The capacity of an induction furnace varies significantly depending on its design, application, and power source. Induction furnaces are widely used in industries for melting metals, and their capacity can range from small laboratory-scale units (a few kilograms) to large industrial furnaces capable of handling several tons of molten metal. The capacity is influenced by factors such as the type of induction furnace (coreless or channel), the power supply (IGBT-based or other), and the specific requirements of the application. For instance, IGBT-based induction furnaces are known for their efficiency and precise control, making them suitable for both small and large-scale operations. Understanding the capacity requirements is crucial for selecting the right furnace for a given application, ensuring optimal performance and cost-effectiveness.
Key Points Explained:
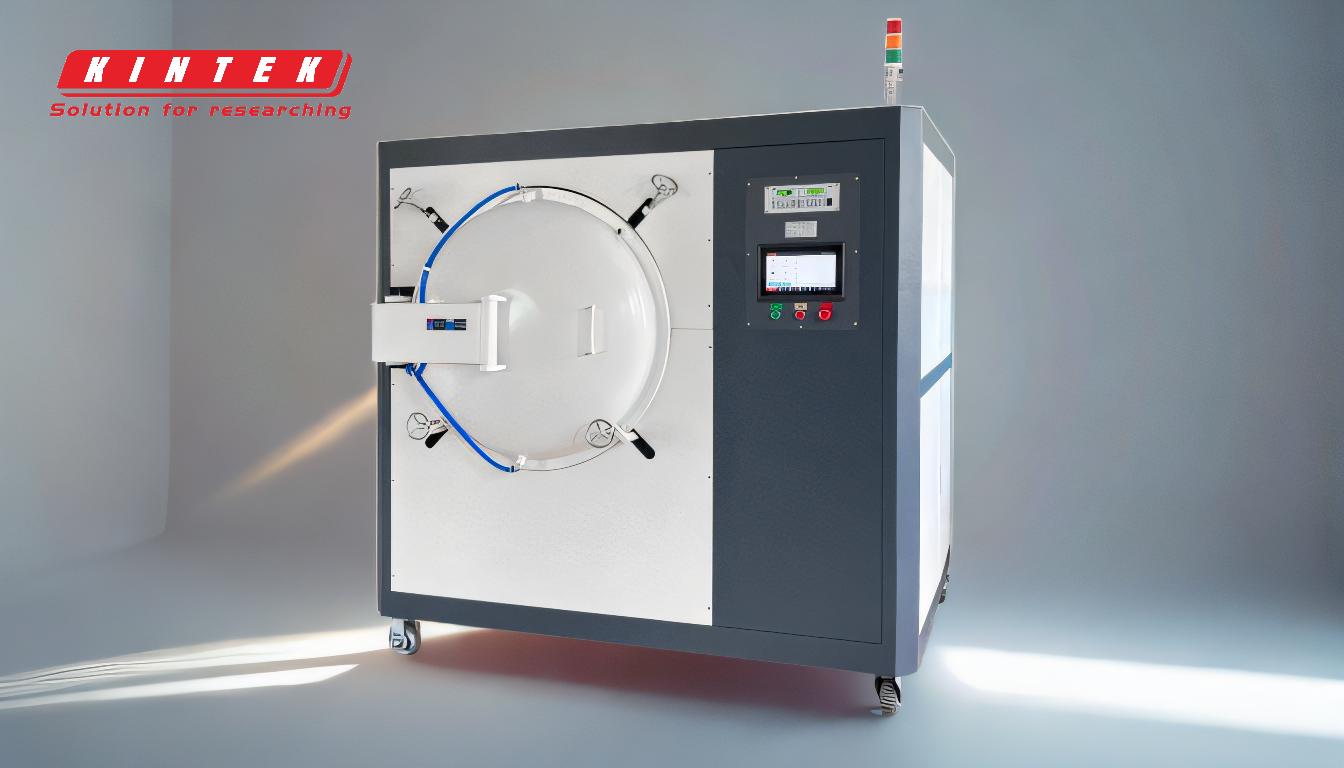
-
Definition and Types of Induction Furnaces:
- Induction furnaces are used for melting metals using electromagnetic induction. They are categorized into two main types: coreless and channel furnaces.
- Coreless furnaces are more versatile and can handle a wide range of capacities, while channel furnaces are typically used for continuous melting processes.
- The choice between these types depends on the specific application and the required capacity.
-
Capacity Range:
- The capacity of an induction furnace can range from a few kilograms to several tons. For example:
- Small-scale furnaces: 1 kg to 500 kg, often used in laboratories or small foundries.
- Medium-scale furnaces: 500 kg to 5 tons, suitable for medium-sized industrial operations.
- Large-scale furnaces: 5 tons to 50 tons or more, used in large foundries and steel plants.
- The capacity is determined by the furnace's design, power supply, and cooling system.
- The capacity of an induction furnace can range from a few kilograms to several tons. For example:
-
Role of IGBT Technology:
- IGBT (Insulated Gate Bipolar Transistor) technology has revolutionized induction furnaces by providing efficient and precise power control.
- IGBT induction furnaces are capable of handling a wide range of capacities, from small to large, due to their ability to deliver high-frequency power with minimal energy loss.
- This technology allows for better temperature control, faster melting times, and reduced operational costs, making it ideal for both small and large-scale applications.
-
Factors Influencing Capacity:
- Power Supply: The power rating of the furnace directly affects its capacity. Higher power ratings enable larger capacities and faster melting times.
- Cooling System: Efficient cooling is essential for maintaining the furnace's performance, especially at higher capacities.
- Material Type: The type of metal being melted (e.g., steel, aluminum, copper) also influences the furnace's capacity, as different metals have varying melting points and thermal properties.
- Furnace Design: The physical dimensions and design of the furnace, including the crucible size and coil configuration, play a significant role in determining its capacity.
-
Applications and Selection Criteria:
- Induction furnaces are used in various industries, including automotive, aerospace, and jewelry manufacturing.
- When selecting an induction furnace, it is essential to consider the required capacity, the type of metal to be melted, and the operational environment.
- For small-scale applications, such as research labs or artisanal metalwork, a furnace with a capacity of 1-100 kg may be sufficient. In contrast, large-scale industrial operations may require furnaces with capacities exceeding 10 tons.
-
Advantages of High-Capacity Induction Furnaces:
- High-capacity furnaces are ideal for large-scale production, offering faster melting rates and higher throughput.
- They are more energy-efficient when operating at full capacity, reducing per-unit energy costs.
- Advanced features, such as automated temperature control and real-time monitoring, enhance operational efficiency and safety.
-
Challenges and Considerations:
- High-capacity furnaces require significant initial investment and infrastructure, including robust power supply and cooling systems.
- Maintenance and operational costs can be higher for large furnaces, necessitating careful planning and budgeting.
- Proper training for operators is crucial to ensure safe and efficient operation, especially at higher capacities.
By understanding these key points, purchasers can make informed decisions when selecting an induction furnace that meets their specific capacity and operational requirements. Whether for small-scale precision work or large-scale industrial production, the right furnace can significantly enhance productivity and cost-efficiency.
Summary Table:
Capacity Range | Applications |
---|---|
1 kg - 500 kg | Laboratories, small foundries |
500 kg - 5 tons | Medium-sized industrial operations |
5 tons - 50+ tons | Large foundries, steel plants |
Key Factors | Details |
---|---|
Power Supply | Higher power enables larger capacities |
Cooling System | Essential for high-capacity performance |
Material Type | Influences melting points and capacity |
Furnace Design | Crucible size, coil configuration |
Need help selecting the right induction furnace? Contact our experts today for tailored solutions!