitations: Some materials may not be suitable for sputtering due to their physical or chemical properties.
In summary, sputtering is a critical technique in semiconductor manufacturing, enabling the deposition of high-quality, uniform, and pure thin films essential for the performance of semiconductor devices. Its ability to precisely control film properties makes it indispensable in the production of advanced electronic components.
Summary Table:
Aspect | Details |
---|---|
Definition | A PVD process where high-energy ions eject atoms from a target, depositing them onto a substrate. |
Mechanism | Inert gas (argon) ionized and accelerated to bombard the target, ejecting atoms. |
Key Steps | Vacuum creation, inert gas introduction, heating, magnetic field creation, ionization, and deposition. |
Applications | Depositing metals like gold for semiconductor electrical and thermal conductivity. |
Advantages | High purity, uniformity, versatility, and excellent adhesion. |
Challenges | Cost, complexity, and material limitations. |
Discover how sputtering can optimize your semiconductor manufacturing—contact our experts today!