Electric furnaces and electric arc furnaces (EAFs) are both used in industrial processes, particularly in metalworking, but they differ significantly in their design, operation, and applications. Electric furnaces typically use heating elements to generate heat through electrical resistance, making them suitable for controlled heating processes like annealing or melting non-ferrous metals. In contrast, electric arc furnaces use an electric arc to generate intense heat, primarily for melting scrap steel and producing high-quality steel with minimal impurities. EAFs are more energy-efficient and versatile, capable of handling 100% scrap material, whereas electric furnaces are better suited for precise temperature control and smaller-scale operations.
Key Points Explained:
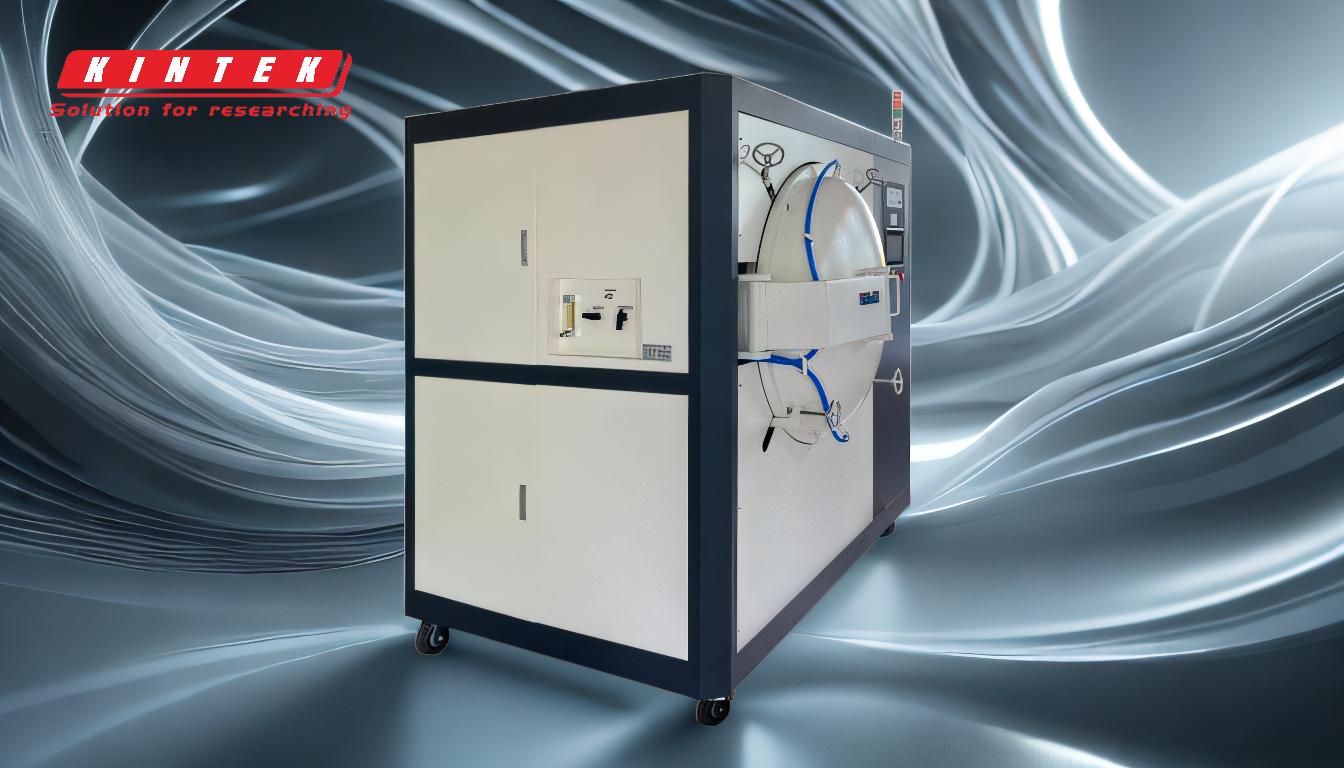
-
Heating Mechanism:
- Electric Furnace: Relies on heating elements, such as electric furnace heating elements, to generate heat through electrical resistance. This method allows for precise temperature control, making it ideal for processes like annealing, tempering, or melting non-ferrous metals.
- Electric Arc Furnace: Uses an electric arc formed between electrodes and the metal charge to produce extremely high temperatures. This method is more intense and efficient for melting large quantities of scrap steel.
-
Energy Efficiency:
- Electric Furnace: Generally less energy-efficient for large-scale metal melting due to the reliance on resistance heating, which can be slower and more energy-consuming.
- Electric Arc Furnace: More energy-efficient for steel production, as it can use 100% scrap material and does not require additional fuel like coke. This makes EAFs a greener option for steelmaking.
-
Applications:
- Electric Furnace: Commonly used for processes requiring precise temperature control, such as heat treatment, glass manufacturing, or melting non-ferrous metals like aluminum or copper.
- Electric Arc Furnace: Primarily used in the steel industry for melting scrap steel and producing high-quality steel with minimal impurities. EAFs are also used in mini-mills, which are smaller and more flexible than traditional blast furnaces.
-
Scalability:
- Electric Furnace: Typically designed for smaller-scale operations and is less adaptable for large-scale industrial processes.
- Electric Arc Furnace: Highly scalable, capable of operating as mini-mills or large industrial units. This flexibility makes EAFs suitable for a wide range of production volumes.
-
Environmental Impact:
- Electric Furnace: While it produces fewer emissions compared to fossil fuel-based furnaces, its energy consumption can still be significant depending on the process.
- Electric Arc Furnace: More environmentally friendly for steel production, as it reduces the need for virgin ores and minimizes waste by utilizing scrap material.
-
Metallurgical Quality:
- Electric Furnace: Suitable for processes requiring consistent and controlled heating but may not achieve the same metallurgical quality as EAFs for certain steel grades.
- Electric Arc Furnace: Capable of producing high-quality steel, including low-alloy steels, high-alloy steels, and even superalloys, thanks to advancements in equipment and refractories.
In summary, the choice between an electric furnace and an electric arc furnace depends on the specific requirements of the application, such as the scale of production, the type of material being processed, and the desired metallurgical quality. Electric furnaces excel in precision and control, while EAFs offer efficiency, scalability, and environmental benefits for steel production.
Summary Table:
Feature | Electric Furnace | Electric Arc Furnace (EAF) |
---|---|---|
Heating Mechanism | Uses heating elements for electrical resistance heating. | Uses an electric arc for intense heat generation. |
Energy Efficiency | Less efficient for large-scale melting. | Highly efficient, especially for steel production using scrap material. |
Applications | Ideal for precise processes like annealing, tempering, and non-ferrous metal melting. | Primarily used for melting scrap steel and producing high-quality steel. |
Scalability | Best for smaller-scale operations. | Highly scalable, suitable for mini-mills and large industrial units. |
Environmental Impact | Lower emissions but higher energy consumption. | Greener option, reduces waste and reliance on virgin ores. |
Metallurgical Quality | Suitable for controlled heating but limited for high-quality steel production. | Capable of producing high-quality steel, including alloys and superalloys. |
Still unsure which furnace suits your needs? Contact our experts today for personalized advice!