Sputtering is a physical process used to deposit thin films of material onto a substrate. It involves bombarding a target material with high-energy ions, typically from an inert gas like argon, in a vacuum chamber. The ions collide with the target, causing atoms or molecules to be ejected from its surface. These ejected particles then travel through the vacuum and deposit onto a substrate, forming a thin, uniform, and highly adherent film. Sputtering is widely used in industries such as semiconductors, optics, and coatings due to its precision, ability to produce high-purity films, and versatility in working with various materials.
Key Points Explained:
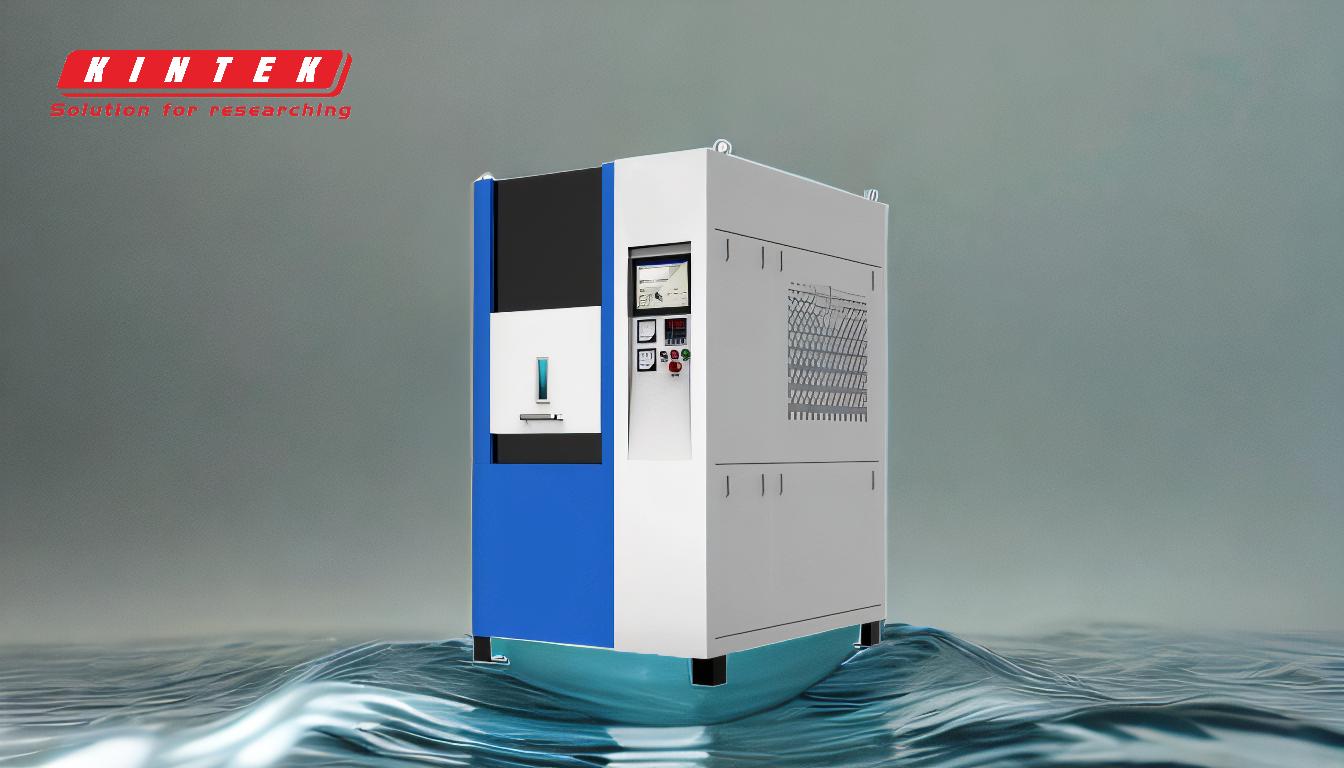
-
Definition of Sputtering:
- Sputtering is a process where high-energy ions bombard a target material, causing atoms or molecules to be ejected from its surface. These ejected particles then deposit onto a substrate, forming a thin film.
-
Key Components of the Process:
- Target Material: The material to be deposited, typically in solid form, placed in the vacuum chamber.
- Substrate: The surface onto which the ejected particles are deposited to form the thin film.
- Inert Gas: Usually argon or xenon, ionized to create the plasma that bombards the target.
- Vacuum Chamber: The environment where the process occurs, ensuring minimal interference from other molecules.
-
The Role of Ions and Plasma:
- A negative electrical potential is applied to the target, creating a plasma of ionized gas atoms.
- These ions are accelerated toward the target, colliding with its surface and transferring energy.
- The energy transfer causes target atoms to be ejected, a process known as sputtering.
-
Momentum Transfer and Ejection:
- When high-energy ions collide with the target, they create a cascade of collisions within the target material.
- If the energy transferred exceeds the bonding energy of the target atoms, the atoms are ejected from the surface.
-
Deposition of Thin Films:
- The ejected atoms travel through the vacuum and deposit onto the substrate.
- The deposited atoms bond at an atomic level, creating a thin, uniform, and highly adherent film.
-
Applications of Sputtering:
- Semiconductors: Used to deposit thin films of metals, oxides, and other materials in integrated circuits.
- Optics: Creates anti-reflective, reflective, or conductive coatings on lenses and mirrors.
- Coatings: Produces wear-resistant, decorative, or functional coatings on various surfaces.
-
Advantages of Sputtering:
- High Precision: Allows for the deposition of extremely thin and uniform films.
- Versatility: Can be used with a wide range of materials, including metals, oxides, and alloys.
- High Purity: Produces films with minimal contamination due to the controlled vacuum environment.
-
Process Conditions:
- Vacuum Environment: Essential to prevent contamination and ensure the efficient travel of ejected particles.
- Inert Gas: Typically argon, due to its inert nature and ability to form stable ions.
- Controlled Energy: The energy of the ions must be carefully controlled to optimize the sputtering process.
-
Types of Sputtering:
- DC Sputtering: Uses a direct current to ionize the gas and bombard the target.
- RF Sputtering: Uses radio frequency for non-conductive targets.
- Magnetron Sputtering: Enhances efficiency by using magnetic fields to confine electrons near the target.
-
Importance in Modern Technology:
- Sputtering is crucial for the production of precision components in electronics, optics, and advanced materials.
- It enables the creation of high-performance coatings and thin films that are essential in modern manufacturing.
By understanding these key points, one can appreciate the complexity and importance of sputtering in various high-tech industries. The process's ability to produce high-quality, uniform thin films makes it indispensable in the development of advanced materials and devices.
Summary Table:
Aspect | Details |
---|---|
Definition | High-energy ions bombard a target, ejecting atoms to form a thin film. |
Key Components | Target material, substrate, inert gas (e.g., argon), vacuum chamber. |
Applications | Semiconductors, optics, wear-resistant coatings. |
Advantages | High precision, versatility, high-purity films. |
Types | DC Sputtering, RF Sputtering, Magnetron Sputtering. |
Importance | Essential for precision components in electronics and advanced materials. |
Interested in how sputtering can enhance your manufacturing process? Contact us today to learn more!