The best crucible for melting metal depends on the type of metal being melted, the melting temperature, and the specific application. Zirconia crucibles are highly regarded for their excellent thermal shock resistance, high melting point, and chemical inertness, making them suitable for melting high-temperature metals like platinum, palladium, and other precious metals. However, other materials like graphite, clay-graphite, and silicon carbide are also popular for different applications. Factors such as cost, durability, and compatibility with the metal being melted should be considered when selecting a crucible.
Key Points Explained:
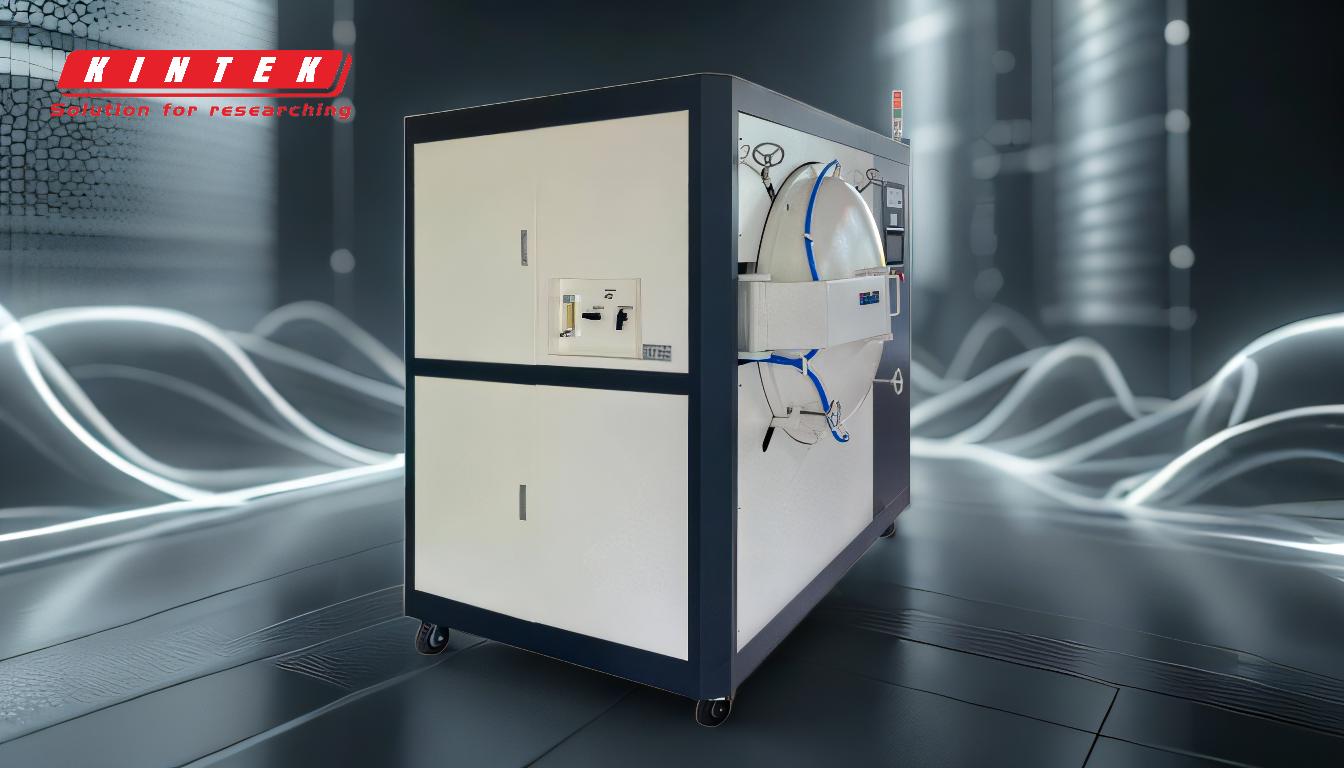
-
Crucible Materials and Their Properties:
- Zirconia Crucibles: These are ideal for high-temperature applications due to their exceptional thermal shock resistance and ability to withstand temperatures up to 2400°C. They are chemically inert, making them suitable for melting precious metals like platinum and palladium. Learn more about zirconia crucibles.
- Graphite Crucibles: These are commonly used for melting non-ferrous metals like aluminum, copper, and brass. They are cost-effective and have good thermal conductivity but are not suitable for high-temperature applications above 1200°C.
- Clay-Graphite Crucibles: These combine the properties of clay and graphite, offering better durability and resistance to oxidation. They are suitable for melting metals like gold, silver, and bronze.
- Silicon Carbide Crucibles: Known for their high thermal conductivity and resistance to thermal shock, these crucibles are ideal for melting metals like iron and steel at high temperatures.
-
Factors to Consider When Choosing a Crucible:
- Melting Temperature: The crucible material must withstand the melting point of the metal. For example, zirconia crucibles are suitable for high-temperature metals, while graphite crucibles are better for lower-temperature metals.
- Chemical Compatibility: The crucible should not react with the metal being melted. Zirconia crucibles are chemically inert, making them ideal for precious metals.
- Thermal Shock Resistance: This is crucial for applications involving rapid heating and cooling. Zirconia and silicon carbide crucibles excel in this regard.
- Durability and Lifespan: Consider the crucible's resistance to wear and tear. Clay-graphite crucibles are durable and cost-effective for frequent use.
- Cost: Zirconia crucibles are more expensive but offer superior performance for high-temperature applications. Graphite and clay-graphite crucibles are more affordable for general use.
-
Applications of Different Crucibles:
- Zirconia Crucibles: Used in laboratories and industries for melting precious metals and high-temperature alloys.
- Graphite Crucibles: Commonly used in foundries for melting non-ferrous metals like aluminum and copper.
- Clay-Graphite Crucibles: Suitable for jewelry making and small-scale metal casting.
- Silicon Carbide Crucibles: Ideal for industrial applications involving iron, steel, and other high-temperature metals.
-
Maintenance and Handling:
- Proper handling and maintenance can extend the lifespan of a crucible. Avoid sudden temperature changes, clean the crucible after each use, and store it in a dry place to prevent oxidation.
By considering these factors, you can select the best crucible for your specific metal-melting needs. Zirconia crucibles are an excellent choice for high-temperature and precious metal applications, while other materials like graphite and silicon carbide are better suited for different metals and industrial uses.
Summary Table:
Crucible Material | Best For | Max Temperature | Key Benefits |
---|---|---|---|
Zirconia Crucibles | Precious metals, high-temp alloys | 2400°C | Thermal shock resistance, chemical inertness |
Graphite Crucibles | Aluminum, copper, brass | 1200°C | Cost-effective, good thermal conductivity |
Clay-Graphite Crucibles | Gold, silver, bronze | 1200°C | Durable, oxidation-resistant |
Silicon Carbide Crucibles | Iron, steel, high-temp metals | 1600°C | High thermal conductivity, thermal shock resistance |
Need help selecting the right crucible for your metal-melting needs? Contact our experts today for personalized advice!