Step coverage in physical vapor deposition (PVD) refers to the ability of a deposited thin film to uniformly cover all surfaces of a substrate, including any steps, trenches, or other three-dimensional features. This is a critical factor in semiconductor manufacturing and other applications where precise and uniform film thickness is required across complex geometries. Poor step coverage can lead to incomplete coverage in recessed areas, which can compromise the performance and reliability of the final product. Understanding step coverage involves examining the deposition process, the material properties, and the geometry of the substrate.
Key Points Explained:
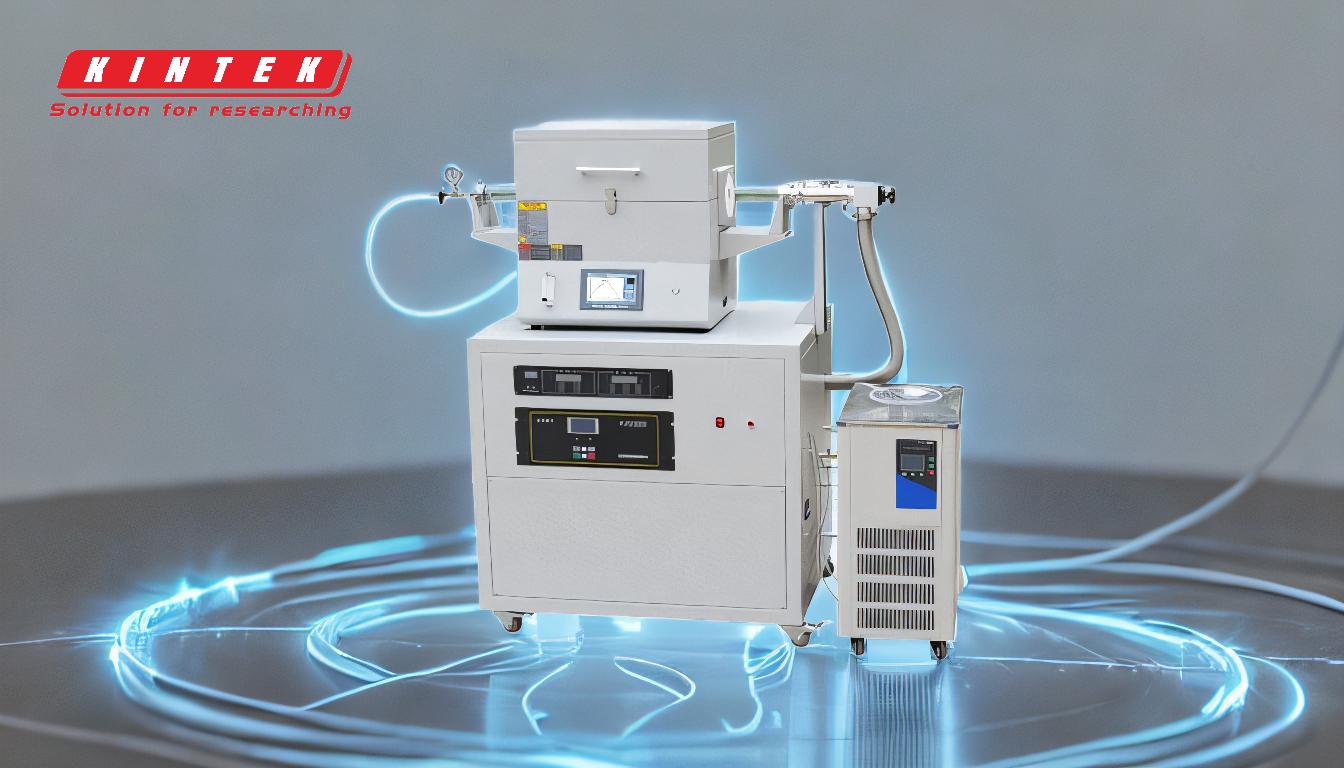
-
Definition of Step Coverage:
- Step coverage is a measure of how well a thin film deposited via PVD conforms to the topography of the substrate. It is typically expressed as the ratio of the film thickness at the bottom of a trench or step to the film thickness on the top surface.
- Good step coverage ensures that the film is uniformly thick across all features, which is essential for the functionality of devices like integrated circuits.
-
Factors Influencing Step Coverage:
- Deposition Angle: The angle at which material is deposited onto the substrate plays a significant role. Materials deposited at oblique angles may not reach the bottom of deep trenches, leading to poor step coverage.
- Material Properties: The properties of the material being deposited, such as its sticking coefficient and surface mobility, affect how well it adheres to and spreads across the substrate.
- Substrate Geometry: The shape and size of the features on the substrate, such as the aspect ratio of trenches, directly impact step coverage. High aspect ratio features are more challenging to cover uniformly.
-
PVD Techniques and Step Coverage:
- Sputtering: In sputtering, atoms are ejected from a target material and deposited onto the substrate. The step coverage in sputtering can be influenced by the energy of the sputtered atoms and the pressure in the deposition chamber.
- Evaporation: In evaporation, the material is heated until it vaporizes and then condenses onto the substrate. This method often results in poorer step coverage compared to sputtering, especially for high aspect ratio features.
-
Improving Step Coverage:
- Rotating the Substrate: Rotating the substrate during deposition can help achieve more uniform coverage by exposing all sides of the features to the vapor flux.
- Using Collimated Sputtering: Collimators can be used to direct the flow of sputtered atoms more precisely, improving coverage in deep trenches.
- Adjusting Process Parameters: Optimizing parameters such as deposition rate, pressure, and temperature can enhance step coverage.
-
Applications and Importance:
- Step coverage is crucial in the fabrication of microelectronic devices, where uniform thin films are necessary for the proper functioning of transistors, interconnects, and other components.
- It is also important in other applications, such as optical coatings and protective layers, where consistent film thickness is required for performance and durability.
Understanding and controlling step coverage in PVD processes is essential for producing high-quality thin films in advanced manufacturing applications. By considering the factors that influence step coverage and employing techniques to improve it, manufacturers can achieve the desired film uniformity and performance.
Summary Table:
Aspect | Details |
---|---|
Definition | Ratio of film thickness at the bottom of a trench to the top surface. |
Key Factors | Deposition angle, material properties, and substrate geometry. |
PVD Techniques | Sputtering (better for high aspect ratios) vs. evaporation (poorer coverage). |
Improvement Methods | Rotating substrate, collimated sputtering, and optimizing process parameters. |
Applications | Microelectronics, optical coatings, and protective layers. |
Need help achieving perfect step coverage in your PVD process? Contact our experts today!