PVD (Physical Vapor Deposition) coatings are composed of a wide range of materials, including metals, alloys, ceramics, and specialized compounds, tailored to meet specific performance requirements across various industries. Common materials include titanium, zirconium, aluminum, stainless steel, copper, and gold, often used in aerospace and electronics. Additionally, specialized coatings like carbides, nitrides, silicides, and borides are employed for enhanced durability and functionality. These coatings can be applied to diverse substrates, such as metals, plastics, glass, and ceramics, making them versatile for applications ranging from decorative finishes to high-performance industrial components.
Key Points Explained:
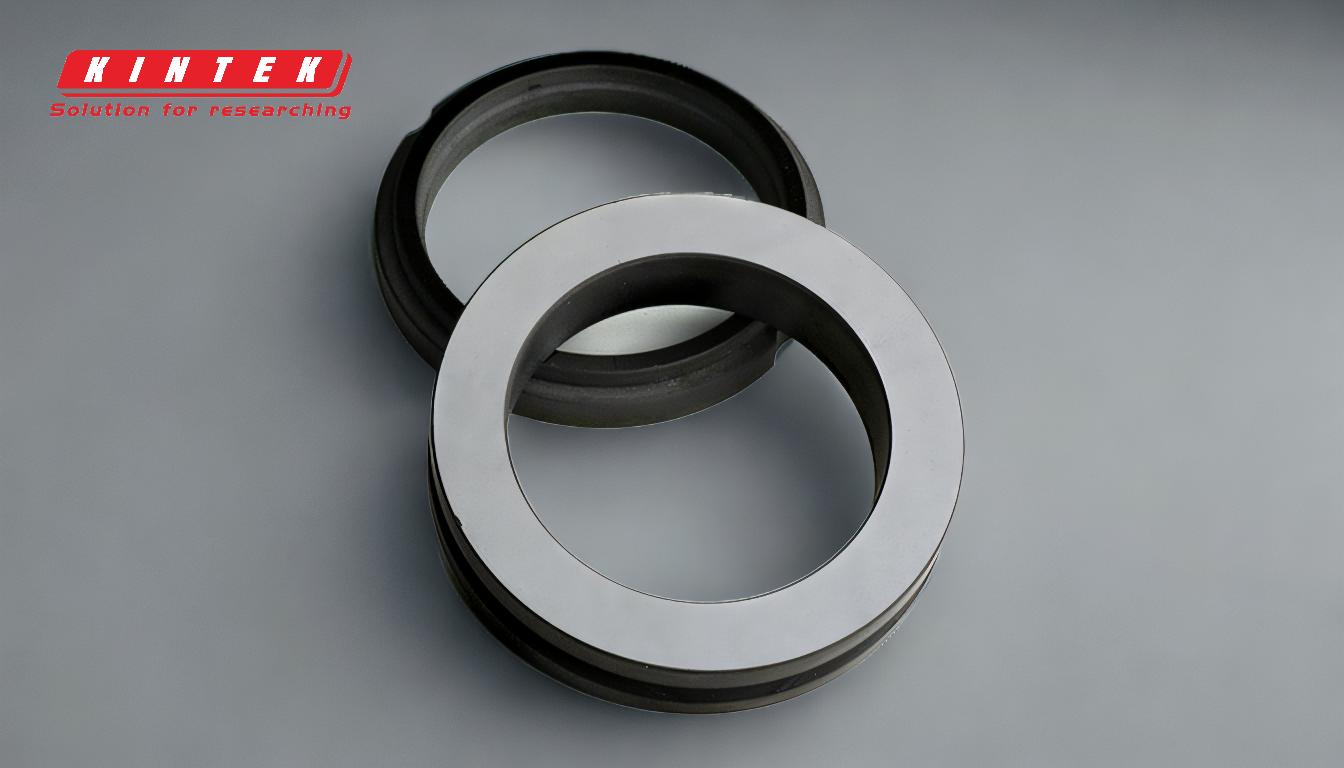
-
Primary Materials in PVD Coatings:
- Metals: Titanium, zirconium, aluminum, stainless steel, and copper are commonly used. Gold is also frequently requested, particularly for aerospace electronics due to its excellent conductivity and corrosion resistance.
- Alloys and Ceramics: Materials like Cr2N, TiN, ZnSn, AlCr, and ITO (Indium Tin Oxide) are widely used. These compounds offer specific properties such as hardness, conductivity, and optical performance, making them suitable for applications in watches, jewelry, electronics, and industrial tools.
-
Specialized Compounds:
- Carbides, Nitrides, and Silicides: These are used for their high hardness and wear resistance, making them ideal for cutting tools, machine parts, and automotive components.
- Diamond-like Carbon (DLC): Known for its exceptional hardness and low friction, DLC is used in applications requiring high wear resistance and durability.
- Sulphur and Molybdenum-based Materials: These are used for their lubricating properties, reducing friction and wear in moving parts.
-
Application-Specific Materials:
- Decorative Coatings: TiN is widely used for decorative purposes in items like watches, glasses, and hardware due to its attractive golden color and durability.
- Optical Coatings: ZnSn is used in low-emissivity (low-e) windows and glass, providing energy efficiency by reflecting infrared light.
- Conductive Coatings: ITO thin films are used in LCDs, plasma displays, and touch panels due to their high conductivity and transparency.
-
Substrates for PVD Coatings:
- Metals: Stainless steel and aluminum are common substrates, often used in industrial and aerospace applications.
- Non-Metals: PVD coatings can also be applied to nylon, plastics, glass, and ceramics, expanding their use in consumer electronics, automotive, and decorative industries.
-
Industry-Specific Requirements:
- Aerospace: Gold coatings are used for their excellent conductivity and resistance to corrosion, crucial for electronic components in harsh environments.
- Automotive: AlCr coatings extend the service life of tools and machine parts, providing enhanced durability and performance.
- Electronics: ITO thin films are essential for high-conductivity, high-hardness applications in displays and touch panels.
In summary, the chemical composition of PVD coatings is highly versatile, encompassing a wide range of materials and compounds tailored to meet specific performance requirements across various industries. This versatility makes PVD coatings a critical technology in modern manufacturing and industrial applications.
Summary Table:
Category | Materials | Applications |
---|---|---|
Primary Materials | Titanium, Zirconium, Aluminum, Stainless Steel, Copper, Gold | Aerospace electronics, industrial tools, decorative finishes |
Alloys & Ceramics | Cr2N, TiN, ZnSn, AlCr, ITO | Watches, jewelry, electronics, low-emissivity windows, LCDs, touch panels |
Specialized Compounds | Carbides, Nitrides, Silicides, Diamond-like Carbon (DLC), Sulphur, Molybdenum | Cutting tools, machine parts, automotive components, high-wear resistance |
Substrates | Metals (stainless steel, aluminum), Non-Metals (plastics, glass, ceramics) | Industrial, aerospace, consumer electronics, decorative industries |
Industry-Specific | Gold (aerospace), AlCr (automotive), ITO (electronics) | Corrosion resistance, durability, high-conductivity applications |
Unlock the potential of PVD coatings for your industry—contact our experts today to learn more!