The cheapest type of additive manufacturing process is typically Fused Deposition Modeling (FDM). FDM is widely used due to its affordability, ease of use, and accessibility. It works by extruding thermoplastic filaments layer by layer to create a 3D object. The materials used, such as PLA and ABS, are relatively inexpensive, and the printers themselves are cost-effective compared to other additive manufacturing technologies. FDM is ideal for prototyping, hobbyists, and small-scale production, making it the most economical choice for many users.
Key Points Explained:
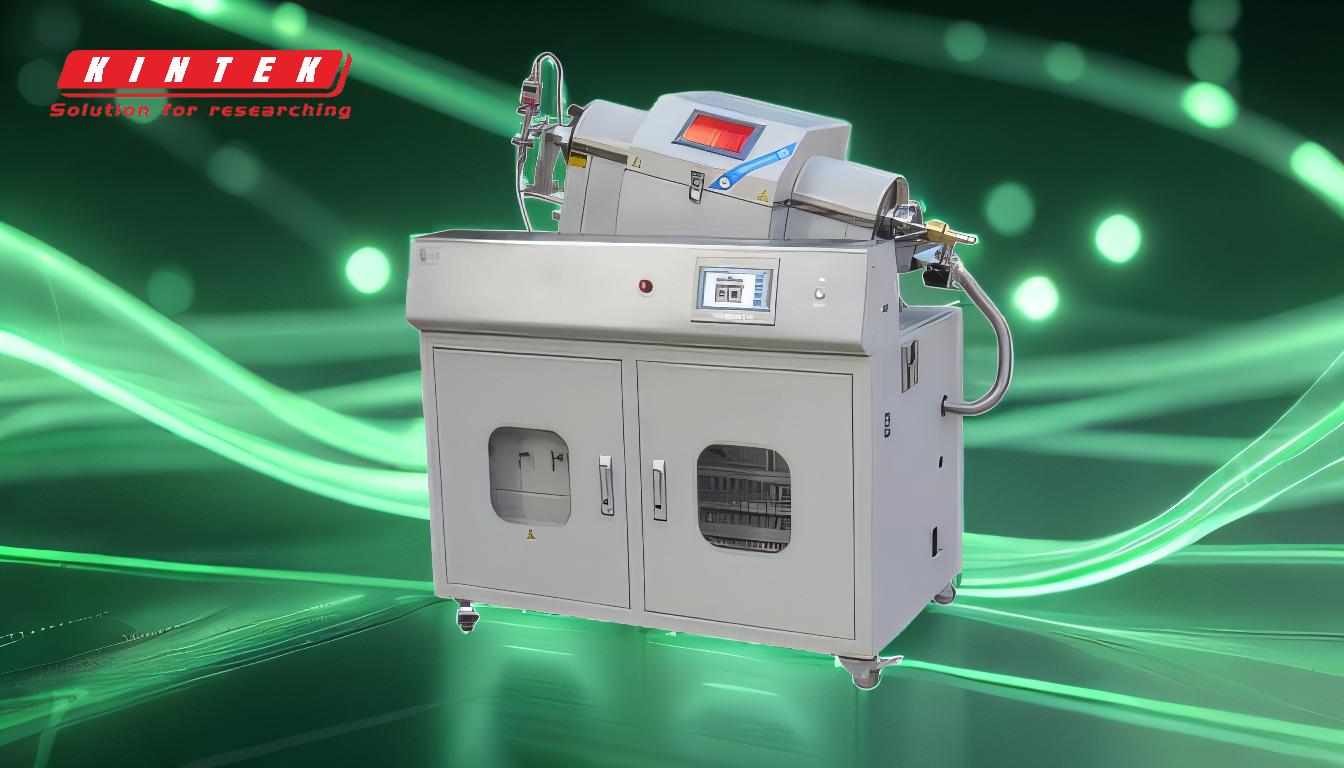
-
Fused Deposition Modeling (FDM) Overview:
- FDM is one of the most affordable and widely accessible additive manufacturing technologies.
- It uses thermoplastic filaments, such as PLA or ABS, which are inexpensive and readily available.
- The process involves heating the filament and extruding it through a nozzle to build the object layer by layer.
-
Cost-Effectiveness of FDM:
- Printer Cost: FDM printers are significantly cheaper than other additive manufacturing systems like SLA (Stereolithography) or SLS (Selective Laser Sintering). Entry-level FDM printers can cost as little as $200, while industrial-grade models are still more affordable than their counterparts.
- Material Cost: Thermoplastic filaments used in FDM are cost-effective, with prices ranging from $20 to $50 per kilogram, depending on the material type and quality.
- Maintenance and Operation: FDM printers require minimal maintenance, and the operational costs are low, making them ideal for budget-conscious users.
-
Applications of FDM:
- Prototyping: FDM is widely used for creating prototypes due to its low cost and ease of use.
- Hobbyist Projects: Many hobbyists and DIY enthusiasts prefer FDM for personal projects because of its affordability.
- Small-Scale Production: For small businesses or startups, FDM provides a cost-effective solution for producing limited quantities of parts.
-
Comparison with Other Additive Manufacturing Processes:
- SLA (Stereolithography): SLA uses liquid resin, which is more expensive than FDM filaments. Additionally, SLA printers are generally pricier and require more maintenance.
- SLS (Selective Laser Sintering): SLS involves powdered materials and high-powered lasers, making it significantly more expensive in terms of both equipment and material costs.
- Metal 3D Printing: Processes like DMLS (Direct Metal Laser Sintering) are far more expensive due to the high cost of metal powders and the complexity of the equipment.
-
Limitations of FDM:
- While FDM is the cheapest option, it has some limitations, such as lower resolution and surface finish compared to SLA or SLS.
- The mechanical properties of FDM parts may not be as strong as those produced by more advanced technologies.
-
Why FDM is the Cheapest Option:
- The combination of low-cost equipment, affordable materials, and minimal operational expenses makes FDM the most economical choice for additive manufacturing.
- Its simplicity and widespread adoption have driven down costs, making it accessible to a broad range of users.
In conclusion, FDM stands out as the most cost-effective additive manufacturing process, offering a balance of affordability, accessibility, and practicality for a wide range of applications.
Summary Table:
Aspect | Details |
---|---|
Process | Fused Deposition Modeling (FDM) |
Cost of Printers | Entry-level: ~$200; Industrial-grade: More affordable than SLA/SLS |
Material Cost | $20–$50 per kilogram (PLA, ABS) |
Applications | Prototyping, hobbyist projects, small-scale production |
Comparison | Cheaper than SLA, SLS, and metal 3D printing |
Limitations | Lower resolution, surface finish, and mechanical strength compared to SLA/SLS |
Ready to explore cost-effective 3D printing solutions? Contact us today to learn more about FDM technology!