An electric arc furnace (EAF) operates on the principle of using an electric arc to generate heat for melting metal. The process involves three-phase electric current, which forms an arc between graphitized electrodes and the metal charge. This arc produces intense heat, melting the metal. The process includes stages such as charging the furnace with scrap metal, preheating, melting, and refining. Additives like burnt lime and spar are used to accelerate slag formation, while the roof swings open for charging, and electrodes are adjusted to control the arc. The voltage is increased to speed up melting, and impurities like carbon, silicon, and manganese are oxidized during the process.
Key Points Explained:
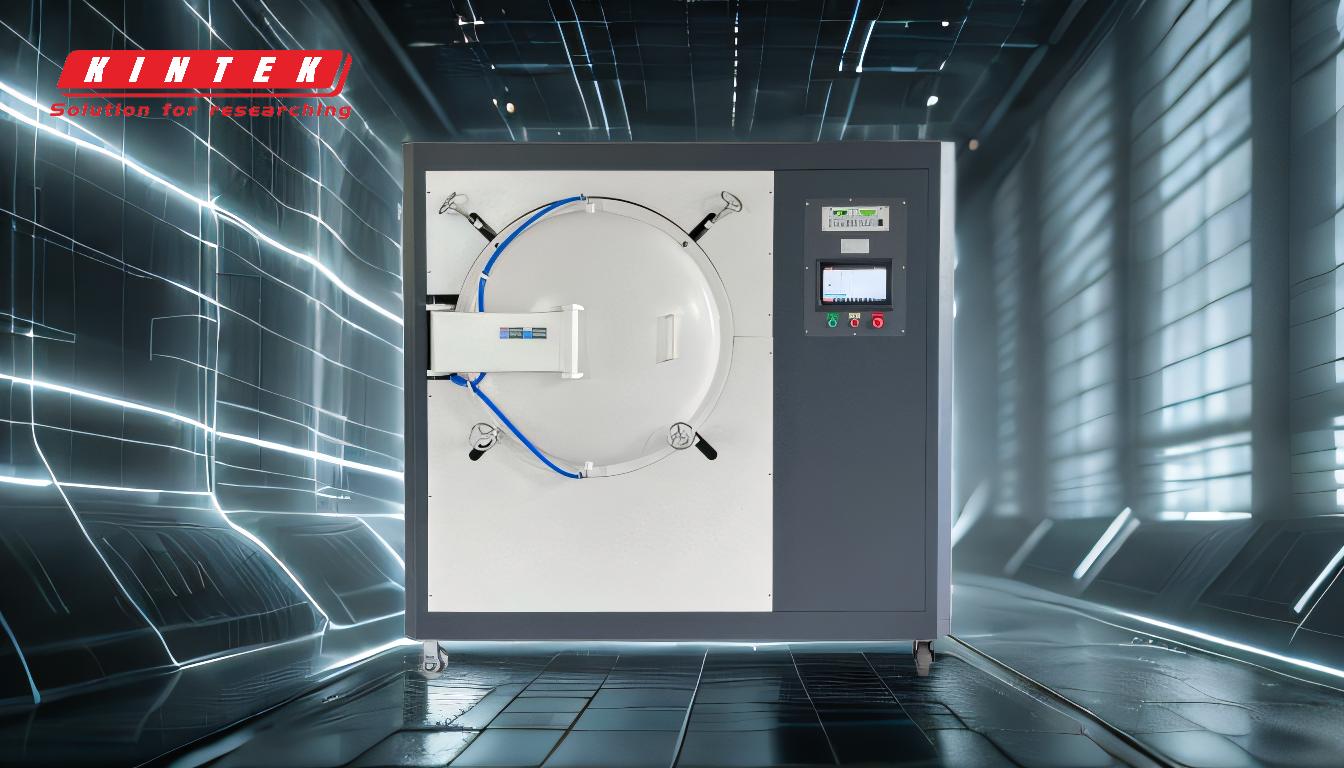
-
Three-Phase Electric Current:
- Electric arc furnaces operate on three-phase electric current, which provides a stable and efficient power supply for generating the electric arc.
- This type of current ensures consistent energy delivery, which is crucial for maintaining the high temperatures needed for metal melting.
-
Electric Arc Formation:
- The core principle of an EAF is the formation of an electric arc between graphitized electrodes and the metal charge.
- The arc generates temperatures high enough to melt the metal, typically reaching up to 3,000°C (5,432°F).
-
Charging the Furnace:
- The furnace is charged with a mixture of heavy and light scrap metal, often preheated using exhaust gases to improve energy efficiency.
- The roof of the furnace swings open to allow the scrap metal to be loaded into the furnace in a large basket.
-
Meltdown Period:
- Once the furnace is charged, the electrodes are lowered onto the scrap metal to produce the electric arc.
- The voltage is increased to accelerate the melting process, ensuring that the metal reaches its molten state quickly.
-
Refining Process:
- During the melting process, impurities such as carbon, silicon, and manganese are oxidized and removed from the metal.
- Additives like burnt lime and spar are introduced to speed up the formation of slag, which helps in the removal of impurities.
-
Electrode Adjustment:
- The electrodes are continuously adjusted to maintain the optimal arc length and ensure efficient heat transfer.
- Proper electrode management is crucial for controlling the melting process and minimizing energy consumption.
-
Energy Efficiency:
- Preheating the scrap metal with exhaust gases and optimizing the arc voltage are key strategies for improving the energy efficiency of the EAF.
- These practices help reduce the overall energy consumption and operational costs of the furnace.
-
Slag Formation:
- Slag, a byproduct of the refining process, is formed by the reaction of additives with impurities in the metal.
- The slag floats on top of the molten metal and is removed periodically to ensure the purity of the final product.
-
Temperature Control:
- Maintaining the correct temperature is essential for the quality of the molten metal.
- The EAF is equipped with sensors and control systems to monitor and regulate the temperature throughout the melting and refining process.
-
Final Product:
- The end result of the EAF process is high-quality molten metal, ready for casting or further processing.
- The efficiency and precision of the EAF make it a preferred choice for recycling scrap metal and producing high-grade steel.
By understanding these key points, one can appreciate the complexity and efficiency of the electric arc furnace process, which plays a crucial role in modern metal production and recycling.
Summary Table:
Key Aspect | Description |
---|---|
Three-Phase Current | Provides stable, efficient power for generating electric arcs. |
Electric Arc Formation | Generates intense heat (up to 3,000°C) to melt metal. |
Charging the Furnace | Scrap metal is loaded and preheated for energy efficiency. |
Meltdown Period | Voltage is increased to accelerate melting. |
Refining Process | Impurities are oxidized, and slag forms to remove contaminants. |
Electrode Adjustment | Electrodes are adjusted to optimize arc length and heat transfer. |
Energy Efficiency | Preheating scrap and optimizing voltage reduce energy consumption. |
Slag Formation | Additives like burnt lime and spar speed up slag formation for impurity removal. |
Temperature Control | Sensors and systems ensure precise temperature regulation. |
Final Product | High-quality molten metal ready for casting or further processing. |
Ready to optimize your metal production? Contact our experts today to learn more about electric arc furnaces!