The e-beam evaporation process is a sophisticated physical vapor deposition (PVD) technique used to create thin, high-purity coatings on substrates. It involves using a high-energy electron beam to heat and evaporate a source material, which then condenses onto a substrate in a vacuum chamber. This method is particularly effective for materials with high melting points, such as metals and alloys, and allows for precise control over coating thickness, typically ranging from 5 to 250 nanometers. The process is widely used in industries requiring high-purity, uniform coatings, such as semiconductors, optics, and aerospace.
Key Points Explained:
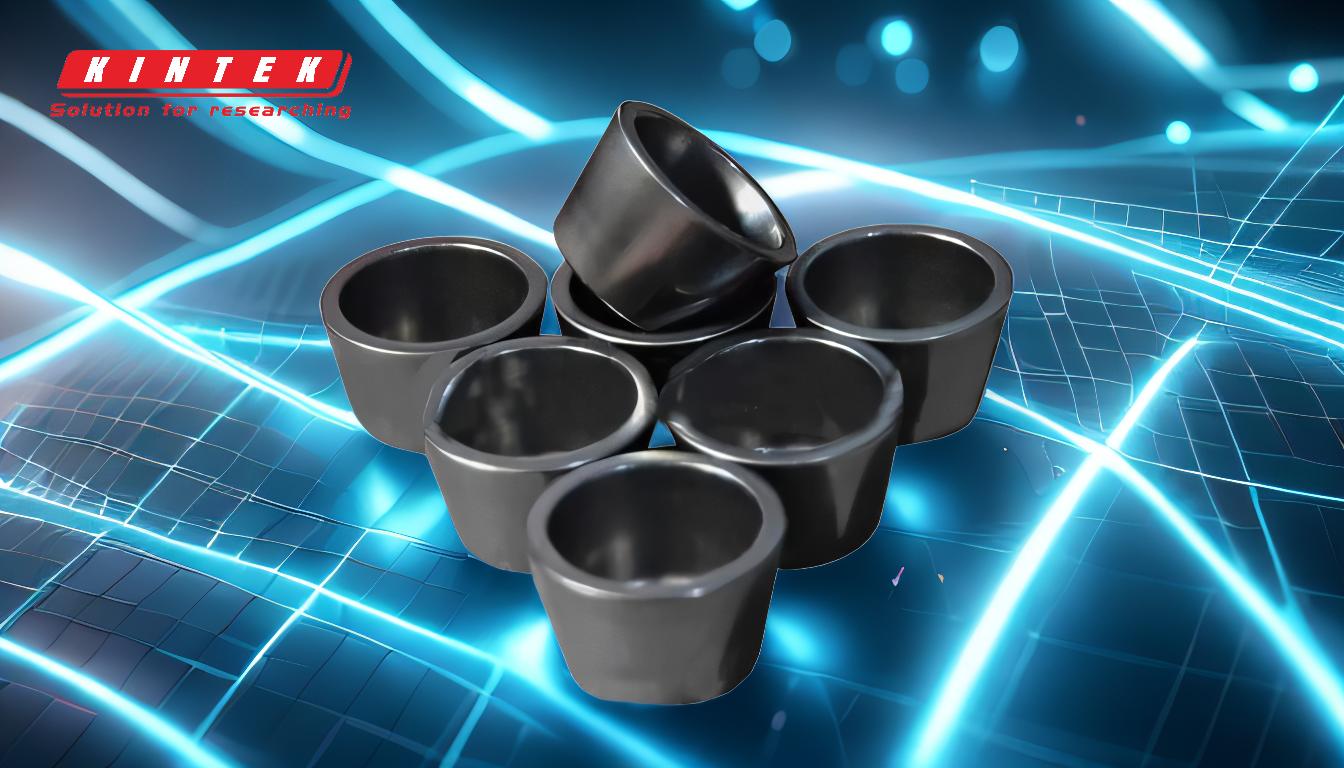
-
Electron Beam Generation and Acceleration:
- The process begins with the generation of electrons using a tungsten filament. When current is passed through the filament, it heats up and emits electrons through thermionic emission.
