Vacuum hardening, particularly when performed in a vacuum hardening furnace, offers numerous advantages that make it a preferred method for heat treatment in various industries. The process involves heating materials in a vacuum environment, which eliminates contamination from gases like oxygen and carbon, ensures uniform temperature distribution, and allows for precise control over the hardening process. This results in improved mechanical properties, enhanced product quality, and repeatable outcomes. Additionally, vacuum hardening minimizes environmental pollution and supports energy-efficient operations. Below, the key advantages are explained in detail.
Key Points Explained:
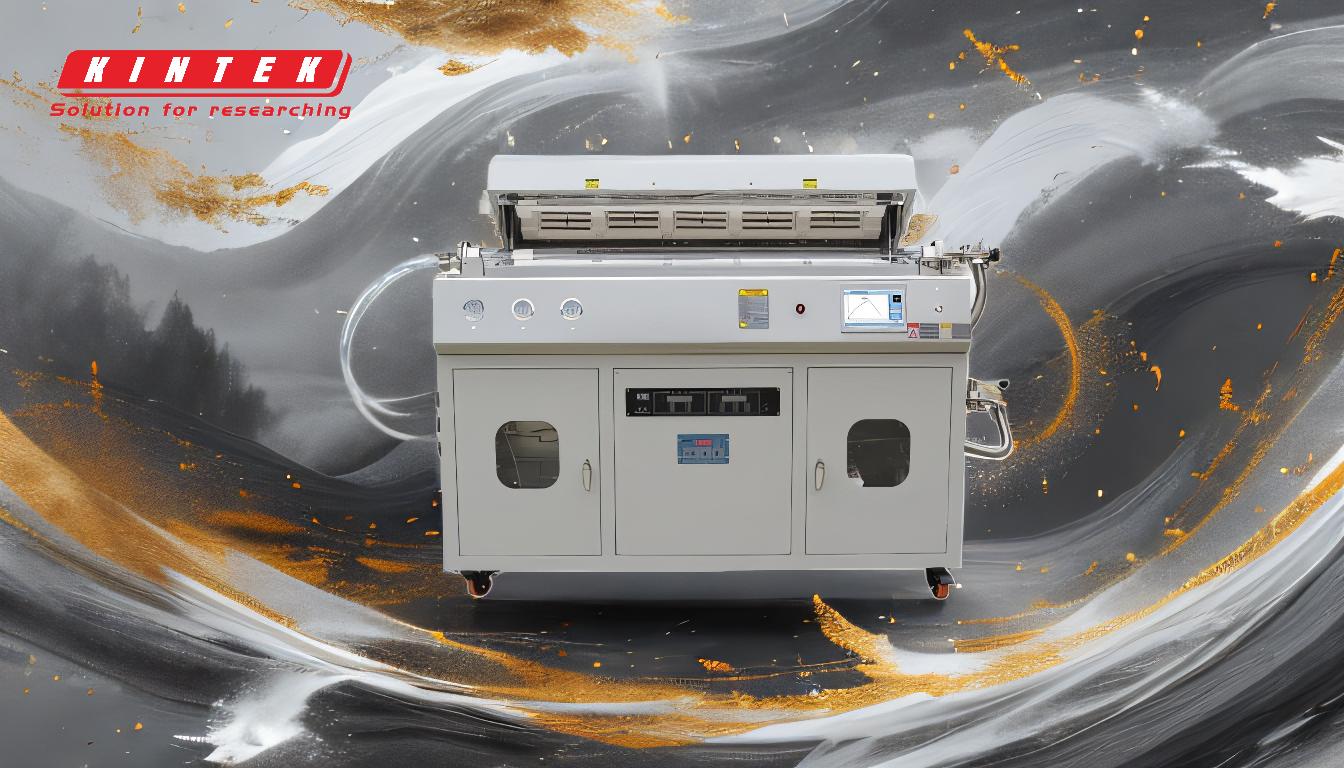
-
Uniform Temperature Distribution and Precise Control
- Vacuum hardening furnaces provide uniform temperatures across a wide range, typically between 1100–1500°C (2000–2800°F). This ensures consistent heating throughout the material, reducing the risk of uneven hardening or distortion.
- Precise temperature control within the heating zone allows for accurate regulation of the hardening process, ensuring optimal metallurgical properties and repeatability.
-
Low Contamination and High Purity
- The vacuum environment eliminates exposure to reactive gases like oxygen, carbon, and nitrogen, which can contaminate the material and degrade its quality. This results in a cleaner, higher-purity product with fewer imperfections.
- By removing byproducts through vacuum pumping systems, the process ensures that the treated materials maintain their integrity and performance characteristics.
-
Improved Mechanical Properties
- Vacuum hardening enhances the chemical and mechanical properties of metals, such as hardness, elasticity, and shear strength. This makes the materials more resistant to wear, corrosion, and fatigue.
- The process also preserves dimensional stability, preventing warping or distortion that can occur in other heat treatment methods.
-
Rapid Cooling (Quenching) and Reduced Cycle Time
- Vacuum furnaces support rapid cooling (quenching), which shortens the overall process cycle time. This is particularly beneficial for high-volume production environments.
- The ability to control the cooling rate ensures that the material achieves the desired microstructure and mechanical properties.
-
Computer-Controlled Processes for Repeatability
- Modern vacuum hardening furnaces are equipped with advanced computer control systems, enabling precise regulation of temperature, pressure, and cooling rates.
- This ensures metallurgical repeatability, allowing manufacturers to produce consistent, high-quality components batch after batch.
-
Versatility in Heat Treatment Applications
- Vacuum hardening furnaces are versatile and can be used for various heat treatment processes, including annealing, brazing, sintering, and tempering. This flexibility makes them suitable for a wide range of materials and applications.
-
Energy Efficiency and Environmental Benefits
- Vacuum furnaces are designed with advanced insulation materials and control systems that minimize heat loss and optimize energy consumption.
- The process generates little to no pollution, making it an environmentally friendly option compared to traditional heat treatment methods.
-
No Oxidation and Clean Surface Finish
- The absence of oxygen in the vacuum environment prevents oxidation, ensuring that the treated materials retain a bright, clean surface finish.
- This is particularly important for components used in industries like aerospace, medical devices, and electronics, where surface quality is critical.
In summary, vacuum hardening in a vacuum hardening furnace offers significant advantages, including uniform heating, low contamination, improved mechanical properties, rapid cooling, and environmental sustainability. These benefits make it an ideal choice for industries requiring high-performance materials with consistent quality and reliability.
Summary Table:
Advantage | Key Benefit |
---|---|
Uniform Temperature Distribution | Ensures consistent heating, reducing uneven hardening or distortion. |
Low Contamination | Eliminates exposure to reactive gases, resulting in high-purity materials. |
Improved Mechanical Properties | Enhances hardness, elasticity, and resistance to wear, corrosion, and fatigue. |
Rapid Cooling (Quenching) | Shortens cycle time and ensures desired microstructure. |
Computer-Controlled Processes | Ensures repeatability and consistent high-quality outcomes. |
Versatility | Suitable for annealing, brazing, sintering, and tempering processes. |
Energy Efficiency | Minimizes heat loss and reduces energy consumption. |
No Oxidation | Prevents oxidation, ensuring a clean surface finish. |
Ready to enhance your heat treatment process? Contact our experts today to learn more about vacuum hardening solutions!