The deposition rate of Physical Vapor Deposition (PVD) typically ranges from 1 to 100 angstroms per second (Å/s), depending on the specific PVD method, material properties, and process conditions. PVD involves transitioning material from a condensed phase to a vapor phase and then back to a condensed film phase on a substrate. Factors influencing the deposition rate include the physical properties of the target material, plasma characteristics (temperature, composition, density), and process parameters such as current and beam energy. PVD is widely used for producing thin films and coatings with high purity, anti-corrosion, and wear-resistant properties, but it requires skilled operation and controlled environments, such as vacuum and high temperatures.
Key Points Explained:
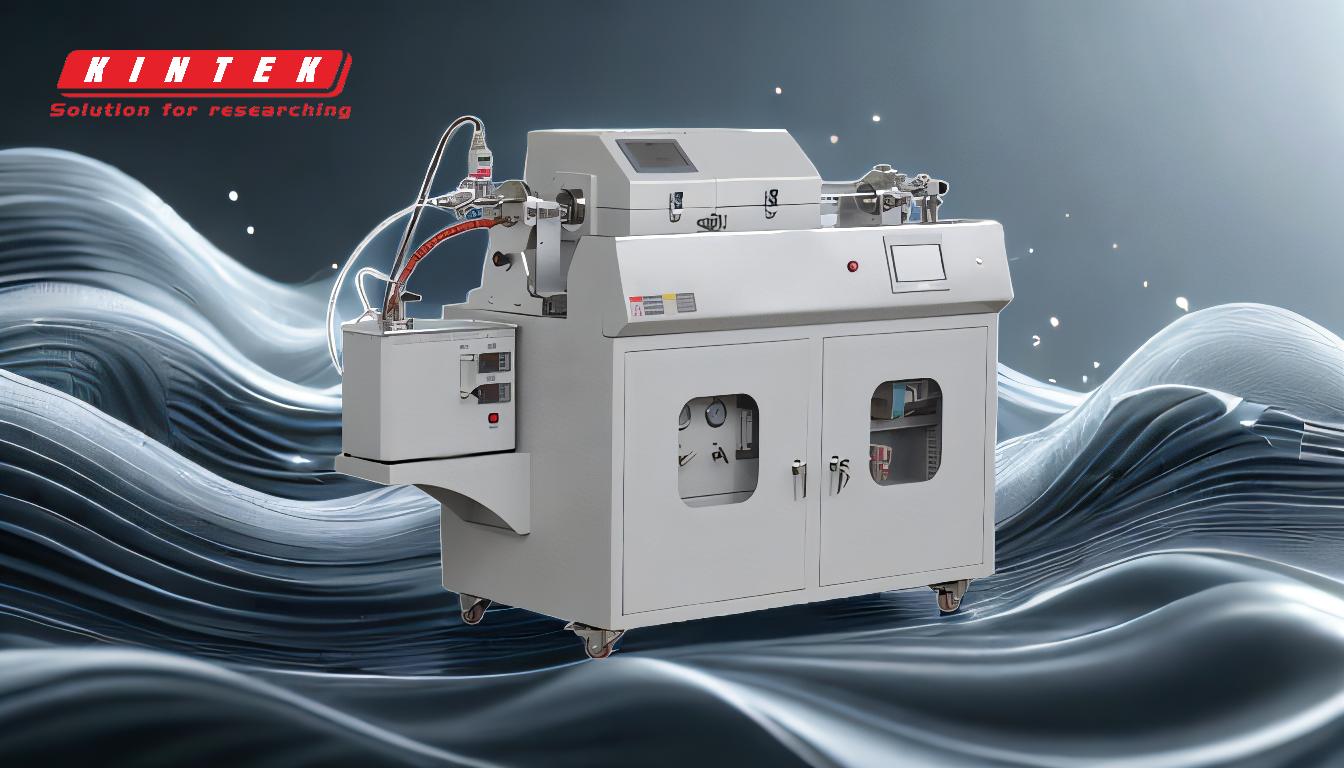
-
Typical Deposition Rate of PVD:
- The deposition rate for PVD processes generally falls within 1 to 100 Å/s. This range can vary depending on the specific PVD technique (e.g., sputtering or evaporation) and the material being deposited.