- These electrons are then accelerated towards the source material using a high-voltage electric field, typically in the range of several kilovolts. The high voltage ensures that the electrons gain sufficient energy to effectively heat the source material.
-
Focusing the Electron Beam:
- A magnetic field is used to focus the accelerated electrons into a narrow, concentrated beam. This focused beam is directed onto the surface of the source material contained in a crucible or water-cooled copper hearth.
- The focusing of the electron beam is crucial for achieving high energy density, which is necessary to evaporate materials with high melting points.
-
Heating and Evaporation of the Source Material:
- When the high-energy electron beam strikes the source material, it transfers a significant amount of energy, causing the material to heat up rapidly. Depending on the material, this energy transfer can lead to either evaporation or sublimation.
- The source material is typically placed in a crucible, which may be water-cooled to prevent contamination from impurities or unwanted reactions with the crucible material.
-
Vacuum Environment:
- The entire process takes place in a vacuum chamber to ensure that the evaporated particles travel unimpeded to the substrate. The vacuum environment minimizes collisions between evaporated particles and residual gas molecules, which could otherwise degrade the quality of the coating.
- A vacuum also prevents oxidation or contamination of the source material and the resulting thin film.
-
Deposition onto the Substrate:
- The evaporated particles travel upwards in the vacuum chamber and deposit onto the substrate, which is positioned above the source material. The substrate is typically held at a controlled temperature to ensure proper adhesion and film quality.
- The deposition process results in a thin, high-purity coating that can alter the substrate's properties, such as electrical conductivity, reflectivity, or corrosion resistance, without affecting its dimensional accuracy.
-
Control of Coating Thickness:
- The thickness of the deposited film is carefully controlled using quartz crystal microbalances. These devices monitor the deposition rate in real-time by measuring the change in mass as the film grows on the substrate.
- By adjusting parameters such as the electron beam current, acceleration voltage, and deposition time, the desired coating thickness, typically between 5 to 250 nanometers, can be achieved with high precision.
-
Advantages of E-Beam Evaporation:
- High Purity: The process produces coatings with very high purity, as the vacuum environment and controlled heating minimize contamination.
- High Melting Point Materials: E-beam evaporation is particularly suited for materials with high melting points, such as gold, platinum, and refractory metals, which are difficult to evaporate using traditional thermal methods.
- Uniform Coatings: The focused electron beam allows for uniform heating and evaporation, resulting in consistent film thickness and quality across the substrate.
- Multi-Layer Coatings: Many e-beam systems are equipped with multiple crucibles, enabling the deposition of multi-layer coatings or co-deposition of different materials without breaking the vacuum.
-
Applications:
- Semiconductors: E-beam evaporation is widely used in the semiconductor industry to deposit thin films of metals and alloys for interconnects, contacts, and other critical components.
- Optics: The process is used to create high-reflectivity coatings for mirrors, lenses, and other optical components.
- Aerospace: E-beam evaporation is employed to produce protective coatings that enhance the durability and performance of aerospace components.
- Research and Development: The technique is also used in R&D for developing new materials and coatings with tailored properties.
In summary, the e-beam evaporation process is a highly controlled and versatile method for depositing thin, high-purity coatings on substrates. Its ability to handle high melting point materials, produce uniform coatings, and operate in a vacuum environment makes it indispensable in various high-tech industries.
Summary Table:
Key Aspect | Details |
---|---|
Process Overview | Uses a high-energy electron beam to evaporate and deposit materials in a vacuum. |
Key Components | Tungsten filament, magnetic field, crucible, vacuum chamber, substrate. |
Coating Thickness | 5 to 250 nanometers, controlled with quartz crystal microbalances. |
Advantages | High purity, uniform coatings, handles high melting point materials. |
Applications | Semiconductors, optics, aerospace, R&D. |
Interested in high-purity coatings for your industry? Contact us today to learn more about e-beam evaporation solutions!