Diamond-like carbon (DLC) coatings are a class of materials known for their unique combination of properties, including high hardness, low friction, and excellent wear and chemical resistance. These coatings are composed primarily of carbon, but their specific chemical composition can vary depending on the deposition method and the presence of hydrogen. The key to understanding DLC coatings lies in their bonding structure, which includes a mix of sp3 (diamond-like) and sp2 (graphite-like) carbon bonds. The proportion of these bonds, along with the presence of hydrogen, significantly influences the coating's mechanical and tribological properties.
Key Points Explained:
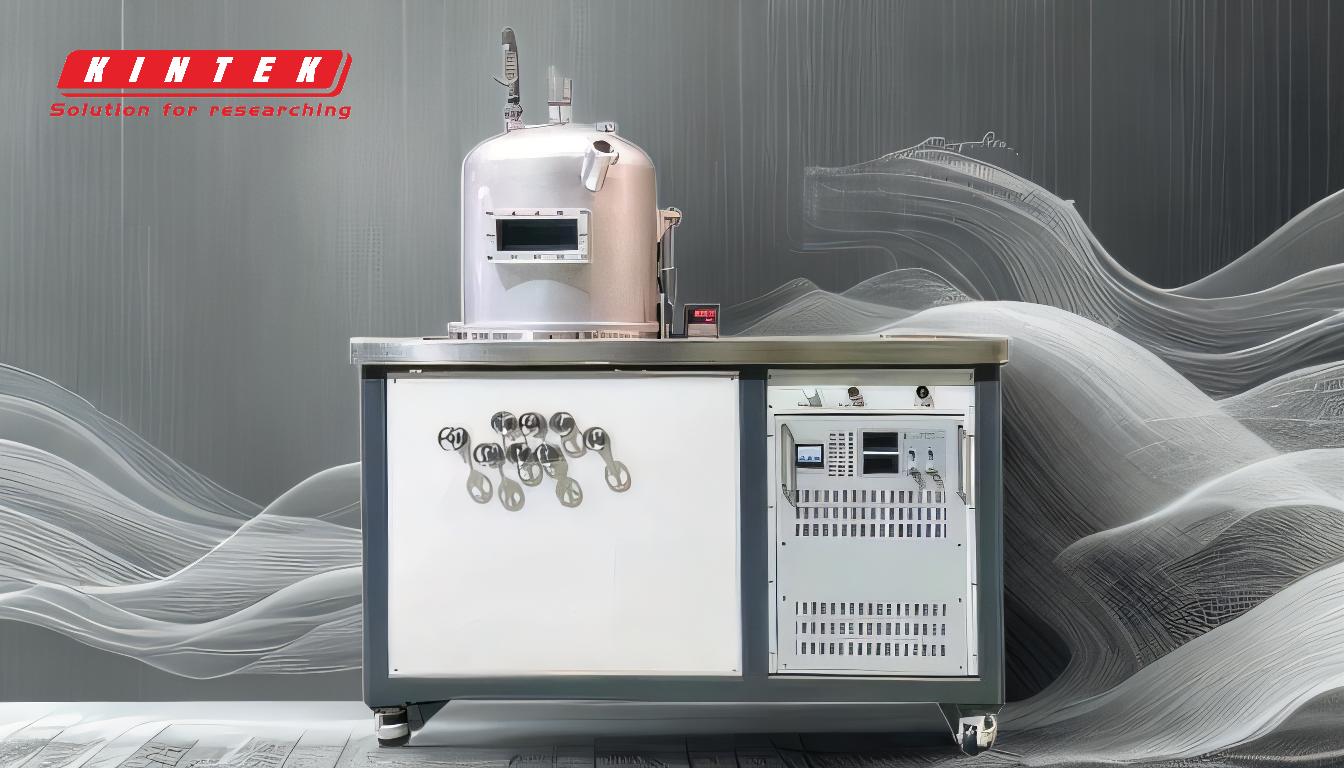
-
Primary Composition: Carbon
- DLC coatings are primarily composed of carbon atoms. The carbon atoms in DLC can form different types of bonds, which are crucial in determining the coating's properties.
- The carbon in DLC can exist in both sp3 (tetrahedral, diamond-like) and sp2 (trigonal, graphite-like) bonding configurations. The sp3 bonds contribute to the hardness and wear resistance, while the sp2 bonds provide some degree of flexibility and lower friction.
-
Bonding Structure: sp3 and sp2 Bonds
- The sp3 bonds are characteristic of diamond, giving DLC its high hardness and wear resistance.
- The sp2 bonds are similar to those found in graphite, contributing to the low friction and some degree of electrical conductivity.
- The ratio of sp3 to sp2 bonds can vary widely depending on the deposition technique and conditions, leading to different types of DLC coatings with varying properties.
-
Hydrogen Content
- Many DLC coatings are hydrogenated, meaning they contain a significant amount of hydrogen. The hydrogen content can range from a few percent to over 50%, depending on the deposition method.
- Hydrogen in DLC coatings helps to stabilize the amorphous structure and can influence the mechanical properties, such as hardness and friction coefficient.
-
Amorphous Structure
- DLC coatings are generally amorphous, meaning they lack a long-range crystalline order. This amorphous nature contributes to their isotropic properties and uniform performance in various directions.
- The amorphous structure also allows for a wide range of possible compositions and properties, making DLC coatings highly versatile.
-
Types of DLC Coatings
- ta-C (Tetrahedral Amorphous Carbon): This type of DLC is characterized by a high fraction of sp3 bonds, making it very hard and diamond-like.
- a-C (Amorphous Carbon): This type has a lower fraction of sp3 bonds and may contain more sp2 bonds, making it less hard but still very wear-resistant.
- H-terminated DLC: These coatings contain hydrogen, which can help to reduce friction and improve chemical resistance.
-
Properties Influenced by Composition
- Hardness: The hardness of DLC coatings can range from 1500 to 3000 HV (Vickers hardness), depending on the sp3/sp2 ratio and hydrogen content.
- Friction Coefficient: DLC coatings are known for their low friction coefficients, which can be as low as 0.05, making them ideal for sliding applications.
- Wear and Chemical Resistance: The combination of high hardness and low friction makes DLC coatings highly resistant to wear and corrosion, suitable for harsh environments.
-
Applications
- DLC coatings are widely used in the automotive and machinery industries, particularly in components like power trains, bearings, and camshafts, where their low friction and wear resistance can lead to significant energy savings and extended component life.
In summary, the chemical composition of DLC coatings is primarily carbon, with a mix of sp3 and sp2 bonds and often a significant amount of hydrogen. The specific composition and bonding structure determine the coating's mechanical and tribological properties, making DLC coatings highly versatile and suitable for a wide range of applications.
Summary Table:
Key Aspect | Details |
---|---|
Primary Composition | Primarily carbon atoms with sp3 (diamond-like) and sp2 (graphite-like) bonds |
Hydrogen Content | Ranges from a few percent to over 50%, stabilizing the amorphous structure |
Bonding Structure | Mix of sp3 (hardness) and sp2 (low friction) bonds |
Amorphous Structure | Lacks long-range crystalline order, enabling versatile properties |
Types of DLC Coatings | ta-C (high sp3), a-C (lower sp3), H-terminated (hydrogenated) |
Properties | High hardness (1500-3000 HV), low friction (as low as 0.05), wear resistance |
Applications | Automotive, machinery (bearings, camshafts, power trains) |
Discover how DLC coatings can enhance your applications—contact our experts today!