The body structure of a furnace is a critical component that ensures its functionality, durability, and efficiency. It typically consists of a robust outer shell, often made of stainless steel, with a double-layer structure to enhance strength and rigidity. The interior is lined with refractory materials to withstand high temperatures and thermal stress. The furnace body includes various functional components such as heating and cooling chambers, loading mechanisms, and specialized openings for electrodes, thermocouples, and observation. Advanced designs may incorporate water-cooling systems, vacuum sealing, and high-temperature-resistant materials like alumina fiber for improved performance. The structure is engineered to handle external forces and high temperatures without deformation, ensuring long-term reliability.
Key Points Explained:
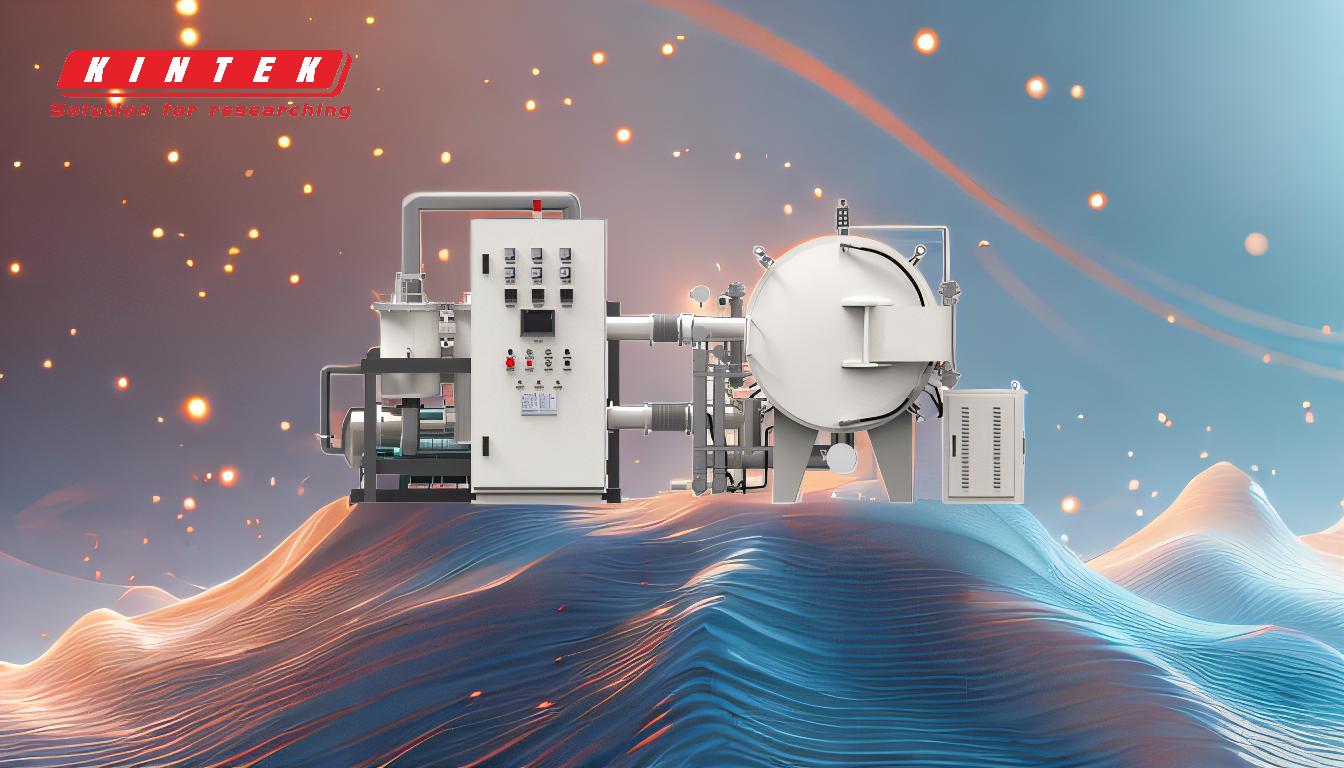
-
Material Composition:
- The furnace body is primarily constructed using stainless steel, specifically 304 stainless steel, known for its durability and resistance to corrosion.
- The outer surface is often mirror-polished to enhance its aesthetic and functional properties.
- The interior is lined with refractory materials such as magnesite bricks, stabilized dolomite blocks, or silica bricks, depending on whether the furnace operates under basic or acidic conditions.
-
Structural Design:
- The furnace body typically features a double-layer structure, divided into inner and outer barrel bodies. This design enhances strength and rigidity, allowing the furnace to withstand external forces and high temperatures without deformation.
- The furnace bottom head is often processed using a spinning process, ensuring uniformity and strength.
- Some designs incorporate a double-layer water sandwich structure, where both inner and outer walls are made of stainless steel, providing additional cooling and thermal management.
-
Functional Components:
- The furnace body includes various openings and holes for functional purposes, such as:
- Electrode holes for electrical connections.
- Suction holes and vent holes for air circulation and pressure management.
- Thermocouple holes for temperature monitoring.
- Infrared holes and observation holes for process monitoring and control.
- These components are typically made of stainless steel to ensure durability and resistance to high temperatures.
- The furnace body includes various openings and holes for functional purposes, such as:
-
Heating and Cooling Mechanisms:
- Furnaces are equipped with heating chambers and cooling chambers to manage thermal processes effectively.
- Advanced designs may include water-cooling devices to prevent overheating and protect sensitive components like vacuum seals and 'O' rings from aging due to excessive temperature.
-
Loading Mechanisms:
- The furnace body is designed to accommodate loading mechanisms, which facilitate the introduction and removal of materials during the heating process.
- These mechanisms are integrated into the overall structure to ensure smooth operation and efficiency.
-
Vacuum Sealing and Thermal Management:
- Some furnace bodies are designed with vacuum-sealed compartments, using 'O' rings to maintain airtight conditions.
- The inclusion of temperature measurement holes and air extraction holes allows for precise control of the internal environment, ensuring optimal thermal management.
-
High-Temperature Resistance:
- The furnace body may be constructed using high-purity alumina fiber materials, which offer excellent heat preservation and can withstand extremely high temperatures.
- This material choice enhances the furnace's ability to maintain consistent temperatures and improves overall energy efficiency.
-
Mounting and Stability:
- The furnace body is typically fixed on the upper part of the furnace frame, ensuring stability and alignment during operation.
- This mounting arrangement helps distribute the weight and forces evenly, reducing the risk of deformation or structural failure.
By understanding these key points, a purchaser can make informed decisions about the type of furnace that best meets their specific needs, considering factors such as material compatibility, thermal management, and structural integrity.
Summary Table:
Key Aspect | Details |
---|---|
Material Composition | Stainless steel (304), mirror-polished, refractory lining (magnesite, etc.) |
Structural Design | Double-layer structure, spinning-processed bottom head, water-cooling |
Functional Components | Electrode holes, thermocouple holes, observation holes, suction/vent holes |
Heating/Cooling Mechanisms | Heating/cooling chambers, water-cooling devices for thermal management |
Loading Mechanisms | Integrated loading systems for material handling |
Vacuum Sealing | Vacuum-sealed compartments with 'O' rings for airtight conditions |
High-Temperature Resistance | High-purity alumina fiber materials for heat preservation |
Mounting and Stability | Fixed on the furnace frame for stability and alignment |
Need a furnace tailored to your needs? Contact us today for expert advice and solutions!