Catalytic fast pyrolysis is an advanced thermal conversion process that transforms biomass or plastic waste into bio-oil, syngas, and biochar. Unlike traditional fast pyrolysis, this process incorporates a catalyst to enhance the quality and yield of bio-oil while reducing undesirable byproducts like char and non-condensable gases (NCG). The catalyst lowers the reaction temperature, making the process more energy-efficient and cost-effective. The process involves three main stages: drying, pyrolysis, and condensation/collection. By optimizing these stages, catalytic fast pyrolysis minimizes bio-oil instability and maximizes the production of valuable fuels and chemicals, making it a promising method for sustainable energy production.
Key Points Explained:
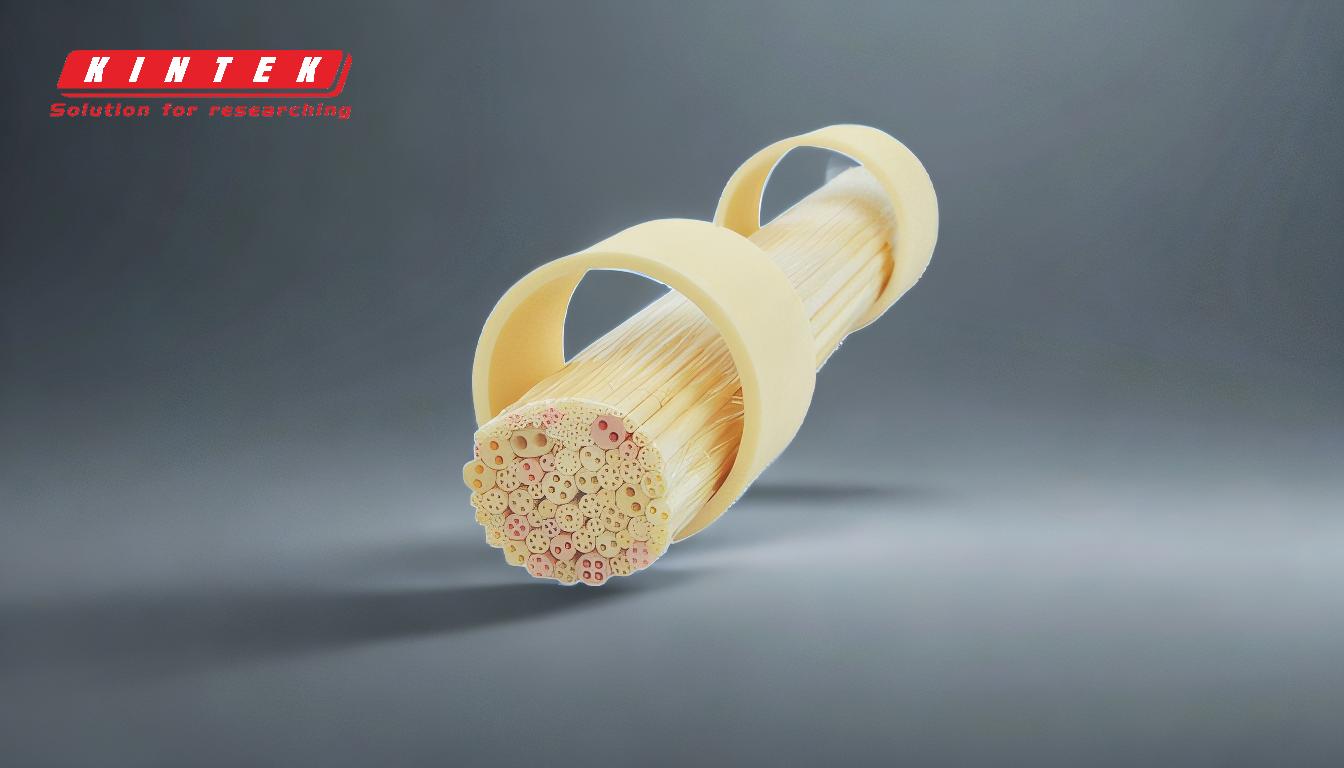
-
Definition and Purpose of Catalytic Fast Pyrolysis:
- Catalytic fast pyrolysis is a thermal decomposition process that converts biomass or plastic waste into bio-oil, syngas, and biochar in the absence of oxygen.
