Annealing is a heat treatment process used to alter the properties of metals, primarily to soften them, improve ductility, and reduce internal stresses. It involves heating the material to a specific temperature, holding it there for a period, and then cooling it slowly. Process annealing, on the other hand, is a specific type of annealing used primarily in the manufacturing of steel and other metals to relieve stresses induced by cold working, making the material more workable without significantly altering its microstructure. Both processes aim to improve the material's properties, but they differ in their applications, temperatures, and cooling rates.
Key Points Explained:
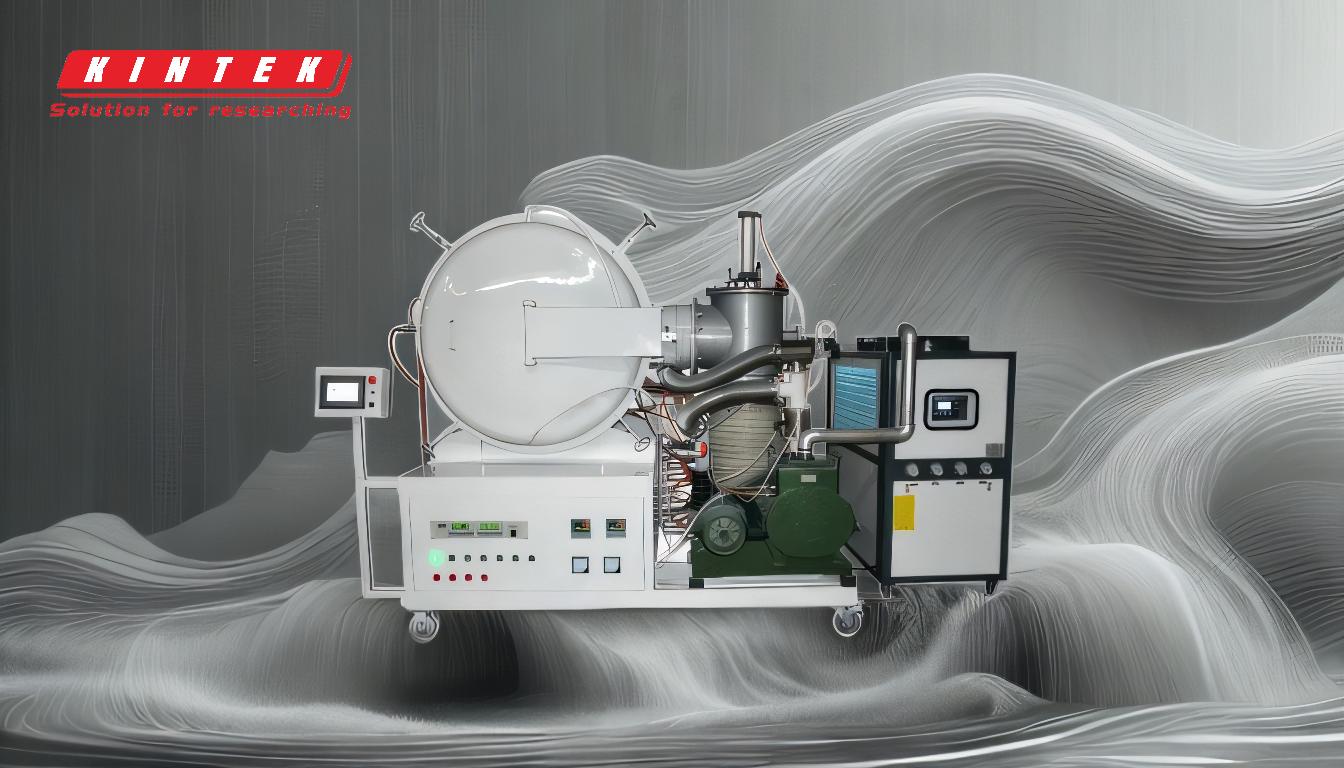
-
Definition of Annealing:
- Annealing is a broad term used to describe a heat treatment process that alters the physical and sometimes chemical properties of a material to increase its ductility and reduce its hardness. This is achieved by heating the material to a specific temperature, maintaining that temperature for a certain period, and then cooling it slowly. The primary goal is to make the material more workable, reduce internal stresses, and prepare it for further processing such as machining or additional heat treatments.
-
Purpose of Annealing:
- The main purpose of annealing is to restore the material to a 'soft' condition, which makes it easier to machine or work with. This is particularly important after processes like cold working, which can make the material hard and brittle. Annealing helps in reducing the number of dislocations in the crystal structure of the material, thereby reducing the risk of fracturing under stress and making the material more suitable for further processing.
-
Process Annealing:
- Process annealing is a specific type of annealing that is used primarily in the manufacturing of steel and other metals. It is typically performed at lower temperatures than full annealing and is used to relieve stresses induced by cold working. The process involves heating the material to a temperature below the lower critical temperature (usually between 550°C and 650°C), holding it there for a short period, and then cooling it in air. This process does not significantly alter the microstructure of the material but makes it more ductile and easier to work with.
-
Differences Between Annealing and Process Annealing:
- Temperature: Full annealing involves heating the material to a temperature above the upper critical temperature and then cooling it slowly, whereas process annealing is done at lower temperatures, typically below the lower critical temperature.
- Cooling Rate: In full annealing, the material is cooled slowly, often in a furnace, to achieve a soft and ductile structure. In process annealing, the cooling rate is faster, usually in air, which does not significantly alter the microstructure.
- Application: Full annealing is used to achieve a soft and ductile condition suitable for further processing, while process annealing is used to relieve stresses and improve workability without significantly changing the material's microstructure.
-
Applications of Annealing and Process Annealing:
- Annealing: Used in a wide range of industries, including automotive, aerospace, and manufacturing, to prepare materials for further processing. It is also used to improve the machinability of metals and to reduce internal stresses.
- Process Annealing: Commonly used in the production of steel sheets, wires, and tubes, where the material undergoes cold working and needs to be softened to continue the manufacturing process without cracking or breaking.
Understanding the differences between annealing and process annealing is crucial for selecting the appropriate heat treatment process based on the desired material properties and the specific requirements of the manufacturing process.
Summary Table:
Aspect | Annealing | Process Annealing |
---|---|---|
Temperature | Above upper critical temperature | Below lower critical temperature (550°C–650°C) |
Cooling Rate | Slow cooling (often in a furnace) | Faster cooling (usually in air) |
Purpose | Softens material, reduces hardness, and improves ductility | Relieves stresses from cold working, improves workability |
Microstructure | Alters microstructure significantly | Does not significantly alter microstructure |
Applications | Automotive, aerospace, manufacturing (machinability and stress reduction) | Steel sheets, wires, tubes (cold working stress relief) |
Need help choosing the right heat treatment process? Contact our experts today for tailored solutions!