DC sputtering is a widely used physical vapor deposition (PVD) technique for creating thin films. It involves bombarding a solid target material with high-energy ions in a low-pressure inert gas environment, typically argon. This process ejects atoms from the target, which then deposit onto a nearby substrate to form a thin film. DC sputtering is favored for its cost-effectiveness, ease of control, and suitability for conductive materials. It is commonly used in industries for metal deposition and coating applications. The technique relies on a DC power supply, which is less expensive and simpler to operate compared to other power sources like RF.
Key Points Explained:
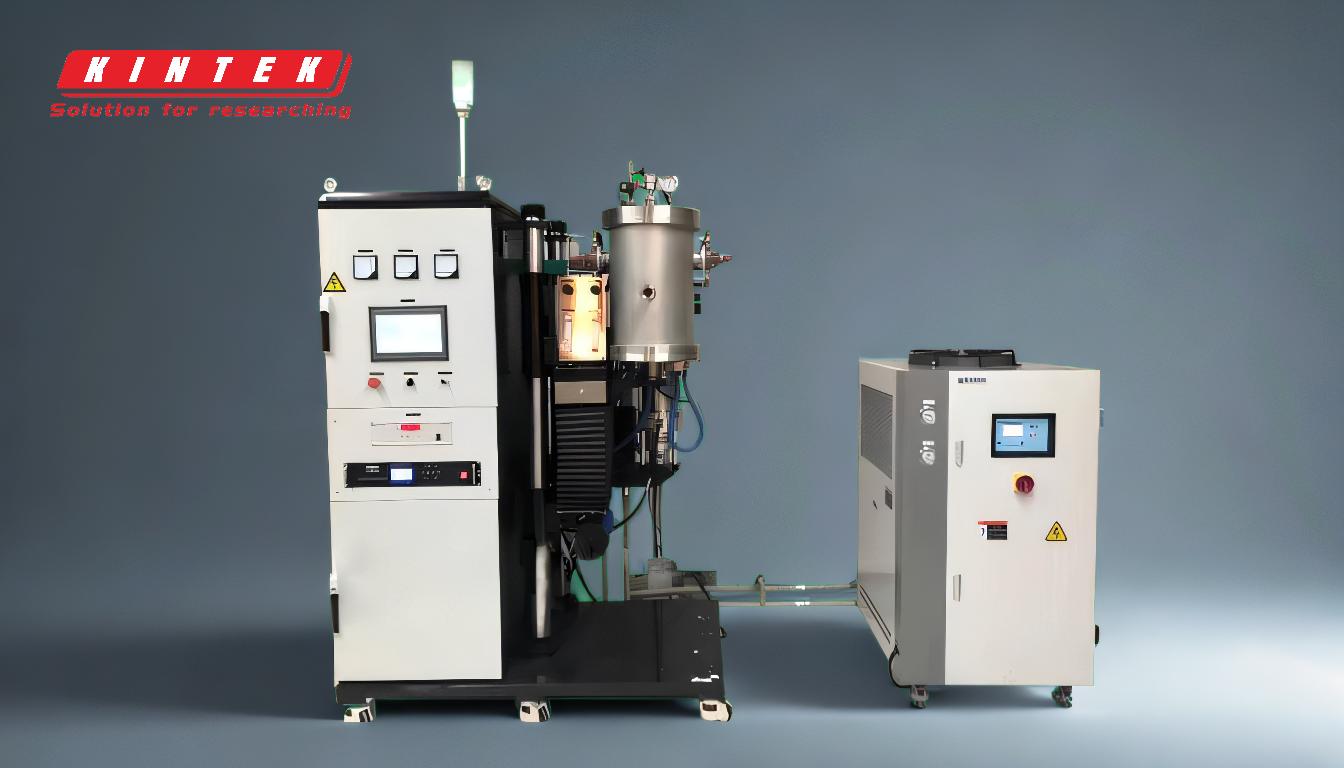
-
Definition and Process of DC Sputtering:
- DC sputtering is a type of PVD process where a solid target material is bombarded with high-energy ions in a low-pressure inert gas environment, usually argon.
- The bombardment ejects atoms from the target, which then deposit onto a substrate to form a thin film.
- This process is controlled by a DC power supply, which is cost-effective and easy to manage.
-
Advantages of DC Sputtering:
- Cost-Effective: DC power supplies are less expensive compared to other power sources like RF, making DC sputtering a more economical choice for industrial applications.
- Ease of Control: The process is straightforward to control, which is particularly beneficial for metal deposition and coating applications.
- Suitability for Conductive Materials: DC sputtering is ideal for targets made of conductive materials, as the DC power supply can effectively manage the ion bombardment process.
-
Mechanism of Sputtering:
- The process involves converting a solid material into a fine spray of microscopic particles, which appear as a gas to the human eye.
- Specialized chilling is often required to manage the heat generated during the sputtering process.
- The sputtering rate can be calculated using a specific formula that takes into account factors like ion flux density, number of target atoms, distance between target and substrate, and the velocity of sputtered atoms.
-
Applications of DC Sputtering:
- Metal Deposition: DC sputtering is commonly used for depositing metals onto various substrates, making it valuable in industries such as electronics, optics, and coatings.
- Thin Film Production: The technique is widely used to produce thin films for applications in semiconductors, solar cells, and other advanced materials.
-
Comparison with Other Sputtering Techniques:
- DC vs. RF Sputtering: While DC sputtering is limited to conductive materials, RF sputtering can be used for both conductive and non-conductive materials. However, DC sputtering is generally more cost-effective and easier to control.
- Industrial Preference: Due to its lower cost and simpler operation, DC sputtering is often preferred in industrial settings, especially for large-scale metal deposition processes.
In summary, DC sputtering is a versatile and cost-effective technique for producing thin films, particularly for conductive materials. Its ease of control and lower operational costs make it a preferred choice in various industrial applications.
Summary Table:
Aspect | Details |
---|---|
Definition | A PVD technique using DC power to bombard a target material with ions. |
Advantages | Cost-effective, easy to control, suitable for conductive materials. |
Applications | Metal deposition, thin film production for electronics, optics, and more. |
Comparison with RF | DC is cheaper and simpler but limited to conductive materials. |
Discover how DC sputtering can enhance your industrial processes—contact us today for expert advice!