- For example, sputtering processes often have lower deposition rates compared to evaporation methods due to differences in energy transfer and material vaporization mechanisms.
-
Factors Influencing Deposition Rate:
- Target Material Properties: The physical properties of the target material, such as its melting point, vapor pressure, and atomic weight, significantly affect the deposition rate. Materials with lower melting points or higher vapor pressures tend to deposit faster.
- Plasma Characteristics: The temperature, composition, and density of the plasma used in PVD processes play a critical role. Higher plasma energy and density can enhance the deposition rate by increasing the ionization and migration of atoms or molecules.
- Process Parameters: Parameters like current, beam energy, and vacuum pressure directly impact the rate at which material is vaporized and deposited. Higher currents and beam energies generally increase the deposition rate.
- Contamination and Chamber Conditions: Monitoring and controlling the elemental composition in the chamber are essential to maintain the desired deposition rate and film quality. Contamination can reduce the deposition rate and affect the film's properties.
-
Comparison with Other Deposition Methods:
- PVD is a line-of-sight process, meaning the material is deposited directly onto the substrate in a straight path. This limits the uniformity of coatings on complex geometries but ensures high-purity films.
- Unlike Chemical Vapor Deposition (CVD), which involves chemical reactions, PVD relies on physical processes (e.g., sputtering or evaporation) to deposit material. This makes PVD more suitable for applications requiring high-purity coatings without chemical contamination.
-
Applications and Advantages of PVD:
- PVD is widely used to produce protective coatings with anti-corrosion, wear-resistant, and decorative properties. It is suitable for substrates such as metals, ceramics, glass, and polymers.
- The process is environmentally friendly because it does not involve hazardous chemicals or produce harmful byproducts.
- PVD coatings are characterized by their high purity, dense structure, and excellent adhesion to the substrate.
-
Challenges and Considerations:
- PVD processes typically require high temperatures (320 to 900°F) and vacuum conditions, which increase operational complexity and costs.
- Skilled operators are needed to monitor and control the process parameters, such as plasma characteristics and chamber conditions.
- A cooling water system is often necessary to dissipate heat generated during the process, adding to the equipment and maintenance requirements.
-
Common PVD Techniques:
- Sputtering: Involves bombarding a target material with high-energy ions to eject atoms, which then deposit onto the substrate. Sputtering is known for its controlled deposition rates and ability to deposit a wide range of materials.
- Evaporation: Involves heating the target material until it vaporizes, and the vapor condenses onto the substrate. Evaporation typically offers higher deposition rates but may be less suitable for materials with high melting points.
-
Deposition Rate Variability:
- The deposition rate can vary significantly depending on the application. For example:
- Decorative coatings may require lower deposition rates to achieve precise thickness and uniformity.
- Industrial coatings (e.g., wear-resistant or anti-corrosion layers) may prioritize higher deposition rates to improve throughput.
- The deposition rate can vary significantly depending on the application. For example:
-
Optimizing Deposition Rate:
- To achieve the desired deposition rate, operators can adjust parameters such as:
- Target power: Increasing the power supplied to the target material can enhance vaporization and deposition.
- Substrate temperature: Controlling the substrate temperature can improve film adhesion and uniformity.
- Vacuum pressure: Lowering the pressure in the chamber can increase the mean free path of atoms, improving deposition efficiency.
- To achieve the desired deposition rate, operators can adjust parameters such as:
By understanding these key points, purchasers and operators can make informed decisions about selecting PVD equipment, optimizing process parameters, and achieving the desired coating properties for their specific applications.
Summary Table:
Aspect | Details |
---|---|
Typical Deposition Rate | 1 to 100 Å/s, depending on method and material |
Key Factors | Target material properties, plasma characteristics, process parameters |
Common Techniques | Sputtering (controlled rates), Evaporation (higher rates) |
Applications | Anti-corrosion, wear-resistant, and decorative coatings |
Challenges | High temperatures, vacuum conditions, skilled operation required |
Optimization Tips | Adjust target power, substrate temperature, and vacuum pressure |
Ready to optimize your PVD process? Contact our experts today for tailored solutions!