System temperature control refers to the process of maintaining a device or environment at a desired temperature using automated systems. It involves the use of sensors, actuators, and control mechanisms to ensure precise and stable temperature regulation. This is crucial for applications involving sensitive equipment, such as optics, lasers, biological samples, or industrial processes like furnace operations. The system typically employs thermoelectric (Peltier) devices for precise control and thermocouples or infrared instruments for temperature measurement, depending on the temperature range. The system can automatically switch between high and low-temperature modes and provides real-time monitoring to ensure optimal performance.
Key Points Explained:
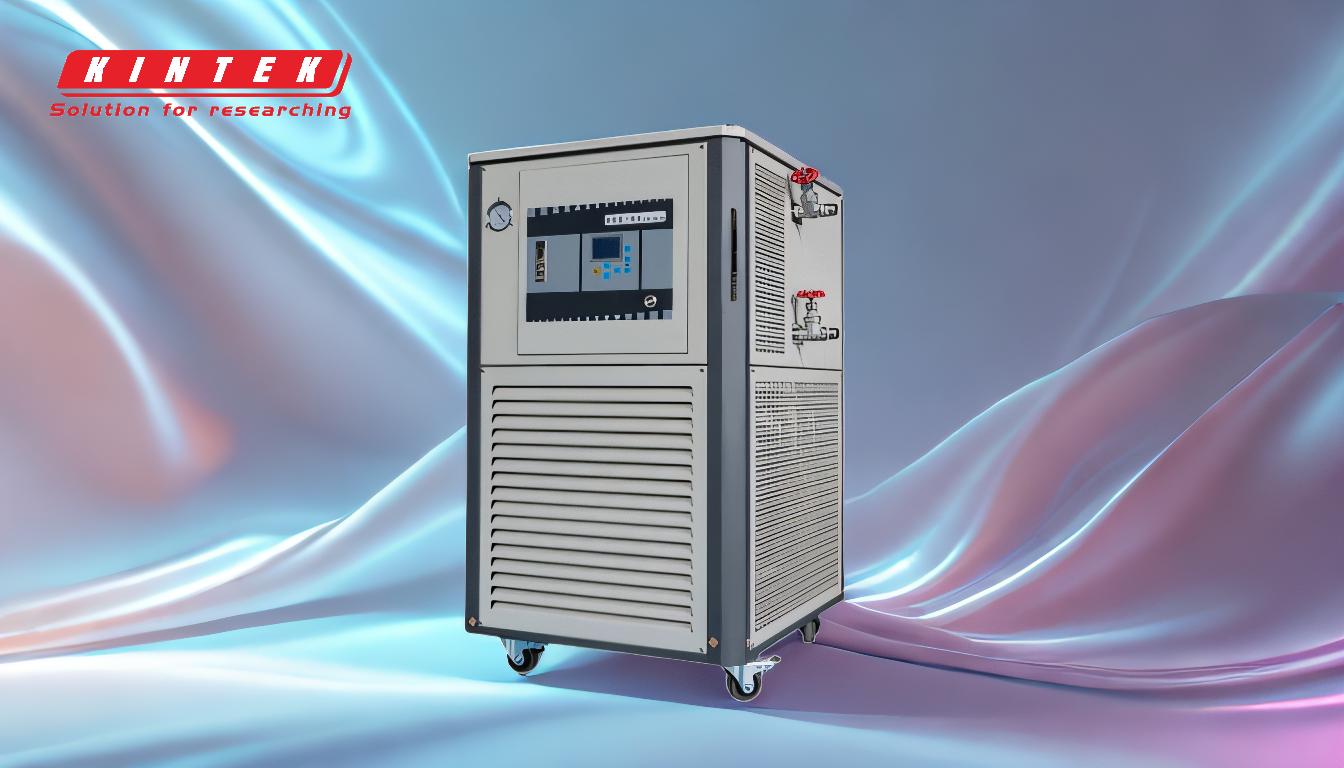
-
Purpose of System Temperature Control:
- The primary goal is to maintain a device or environment at a constant, desired temperature.
- This is essential for applications where temperature fluctuations could negatively impact performance, such as in optics, lasers, biological samples, or industrial processes.
-
Components of a Temperature Control System:
-
Sensors: Devices like thermocouples or infrared instruments measure the temperature.
- Thermocouples are used for temperatures below 1700°C.
- Infrared instruments are employed for temperatures above 1700°C.
-
Actuators: Devices like thermoelectric (Peltier) modules adjust the temperature.
- Peltier devices are commonly used for precise temperature control in sensitive applications.
- Control Mechanisms: These systems automatically adjust the actuators based on sensor feedback to maintain the desired temperature.
-
Sensors: Devices like thermocouples or infrared instruments measure the temperature.
-
Temperature Ranges and Automatic Conversion:
- The system supports both high and low-temperature ranges.
- It can automatically switch between these ranges, ensuring optimal performance across different operating conditions.
-
Real-Time Monitoring:
- The system provides continuous monitoring of temperature and furnace conditions.
- This allows for immediate adjustments and ensures stability and accuracy in temperature control.
-
Applications:
- Scientific Research: Maintaining precise temperatures for experiments involving lasers, optics, or biological samples.
- Industrial Processes: Regulating furnace temperatures in manufacturing or materials processing.
- Electronics: Cooling or heating sensitive electronic components to ensure proper functioning.
By integrating these components and features, a system temperature control setup ensures reliable and precise temperature regulation, critical for both scientific and industrial applications.
Summary Table:
Key Aspect | Details |
---|---|
Purpose | Maintain a device or environment at a constant, desired temperature. |
Components | Sensors (thermocouples, infrared), Actuators (Peltier), Control Mechanisms. |
Temperature Ranges | Supports high and low ranges with automatic switching. |
Real-Time Monitoring | Continuous monitoring for immediate adjustments and stability. |
Applications | Scientific research, industrial processes, electronics. |
Ensure precise temperature control for your applications—contact us today to learn more!