The atmosphere of an annealing furnace, particularly a vacuum annealing furnace, plays a critical role in determining the quality and properties of the treated materials. It is designed to either protect the material from oxidation or to facilitate surface changes, such as carburizing or nitriding. In vacuum annealing furnaces, high-purity inert gases like nitrogen or argon are commonly used to create a protective atmosphere, ensuring minimal contamination and oxidation. Additionally, these furnaces can operate under high vacuum conditions, which are ideal for high-precision applications. The choice of atmosphere depends on the material being treated and the desired outcome of the annealing process.
Key Points Explained:
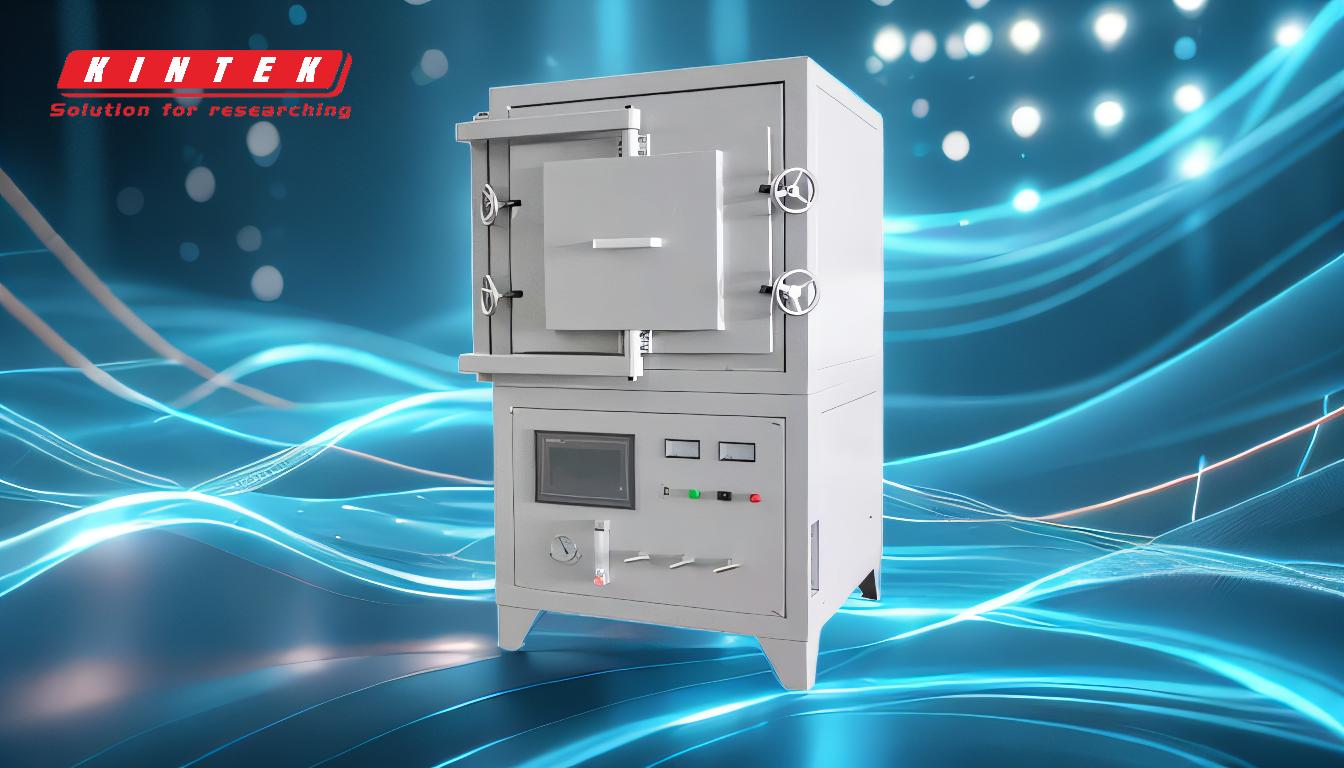
-
Purpose of Furnace Atmosphere:
- The atmosphere in an annealing furnace serves two primary purposes:
- Protection from Oxidation: Chemically inert atmospheres, such as nitrogen or argon, prevent oxidation and other chemical reactions that could degrade the material.
- Surface Modification: Chemically active atmospheres, such as those containing hydrogen or carbon monoxide, can alter the surface properties of the material, such as adding carbon or nitrogen.
- The atmosphere in an annealing furnace serves two primary purposes:
-
Common Atmospheres in Annealing Furnaces:
- Nitrogen-Based Atmospheres: Nitrogen is widely used because it is inexpensive, dry, and inert at high temperatures. It is particularly effective for materials like aluminum.
- Reducing Gas Atmospheres: For metals prone to oxidation, reducing gases like hydrogen or carbon monoxide are added to react with oxygen, preventing oxidation.
- High-Purity Inert Gas: In vacuum annealing, high-purity inert gases (e.g., argon or nitrogen) with purity levels exceeding 99.99% are used to ensure a contamination-free environment.
-
Vacuum Annealing Furnace Atmosphere:
- A vacuum annealing furnace operates under high vacuum conditions, typically at pressures less than 10^-3 Torr, to eliminate oxidation and contamination.
- It is often used for high-precision components like stainless steel parts, bearings, and cutting tools, where even minor contamination can compromise performance.
- The protective atmosphere in these furnaces is maintained using high-purity inert gases, with a pressure range of 0.05 to 0.07 MPa.
-
Applications of Vacuum Annealing:
- Vacuum annealing is ideal for applications requiring high precision and minimal contamination, such as:
- Stainless steel deep-drawing parts (e.g., plumbing equipment).
- Stainless steel bearings and cutting tools.
- Self-tapping screws and dowels.
- The process ensures that the material retains its mechanical properties and surface finish.
- Vacuum annealing is ideal for applications requiring high precision and minimal contamination, such as:
-
Furnace Design and Operation:
- A vacuum annealing furnace typically consists of a heating furnace hood and a mobile chassis.
- The furnace hood is equipped with a crane for material handling and a pneumatic or electric-operated furnace door.
- The mobile chassis includes a quenching water tank and a material basket, facilitating efficient processing.
-
Temperature Control in Annealing Furnaces:
- Temperature regulation is critical in annealing furnaces. Advanced systems use thyristor voltage regulators for heater power supply and imported temperature controllers for precise temperature management.
- This ensures consistent heating and cooling rates, which are essential for achieving the desired material properties.
By understanding the role of the atmosphere in annealing furnaces, particularly in vacuum annealing furnaces, manufacturers can select the appropriate conditions to achieve optimal results for their specific applications.
Summary Table:
Aspect | Details |
---|---|
Purpose of Atmosphere | - Protection from oxidation (inert gases like nitrogen, argon). |
- Surface modification (active gases like hydrogen, carbon monoxide). | |
Common Atmospheres | - Nitrogen-based: Cost-effective, inert, ideal for aluminum. |
- Reducing gases: Hydrogen or CO to prevent oxidation. | |
- High-purity inert gases: Argon or nitrogen (>99.99% purity). | |
Vacuum Annealing | - Operates under high vacuum (<10^-3 Torr) for minimal contamination. |
- Uses high-purity inert gases (0.05–0.07 MPa) for precision applications. | |
Applications | - Stainless steel parts, bearings, cutting tools, and self-tapping screws. |
Furnace Design | - Heating furnace hood, mobile chassis, quenching water tank, material basket. |
Temperature Control | - Advanced systems with thyristor voltage regulators and precise controllers. |
Discover the ideal annealing furnace atmosphere for your materials—contact our experts today!