Calibration of a vacuum refers to the process of ensuring that the vacuum system operates accurately and consistently within specified parameters. This involves verifying and adjusting the vacuum levels, pressure sensors, and other components to meet the required standards for specific applications, such as vacuum tempering, vacuum deposition coating, or vacuum furnace processes. Calibration ensures that the vacuum chamber maintains the desired environment, free from contaminants like air or gases, which is critical for achieving precise results in industrial processes.
Key Points Explained:
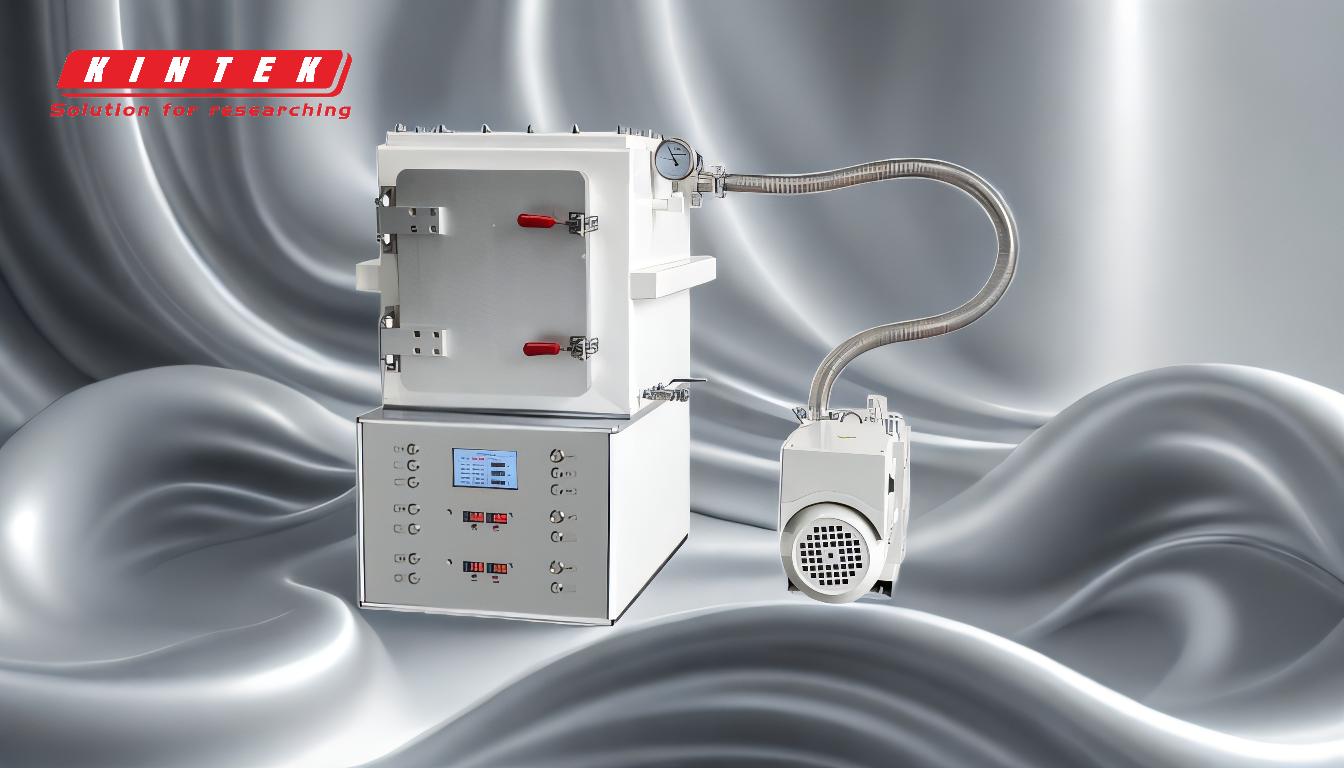
-
Understanding Vacuum Calibration:
- Vacuum calibration involves checking and adjusting the vacuum system to ensure it operates within the desired pressure range. This is crucial for processes like vacuum tempering and vacuum deposition coating, where even minor deviations can affect the quality of the final product.
- The calibration process typically includes verifying the accuracy of pressure sensors, vacuum gauges, and other monitoring equipment to ensure they provide reliable readings.
-
Importance of Vacuum Calibration:
- Precision in Processes: In vacuum tempering, for example, maintaining a precise vacuum ensures that the steel is heated and cooled uniformly, resulting in a balanced combination of hardness and ductility.
- Contamination Control: In vacuum deposition coating, a properly calibrated vacuum chamber eliminates air and gases that could interfere with the deposition process, ensuring a high-quality thin film.
- Consistency: Calibration ensures that the vacuum system operates consistently across multiple cycles, which is essential for industrial applications requiring repeatability.
-
Steps in Vacuum Calibration:
- Initial Assessment: Evaluate the current performance of the vacuum system, including pressure levels and sensor accuracy.
- Verification: Use calibrated reference instruments to verify the readings of the vacuum system's sensors and gauges.
- Adjustment: If discrepancies are found, adjust the system to align with the desired parameters. This may involve recalibrating sensors or making mechanical adjustments to the vacuum pump.
- Testing: After adjustments, test the system to ensure it operates within the specified range and maintains consistency.
-
Applications of Vacuum Calibration:
- Vacuum Tempering: Ensures that the vacuum furnace maintains the correct environment for heating and cooling steel, achieving the desired microstructure (e.g., tempered martensite).
- Vacuum Deposition Coating: Guarantees that the vacuum chamber is free of contaminants, allowing for the precise deposition of materials onto substrates.
- Vacuum Furnace Processes: Ensures that the furnace operates at the correct pressure and temperature, critical for processes like quenching and tempering.
-
Tools and Equipment for Calibration:
- Vacuum Gauges: Used to measure the pressure inside the vacuum chamber.
- Reference Instruments: Provide a standard for verifying the accuracy of the vacuum system's sensors.
- Calibration Software: Automates the calibration process, making it easier to track and adjust system parameters.
-
Maintenance and Regular Calibration:
- Regular calibration is essential to maintain the accuracy and reliability of vacuum systems. Over time, components like sensors and gauges can drift, leading to inaccurate readings.
- Scheduled maintenance and calibration help prevent downtime and ensure that the vacuum system continues to perform optimally.
In summary, vacuum calibration is a critical process for ensuring the accuracy, consistency, and reliability of vacuum systems used in various industrial applications. By maintaining precise control over vacuum levels and system parameters, calibration helps achieve high-quality results in processes like vacuum tempering, deposition coating, and furnace operations.
Summary Table:
Key Aspect | Details |
---|---|
Definition | Ensuring vacuum systems operate accurately within specified parameters. |
Importance | Precision, contamination control, and consistency in industrial processes. |
Steps | Assessment, verification, adjustment, and testing. |
Applications | Vacuum tempering, deposition coating, and furnace processes. |
Tools | Vacuum gauges, reference instruments, and calibration software. |
Maintenance | Regular calibration prevents downtime and ensures optimal performance. |
Ensure your vacuum system operates at peak performance—contact our experts today for calibration services!