- The primary goal is to optimize the yield and quality of bio-oil while reducing the formation of char and non-condensable gases (NCG).
- This process is particularly valuable for producing renewable liquid fuels and chemicals, offering a sustainable alternative to fossil fuels.
-
Key Differences from Traditional Fast Pyrolysis:
- Use of a Catalyst: The introduction of a catalyst in the pyrolysis process lowers the reaction temperature, reducing energy consumption and process costs.
- Improved Bio-Oil Quality: The catalyst enhances the chemical composition of the bio-oil, making it more stable and less prone to aging or degradation.
- Reduced Byproducts: The process minimizes the production of char and NCG, which are often considered waste products in traditional pyrolysis.
-
Stages of Catalytic Fast Pyrolysis:
- Drying: The feedstock (biomass or plastic waste) is dried to remove moisture, ensuring efficient thermal decomposition in the subsequent stages.
- Pyrolysis: The dried feedstock is heated to temperatures between 400-600°C (or up to 900°C for plastic waste) in an inert atmosphere. The catalyst facilitates the breakdown of the material into volatile gases, liquid bio-oil, and solid char.
- Condensation and Collection: The volatile gases are condensed into bio-oil, while the remaining solid char (biochar) and syngas are collected for further use or refinement.
-
Role of the Catalyst:
- The catalyst plays a critical role in lowering the activation energy required for the pyrolysis reaction, enabling the process to occur at lower temperatures.
- It also promotes selective chemical reactions that enhance the yield of desirable products (e.g., bio-oil) while suppressing the formation of unwanted byproducts (e.g., char and NCG).
- Common catalysts include zeolites, metal oxides, and other materials tailored to specific feedstocks and desired outputs.
-
Advantages of Catalytic Fast Pyrolysis:
- Higher Bio-Oil Yield: The process maximizes the production of bio-oil, which can be refined into fuels or used as a chemical feedstock.
- Improved Product Quality: The bio-oil produced is more stable and has a higher energy density compared to that from traditional pyrolysis.
- Energy Efficiency: The lower reaction temperature reduces energy consumption, making the process more economically viable.
- Environmental Benefits: By converting waste materials into valuable products, catalytic fast pyrolysis contributes to waste reduction and sustainable energy production.
-
Applications and Outputs:
- Bio-Oil: The primary output, used as a renewable fuel or chemical feedstock.
- Syngas: A mixture of hydrogen, carbon monoxide, and other gases, which can be used for energy generation or as a precursor for synthetic fuels.
- Biochar: A solid residue rich in carbon, used as a soil amendment or for carbon sequestration.
- Non-Condensable Gases (NCG): Although minimized, these gases can still be captured and utilized for energy recovery.
-
Challenges and Considerations:
- Catalyst Selection: Choosing the right catalyst is crucial for optimizing the process and achieving the desired product quality.
- Feedstock Variability: The composition of biomass or plastic waste can vary, requiring adjustments in process parameters to maintain efficiency.
- Scale-Up: While catalytic fast pyrolysis shows promise at the lab scale, scaling up to industrial levels presents technical and economic challenges.
-
Future Prospects:
- Research is ongoing to develop more efficient catalysts and improve process integration with downstream refining technologies.
- The process has the potential to play a significant role in the circular economy by converting waste materials into valuable resources.
- Continued advancements in catalytic fast pyrolysis could further enhance its economic viability and environmental benefits, making it a key technology for sustainable energy production.
Summary Table:
Aspect | Details |
---|---|
Process | Converts biomass/plastic waste into bio-oil, syngas, and biochar. |
Key Feature | Uses a catalyst to enhance bio-oil quality and yield. |
Stages | Drying, pyrolysis, and condensation/collection. |
Catalyst Role | Lowers reaction temperature, improves energy efficiency, and reduces byproducts. |
Advantages | Higher bio-oil yield, improved quality, energy efficiency, and eco-friendliness. |
Applications | Renewable fuels, chemical feedstocks, energy generation, and soil amendment. |
Challenges | Catalyst selection, feedstock variability, and industrial scale-up. |
Interested in sustainable energy solutions? Contact us today to learn more about catalytic fast pyrolysis!