Quenching is a critical process in materials science, particularly in metallurgy and ceramics, where it involves rapidly cooling a material to alter its microstructure and enhance its mechanical properties. In the context of fine ceramics, quenching can be used to control the crystallization process, improve hardness, and reduce residual stresses. The concept revolves around the rapid extraction of heat from the material, often using a liquid medium like water or oil, to achieve desired material characteristics. This process is essential for applications requiring high strength, wear resistance, and thermal stability.
Key Points Explained:
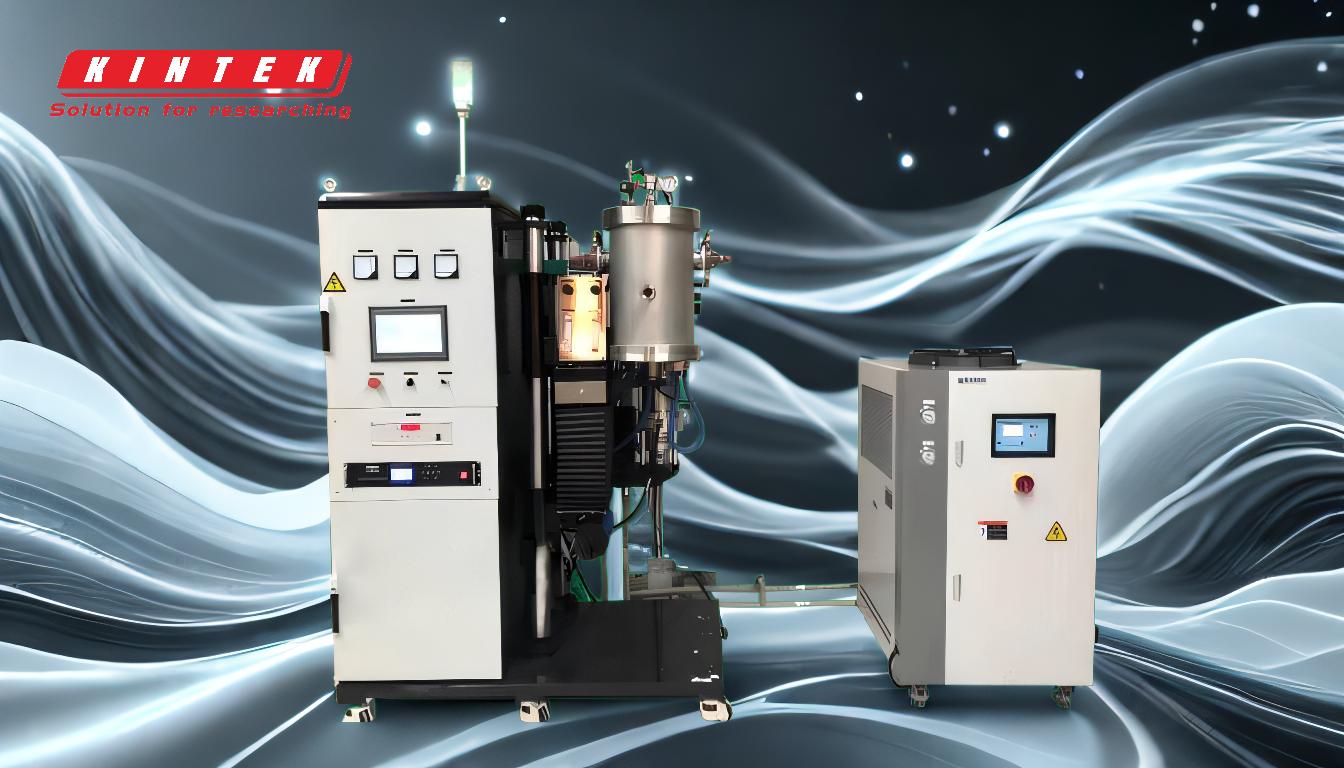
-
Definition and Purpose of Quenching:
- Quenching is a heat treatment process where a material is rapidly cooled from a high temperature to room temperature or below. This rapid cooling prevents the material from undergoing undesirable phase transformations, leading to improved mechanical properties such as hardness and strength.
- In fine ceramics, quenching is used to control the microstructure, ensuring that the material achieves the desired crystalline structure and mechanical properties. This is particularly important for applications requiring high thermal and mechanical stability.
-
Mechanism of Quenching:
- During quenching, the material is heated to a temperature where its microstructure becomes unstable or undergoes phase changes. Rapid cooling then "freezes" this microstructure, preventing the formation of undesirable phases.
- The cooling rate is critical. Too slow, and the material may not achieve the desired properties; too fast, and it may crack or warp due to thermal stresses.
-
Applications in Fine Ceramics:
- Fine ceramics, such as those used in electronics, aerospace, and medical devices, often require precise control over their microstructure to achieve specific properties. Quenching can be used to enhance the hardness, wear resistance, and thermal stability of these materials.
- For example, in the production of fine ceramics for electronic components, quenching can help achieve a uniform microstructure, which is essential for consistent electrical properties.
-
Quenching Media:
- The choice of quenching medium (e.g., water, oil, or air) depends on the material and the desired cooling rate. Water provides rapid cooling, while oil offers a more controlled cooling rate, reducing the risk of cracking.
- In fine ceramics, the quenching medium must be carefully selected to avoid thermal shock, which can cause cracking or other defects.
-
Challenges and Considerations:
- One of the main challenges in quenching fine ceramics is managing thermal stresses. Rapid cooling can cause uneven contraction, leading to cracks or warping. To mitigate this, the quenching process must be carefully controlled, often involving preheating the quenching medium or using a step-wise cooling process.
- Another consideration is the material's composition. Different ceramic materials may require different quenching strategies to achieve the desired properties.
-
Relation to Other Processes:
- Quenching is often used in conjunction with other heat treatment processes, such as tempering, to achieve a balance between hardness and toughness. In fine ceramics, this combination can be used to tailor the material's properties for specific applications.
- For example, in the production of fine ceramics for cutting tools, quenching followed by tempering can enhance both hardness and toughness, making the material more durable.
-
Future Trends:
- Advances in quenching technology, such as the use of cryogenic quenching (using liquid nitrogen), are being explored to further enhance the properties of fine ceramics. These methods offer even faster cooling rates, potentially leading to new material properties and applications.
- Additionally, the integration of quenching with other manufacturing processes, such as chemical vapor deposition (CVD), could enable the production of fine ceramics with tailored microstructures and properties in a single step.
In summary, quenching is a vital process in the production of fine ceramics, enabling the control of microstructure and the enhancement of mechanical properties. By carefully managing the cooling rate and quenching medium, manufacturers can produce materials with the desired characteristics for a wide range of applications. For more information on fine ceramics, visit fine ceramics.
Summary Table:
Key Aspect | Details |
---|---|
Definition | Rapid cooling of materials to alter microstructure and enhance properties. |
Purpose | Improves hardness, strength, and thermal stability. |
Mechanism | Freezes microstructure by rapid heat extraction. |
Applications | Fine ceramics for electronics, aerospace, and medical devices. |
Quenching Media | Water, oil, or air, chosen based on cooling rate and material. |
Challenges | Managing thermal stresses and avoiding cracking. |
Future Trends | Cryogenic quenching and integration with CVD processes. |
Discover how quenching can optimize your material properties—contact our experts today!