Electron beam welding (EBW) offers several advantages, making it a preferred choice for specific applications. It provides a high depth-to-width ratio, enabling deep and narrow welds without the need for multiple passes, which enhances precision and efficiency. The process generates minimal heat, reducing shrinkage and distortion, and allowing welding near heat-sensitive components. Additionally, EBW produces high-quality welds with excellent surface finishes and narrow kerf widths, making it suitable for high-value products. Despite its high equipment costs, the benefits of precision, reduced thermal impact, and superior weld quality make EBW advantageous for industries requiring high-performance welding.
Key Points Explained:
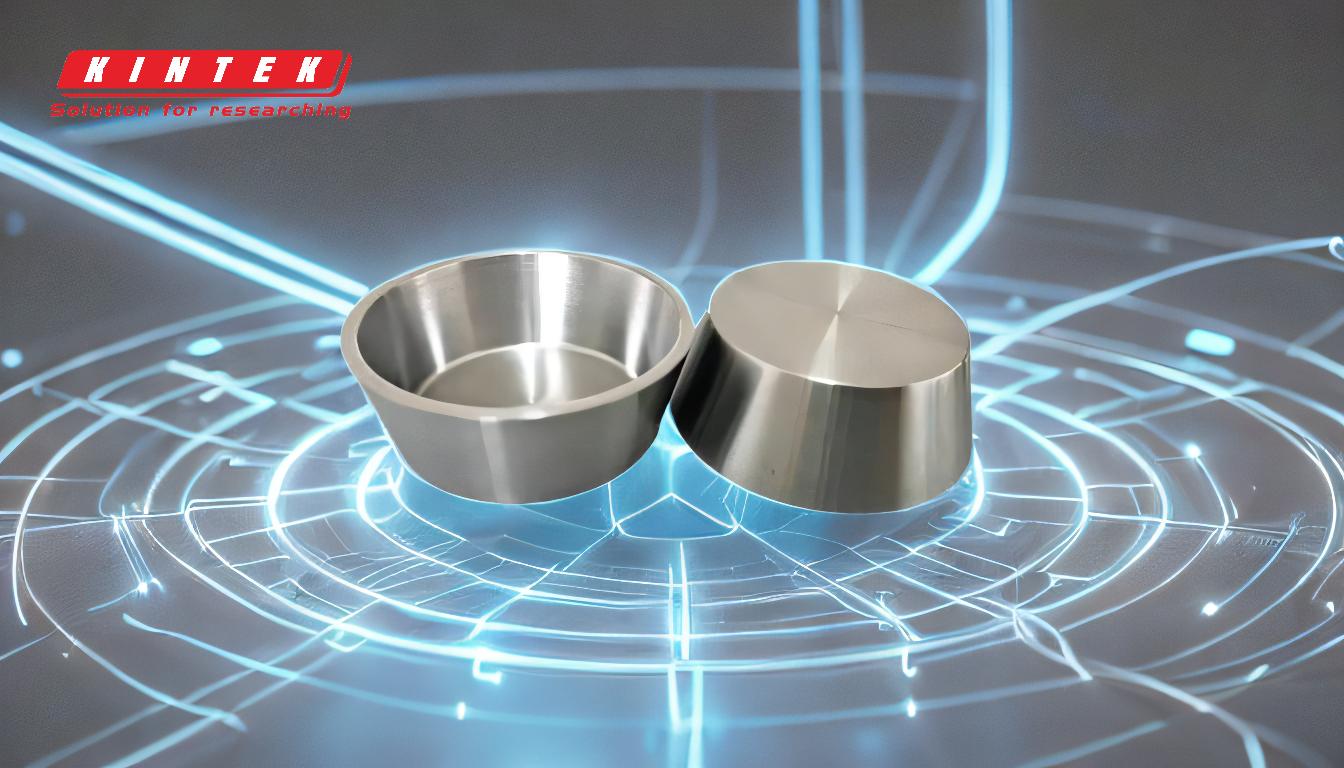
-
High Depth-to-Width Ratio:
- Explanation: Electron beam welding creates welds with a high depth-to-width ratio, meaning the weld can be very deep relative to its width. This eliminates the need for multiple-pass welds, which are often required in traditional welding methods.
- Advantage: This feature allows for precise and efficient welding, especially in applications where deep penetration is necessary, such as in aerospace or automotive industries.
-
Low Heat Input:
- Explanation: EBW generates minimal heat during the welding process. This low heat input reduces the risk of shrinkage and distortion in the welded materials.
- Advantage: The reduced thermal impact makes EBW suitable for welding near heat-sensitive components, such as electronic parts or materials with low melting points, without compromising their integrity.
-
Superior Weld Quality:
- Explanation: The process produces high-quality welds with excellent surface finishes and narrow kerf widths. The high-velocity electron beam ensures precise material vaporization and fusion.
- Advantage: The superior weld quality is crucial for high-value products where precision and reliability are paramount, such as in medical devices or precision engineering.
-
Versatility in Material Compatibility:
- Explanation: EBW can accurately cut or bore a wide variety of metals, including those that are difficult to weld using traditional methods.
- Advantage: This versatility allows for the welding of dissimilar metals and complex geometries, expanding the range of applications in various industries.
-
Cost-Effectiveness for High-Volume Applications:
- Explanation: While the initial equipment costs are high, EBW can be more cost-effective in high-volume commercial applications due to its rapid processing capabilities and the use of less expensive evaporative materials.
- Advantage: For industries requiring large-scale production, such as automotive or consumer electronics, EBW can offer significant cost savings over time.
-
Reduced Post-Welding Processing:
- Explanation: The precision and quality of EBW often eliminate the need for extensive post-welding processing, such as grinding or finishing.
- Advantage: This reduces overall production time and costs, making the process more efficient and appealing for manufacturers.
In summary, electron beam welding provides distinct advantages in terms of precision, thermal management, weld quality, material compatibility, and cost-effectiveness for high-volume applications. These benefits make it an invaluable technique in industries where high-performance welding is critical.
Summary Table:
Advantage | Explanation | Benefit |
---|---|---|
High Depth-to-Width Ratio | Enables deep, narrow welds without multiple passes | Enhances precision and efficiency in industries like aerospace and automotive |
Low Heat Input | Generates minimal heat, reducing shrinkage and distortion | Ideal for welding near heat-sensitive components |
Superior Weld Quality | Produces high-quality welds with excellent surface finishes and narrow kerf widths | Critical for high-value products like medical devices |
Versatility in Material Compatibility | Welds a wide variety of metals, including dissimilar metals and complex geometries | Expands application range across industries |
Cost-Effectiveness for High-Volume Applications | High initial costs offset by rapid processing and reduced material expenses | Offers significant savings in large-scale production |
Reduced Post-Welding Processing | Eliminates the need for extensive finishing or grinding | Reduces production time and costs |
Learn how electron beam welding can transform your manufacturing process—contact us today for expert guidance!