The difference between electroplated and vacuum brazed processes lies in their methods, applications, and the environments in which they are performed. Electroplating involves depositing a thin layer of metal onto a surface using an electrical current, while vacuum brazing is a high-temperature joining process that occurs in a vacuum environment, using a filler metal to bond components without melting the base materials. Vacuum brazing is particularly suited for applications requiring high strength, precision, and minimal oxidation, such as aerospace and medical devices. Electroplating, on the other hand, is often used for corrosion resistance, wear resistance, or aesthetic purposes. The vacuum brazing furnace plays a critical role in ensuring a controlled environment for the brazing process, preventing oxidation and ensuring high-quality joints.
Key Points Explained:
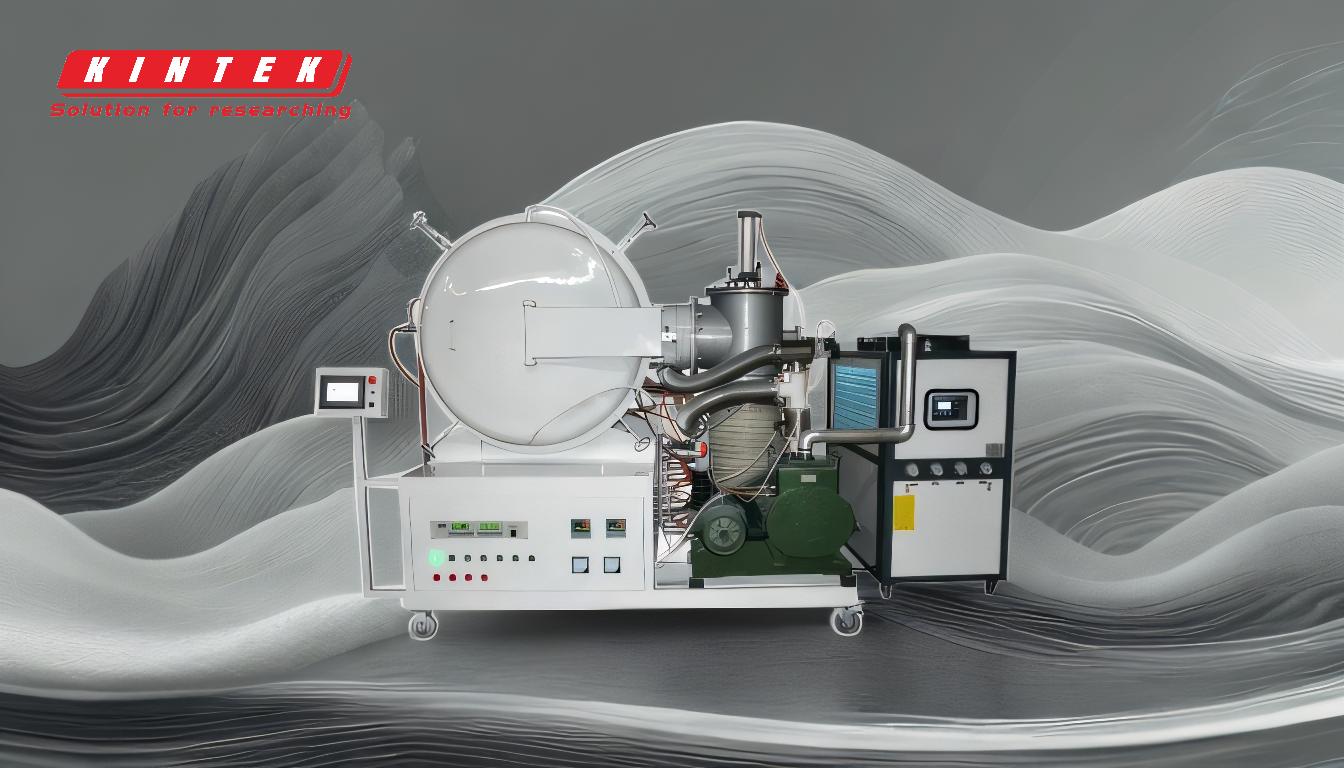
-
Process Differences:
- Electroplating: This process involves immersing the workpiece in an electrolyte solution containing metal ions. An electric current is applied, causing the metal ions to deposit onto the workpiece, forming a thin, uniform coating. It is primarily used for surface enhancement, such as improving corrosion resistance, wear resistance, or appearance.
- Vacuum Brazing: This process involves heating the workpiece and a filler metal in a vacuum environment until the filler metal melts and flows into the joint by capillary action. The base materials do not melt, ensuring dimensional stability and high joint strength. It is ideal for joining complex or heat-sensitive components.
-
Environmental Requirements:
- Electroplating: Requires a liquid electrolyte solution and an electrical power source. The process can produce hazardous waste, requiring proper disposal and environmental controls.
- Vacuum Brazing: Takes place in a vacuum brazing furnace, which creates a controlled, oxygen-free environment. This prevents oxidation and contamination, making it suitable for high-precision and high-strength applications.
-
Applications:
- Electroplating: Commonly used in industries like automotive (for corrosion-resistant coatings), electronics (for conductive layers), and jewelry (for decorative finishes).
- Vacuum Brazing: Preferred in industries requiring high-performance joints, such as aerospace (for turbine components), medical devices (for biocompatible materials), and advanced manufacturing (for complex assemblies).
-
Equipment and Control:
- Electroplating: Requires plating tanks, rectifiers, and filtration systems. The process is controlled by adjusting current density, temperature, and plating time.
- Vacuum Brazing: Utilizes a vacuum brazing furnace, which includes a vacuum system and a heating system. The process is automated, with precise temperature control and vacuum levels maintained throughout the cycle.
-
Advantages and Limitations:
-
Electroplating:
- Advantages: Cost-effective for large-scale production, versatile for various metals and applications.
- Limitations: Limited to surface coatings, potential environmental concerns, and less suitable for high-strength applications.
-
Vacuum Brazing:
- Advantages: Produces strong, clean, and oxidation-free joints, suitable for complex geometries and high-performance materials.
- Limitations: Higher equipment and operational costs, longer processing times, and limited to specific materials and joint designs.
-
Electroplating:
-
Role of the Vacuum Brazing Furnace:
- The vacuum brazing furnace is essential for maintaining the required vacuum level and temperature during the brazing process. It ensures a contamination-free environment, which is critical for achieving high-quality joints. The furnace's automated controls allow for precise regulation of heating and cooling cycles, ensuring consistent results.
By understanding these key differences, equipment and consumable purchasers can make informed decisions based on the specific requirements of their applications, whether they prioritize surface enhancement or structural integrity. For more details on vacuum brazing furnaces, visit vacuum brazing furnace.
Summary Table:
Aspect | Electroplating | Vacuum Brazing |
---|---|---|
Process | Deposits a thin metal layer using an electric current. | Joins components with a filler metal in a vacuum environment. |
Applications | Corrosion resistance, wear resistance, aesthetics (e.g., automotive, jewelry). | High-strength, precision joints (e.g., aerospace, medical devices). |
Environment | Liquid electrolyte solution, electrical power source, hazardous waste. | Vacuum brazing furnace, oxygen-free, contamination-free. |
Equipment | Plating tanks, rectifiers, filtration systems. | Vacuum brazing furnace with heating and vacuum systems. |
Advantages | Cost-effective, versatile for surface coatings. | Strong, clean, oxidation-free joints, suitable for complex geometries. |
Limitations | Limited to surface coatings, environmental concerns. | Higher costs, longer processing times, specific material requirements. |
Need help choosing between electroplating and vacuum brazing for your project? Contact our experts today for tailored advice!