The Chemical Vapor Deposition (CVD) process is a critical technology in semiconductor manufacturing, used to deposit high-quality thin films and coatings on substrates. It involves the introduction of gaseous precursors into a reaction chamber, where they undergo chemical reactions to form solid materials on the substrate surface. The process is divided into several key steps, including precursor introduction, activation, surface reaction, and byproduct removal. CVD is widely used in semiconductor fabrication, particularly in CMOS processes, to create essential layers and structures. The process is influenced by factors such as temperature, pressure, and the type of heat source, and it can be tailored to meet specific requirements for film uniformity, thickness, and material properties.
Key Points Explained:
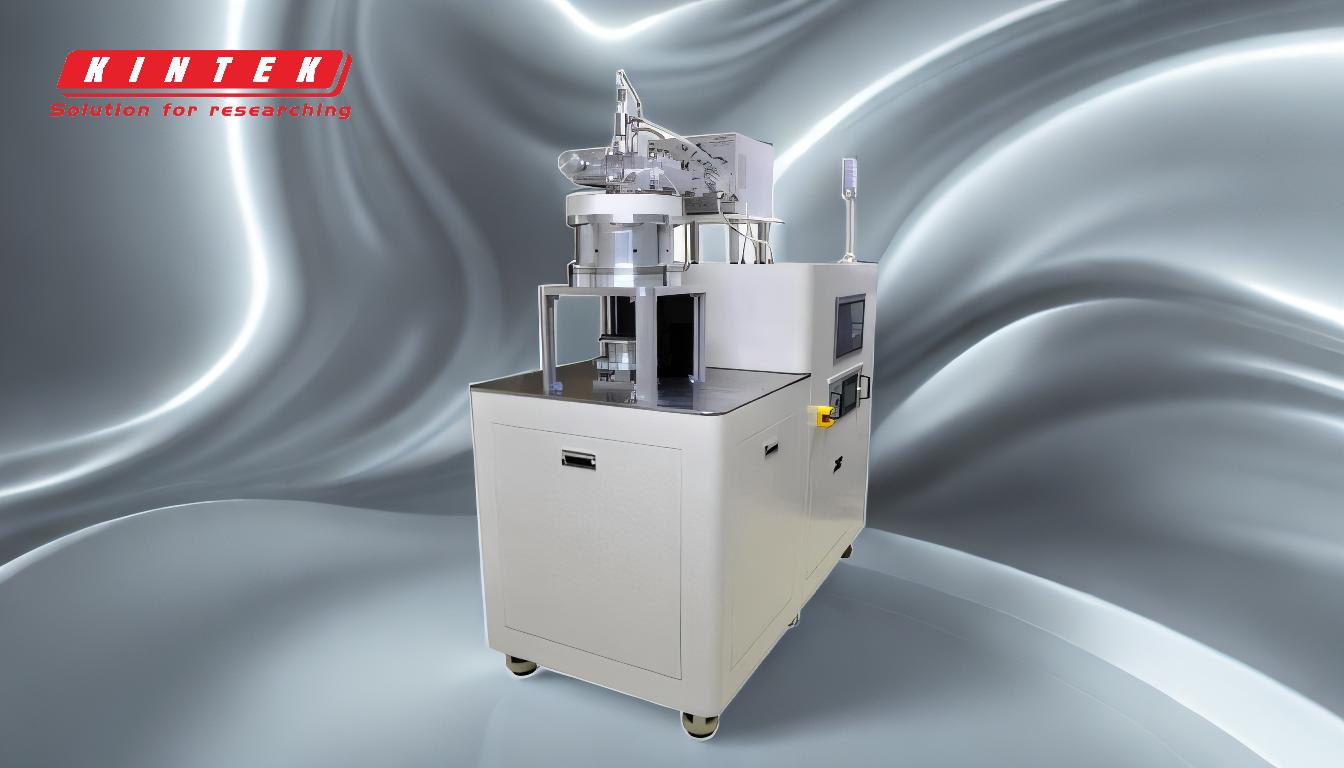
-
Introduction of Reactants
- Gaseous precursors are introduced into a reaction chamber containing the substrate.
- These precursors are typically organometallic or halide compounds that react or decompose to form the desired material.
- The choice of precursor depends on the material to be deposited and the specific requirements of the semiconductor device.
-
Activation of Reactants
- Precursors are activated using methods such as thermal energy, plasma, or catalysts.
- Activation breaks down the precursors into reactive species that can participate in surface reactions.
- The activation method is chosen based on the material properties and the desired deposition rate.
-
Surface Reaction and Deposition
- Activated precursors react at the substrate surface to form the desired material.
- The reaction begins as islands on the substrate surface, which grow and merge to create a continuous film.
- The film's properties, such as thickness and uniformity, are controlled by adjusting process parameters like temperature and pressure.
-
Removal of Byproducts
- Volatile or non-volatile byproducts are eliminated from the reaction chamber.
- Byproducts diffuse across the boundary layer and flow out of the reactor, ensuring a clean deposition environment.
- Efficient removal of byproducts is crucial for maintaining film quality and preventing contamination.
-
Influence of Process Parameters
- Temperature and pressure are critical factors in the CVD process.
- High temperatures and low pressures are typically used to enhance precursor reactivity and film uniformity.
- The type of heat source (e.g., thermal, plasma) also affects the deposition process.
-
Applications in Semiconductor Manufacturing
- CVD is widely used in CMOS fabrication to deposit thin films of materials like silicon dioxide, silicon nitride, and polysilicon.
- These films are essential for creating the layers and structures in semiconductor devices.
- The process can be tailored to meet specific requirements for film properties, such as electrical conductivity and thermal stability.
-
Advantages of CVD
- High-quality films with excellent uniformity and conformality.
- Ability to deposit a wide range of materials, including metals, semiconductors, and insulators.
- Scalability for large-scale production in the semiconductor industry.
-
Challenges in CVD
- Precursor selection and handling can be complex and costly.
- Process optimization is required to achieve desired film properties and minimize defects.
- Environmental and safety concerns related to the use of hazardous chemicals.
By understanding these key points, semiconductor manufacturers can effectively utilize the CVD process to produce high-quality thin films and coatings, essential for the fabrication of advanced semiconductor devices.
Summary Table:
Key Steps in CVD Process | Description |
---|---|
Introduction of Reactants | Gaseous precursors are introduced into the reaction chamber for deposition. |
Activation of Reactants | Precursors are activated via thermal energy, plasma, or catalysts. |
Surface Reaction & Deposition | Activated precursors react on the substrate to form a continuous film. |
Removal of Byproducts | Byproducts are eliminated to maintain film quality and prevent contamination. |
Process Parameters | Temperature, pressure, and heat source type influence film properties. |
Applications | Used in CMOS fabrication to deposit materials like silicon dioxide and nitride. |
Advantages | High-quality films, material versatility, and scalability for production. |
Challenges | Complex precursor handling, process optimization, and safety concerns. |
Discover how the CVD process can enhance your semiconductor manufacturing—contact our experts today!