The dew point of a sintering furnace is a critical parameter that indicates the temperature at which water vapor in the furnace atmosphere begins to condense. This measurement is essential for controlling the furnace's atmosphere, particularly in processes like sintering, where the chemical composition of the atmosphere directly impacts the quality of the final product. The dew point is typically measured using a dew-point analyzer, which indirectly determines the carbon potential of the furnace atmosphere by analyzing water vapor content. Sintering furnaces operate at high temperatures (750–1300°C) and require precise control of humidity, temperature, and atmosphere composition to ensure optimal bonding of materials, especially high-strength metals like tungsten. The dew point measurement is most relevant in the critical brazing zone, where impurities are minimized, and the furnace environment must be free from corrosive gases and excessive humidity.
Key Points Explained:
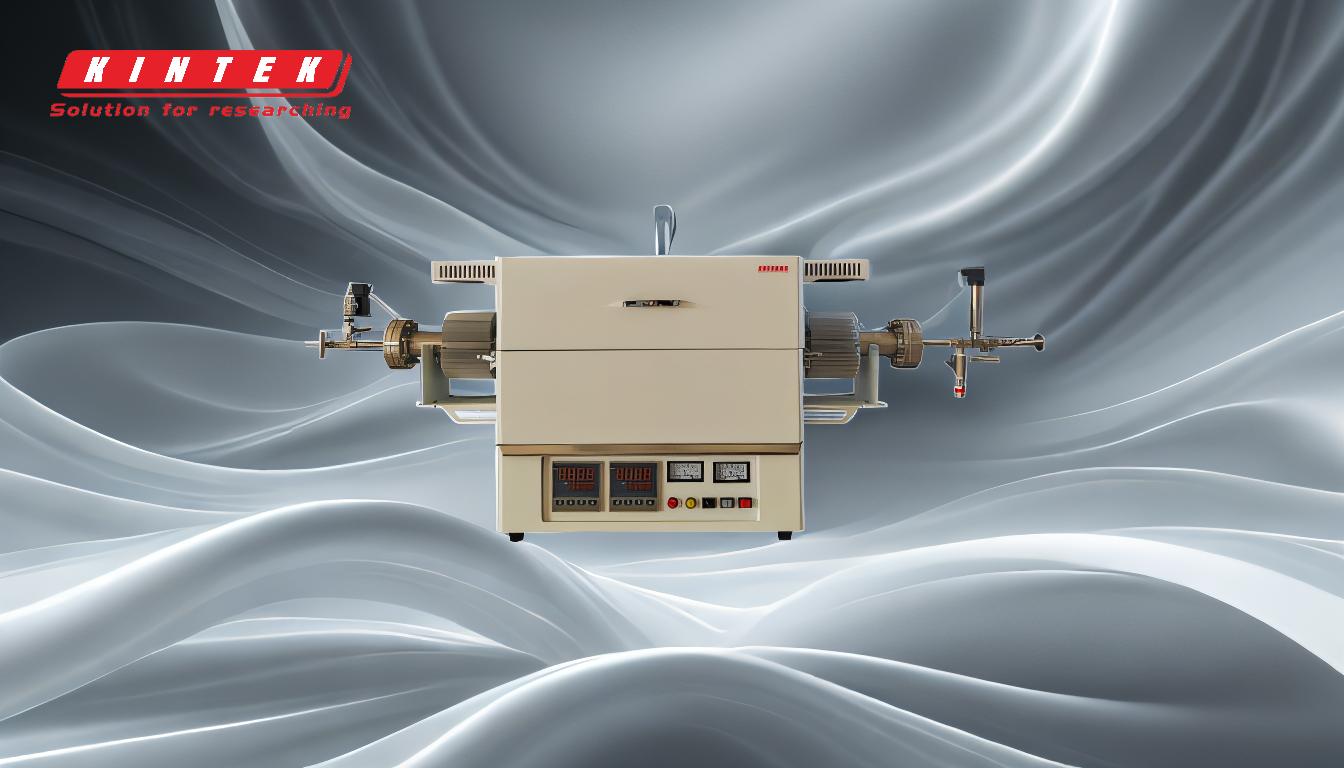
-
Definition of Dew Point in a Sintering Furnace:
- The dew point is the temperature at which water vapor in the furnace atmosphere begins to condense.
- It is a critical indicator of the moisture content in the furnace atmosphere, which directly affects the sintering process.
- High moisture levels can lead to oxidation or other undesirable reactions, especially in high-temperature environments.
-
Importance of Dew Point in Sintering:
- The dew point helps determine the carbon potential of the furnace atmosphere, which is crucial for achieving the desired material properties.
- In sintering, maintaining a controlled atmosphere with low moisture content is essential to prevent defects and ensure uniform bonding of particles.
- For materials like tungsten, which have extremely high melting points, precise control of the dew point is necessary to achieve high-strength bonds.
-
Measurement of Dew Point:
- Dew-point analyzers are used to measure the water vapor content in the furnace atmosphere.
- These instruments pull a gas sample from the furnace and analyze it to determine the dew point.
- The measurement is typically taken in the critical brazing zone, where impurities are at their lowest concentrations, ensuring accurate representation of actual sintering conditions.
-
Operating Conditions of Sintering Furnaces:
- Sintering furnaces operate at temperatures ranging from 750°C to 1300°C, depending on the material and desired characteristics.
- The furnace environment must be free from excessive humidity (relative humidity not exceeding 85%) and corrosive or explosive gases.
- Proper ventilation and avoidance of strong electromagnetic or magnetic fields are also necessary to maintain a stable furnace environment.
-
Controlled Atmospheres in Sintering Furnaces:
- Common controlled atmospheres include nitrogen-hydrogen, hydrogen, vacuum, dissociated ammonia, and endothermic gas atmospheres.
- Each atmosphere type has specific dew point requirements to ensure optimal sintering conditions.
- For example, hydrogen atmospheres require extremely low dew points to prevent oxidation, while nitrogen-based atmospheres may tolerate slightly higher moisture levels.
-
Practical Considerations for Dew Point Control:
- When heating materials that release volatile gases, sealed containers or appropriate openings should be used to prevent damage to the furnace heating elements.
- Regular monitoring and adjustment of the dew point are necessary to maintain consistent sintering conditions and avoid defects in the final product.
- The furnace must be operated in a well-ventilated environment to ensure the stability of the controlled atmosphere and prevent contamination.
By understanding and controlling the dew point in a sintering furnace, manufacturers can ensure the production of high-quality sintered components with consistent material properties. This requires careful monitoring of the furnace atmosphere, precise temperature control, and adherence to environmental guidelines.
Summary Table:
Key Aspect | Details |
---|---|
Definition | Temperature at which water vapor condenses in the furnace atmosphere. |
Importance | Determines carbon potential and prevents oxidation or defects in sintering. |
Measurement | Measured using dew-point analyzers in the critical brazing zone. |
Operating Conditions | 750–1300°C, low humidity (<85%), and controlled atmosphere. |
Controlled Atmospheres | Nitrogen-hydrogen, hydrogen, vacuum, dissociated ammonia, endothermic gas. |
Practical Considerations | Regular monitoring, sealed containers, and proper ventilation required. |
Ensure your sintering furnace operates at peak efficiency—contact our experts today for tailored solutions!