The density of a sinter is a critical parameter that influences its mechanical, thermal, and electrical properties. Sintering is a process where powdered materials are compacted and heated to form a solid mass without melting the material entirely. The density of a sinter is typically expressed as a percentage of the theoretical density of the material, which is the density of the material if it were fully dense with no porosity. Achieving a high relative density is essential for ensuring the sinter's performance in its intended application. The sintering process involves multiple stages, including the removal of pores and achieving uniform shrinkage, which directly impacts the final density of the sinter.
Key Points Explained:
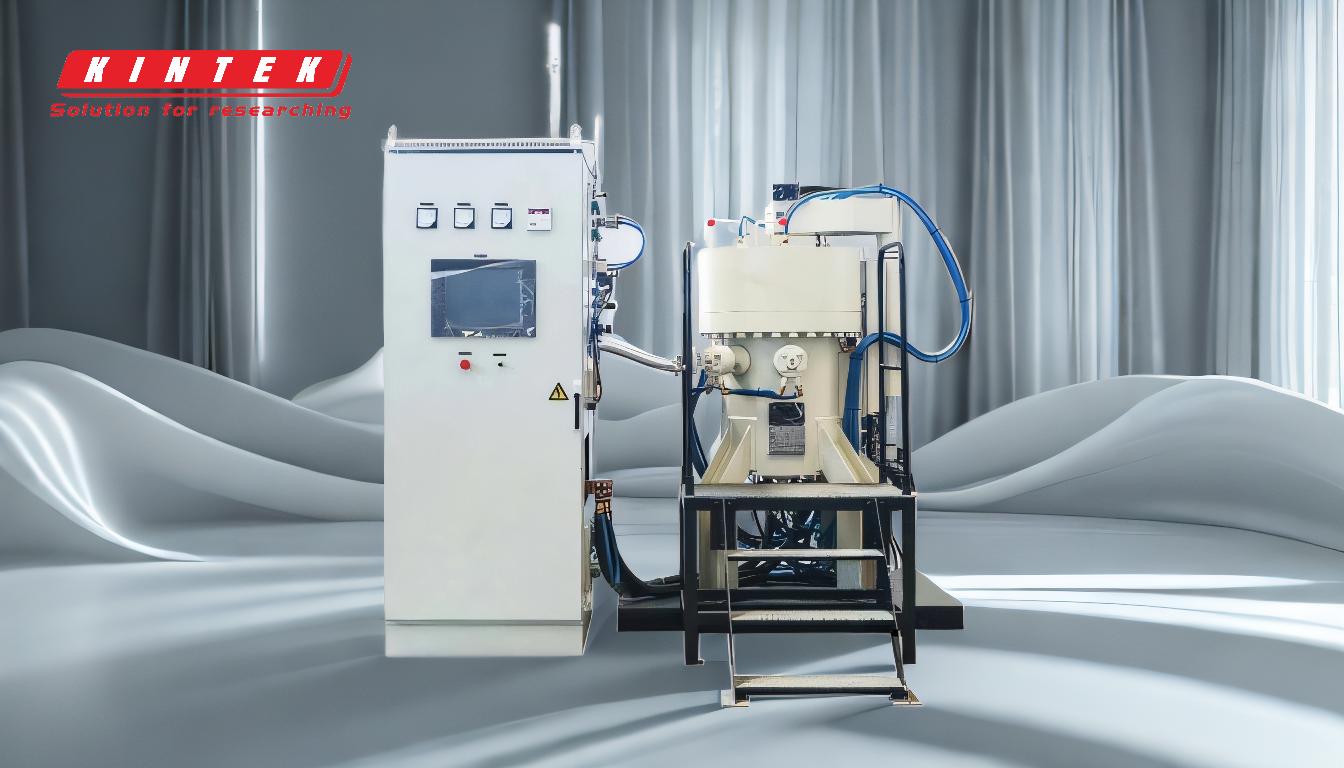
-
Definition of Sinter Density:
- The density of a sinter refers to the mass per unit volume of the sintered material. It is often expressed as a percentage of the theoretical density, which is the maximum possible density of the material with no porosity.
- The theoretical density is calculated based on the material's crystal structure and atomic weight. For example, the theoretical density of alumina (Al₂O₃) is approximately 3.98 g/cm³.
-
Importance of Relative Density:
- Relative density is a measure of how close the sintered material's density is to its theoretical density. A relative density higher than 75% is often targeted in the initial sintering stage to ensure the removal of supercritical pores.
- Supercritical pores are large voids that can significantly weaken the material. Removing these pores in the first sintering stage is crucial for achieving a strong and dense final product.
-
Sintering Process and Density Control:
- The sintering process typically involves two main stages: an initial sintering stage and a final densification stage.
- In the initial stage, the material is heated to a temperature that ensures a relative density of at least 75%. This stage helps in removing large pores and initiating the densification process.
- After cooling, the material is subjected to a second sintering temperature, where it is held until the densification is completed. This stage ensures that the material reaches its maximum possible density with minimal porosity.
-
Role of Green Density:
- Green density refers to the density of the compacted powder before sintering. A uniform green density is crucial for achieving controlled and uniform shrinkage during sintering.
- Advanced ceramics, for example, typically shrink by 20-25% during sintering. If the green density is not uniform, the shrinkage will be uneven, leading to defects such as warping or cracking in the final product.
-
Factors Affecting Sinter Density:
- Particle Size and Distribution: Smaller particles with a narrow size distribution tend to sinter more effectively, leading to higher densities.
- Sintering Temperature and Time: Higher temperatures and longer sintering times generally result in higher densities, but care must be taken to avoid over-sintering, which can lead to grain growth and reduced mechanical properties.
- Pressure: In some sintering processes, such as hot pressing or spark plasma sintering, external pressure is applied to enhance densification.
-
Measurement of Sinter Density:
- The density of a sinter can be measured using techniques such as Archimedes' principle, where the sample is weighed in air and then in a liquid to determine its volume.
- X-ray diffraction (XRD) can also be used to estimate the theoretical density based on the material's crystal structure, and this can be compared to the measured density to determine the relative density.
-
Applications and Implications of Sinter Density:
- High-density sinters are essential for applications requiring high strength, wear resistance, and thermal stability, such as in cutting tools, aerospace components, and electronic substrates.
- In contrast, controlled porosity (lower density) may be desirable in some applications, such as filters or catalysts, where a high surface area is needed.
In summary, the density of a sinter is a critical factor that determines its performance in various applications. Achieving a high relative density requires careful control of the sintering process, including the initial and final sintering temperatures, as well as the uniformity of the green density. Understanding and optimizing these factors can lead to the production of high-quality sintered materials with the desired properties.
Summary Table:
Aspect | Details |
---|---|
Definition | Mass per unit volume of sintered material, expressed as % of theoretical density. |
Theoretical Density | Maximum density with no porosity (e.g., Al₂O₃: ~3.98 g/cm³). |
Relative Density | Target >75% in initial stage to remove supercritical pores. |
Sintering Stages | 1. Initial stage (75%+ density), 2. Final densification (minimal porosity). |
Green Density | Uniformity ensures controlled shrinkage (e.g., 20-25% for ceramics). |
Key Factors | Particle size, sintering temperature/time, external pressure. |
Measurement Methods | Archimedes' principle, X-ray diffraction (XRD). |
Applications | High density: cutting tools, aerospace; lower density: filters, catalysts. |
Need help optimizing your sintering process? Contact our experts today!