Brazing is a joining technique that uses a filler metal to bond components without melting the base materials, typically at temperatures above 840°F. It is known for creating strong joints, often as strong as the base metals themselves, making it a preferred method in industries such as cookware, automotive, and HVAC systems. Flame brazing and induction brazing are two common methods of brazing, each with distinct differences in how heat is applied and the resulting effects on the process. Below, we explore the key differences between these two methods.
Key Points Explained:
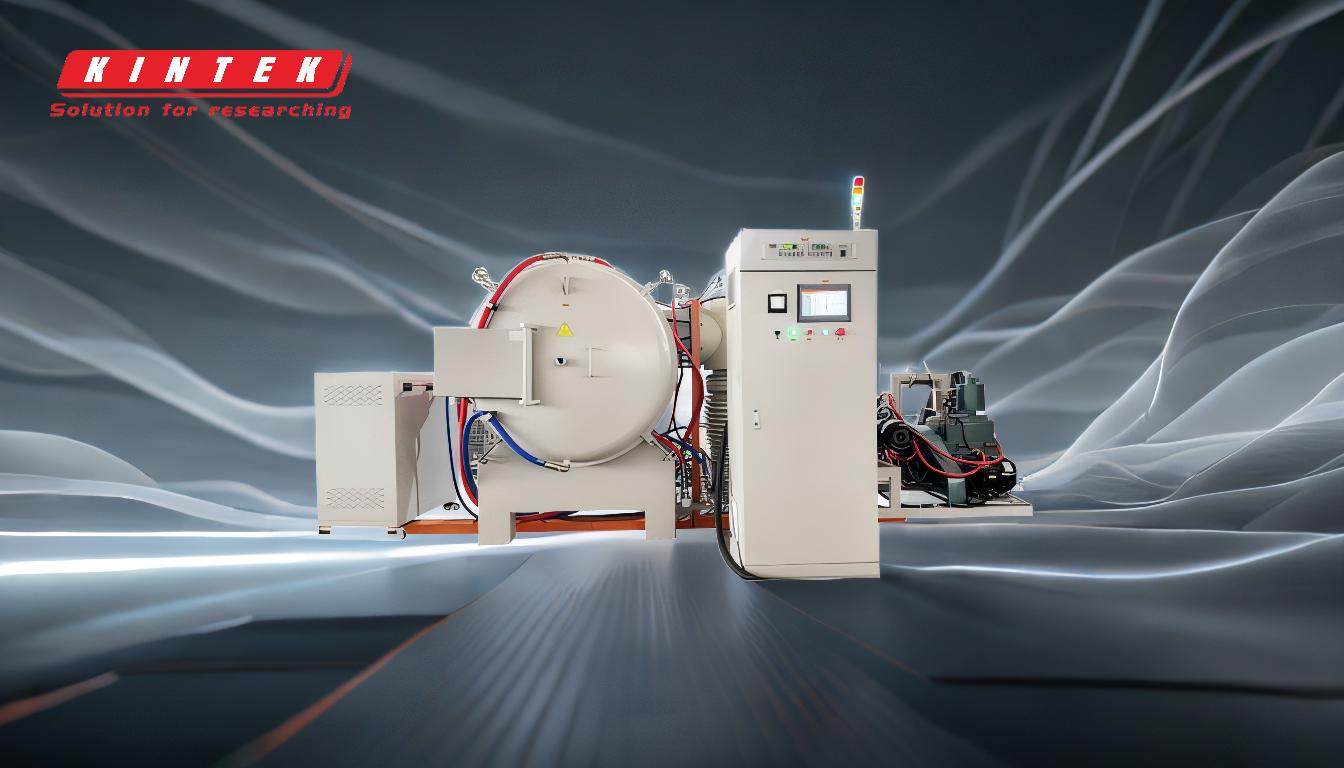
-
Heat Source and Application:
- Flame Brazing: This method uses a gas flame (often oxy-acetylene or propane) to directly heat the joint area and the filler metal. The flame is manually or mechanically directed at the workpiece, allowing for localized heating.
- Induction Brazing: This method uses electromagnetic induction to generate heat within the workpiece itself. An induction coil creates an alternating magnetic field, which induces eddy currents in the conductive base material, heating it from within.
-
Precision and Control:
- Flame Brazing: While effective, flame brazing can be less precise due to the manual control of the flame. It may result in uneven heating or overheating if not carefully managed.
- Induction Brazing: Induction brazing offers superior precision, as the heat is generated directly within the workpiece. This allows for consistent and localized heating, reducing the risk of overheating or damaging surrounding areas.
-
Speed and Efficiency:
- Flame Brazing: The process can be slower, especially for larger or more complex joints, as the heat transfer relies on the flame's contact with the surface.
- Induction Brazing: Induction brazing is generally faster and more efficient, as the heat is generated internally and can be quickly controlled. This makes it ideal for high-volume production.
-
Energy Consumption:
- Flame Brazing: Typically consumes more energy, as the flame must continuously burn to maintain the required temperature.
- Induction Brazing: More energy-efficient, as the induction process directly heats the workpiece without significant heat loss to the surrounding environment.
-
Applications and Suitability:
- Flame Brazing: Often used for larger components or in situations where portability is required. It is also suitable for materials that are less conductive or have irregular shapes.
- Induction Brazing: Ideal for smaller, more precise components, especially those made of conductive materials like copper, brass, or steel. It is commonly used in industries requiring high precision, such as electronics or medical devices.
-
Joint Quality and Consistency:
- Flame Brazing: The quality of the joint can vary depending on the operator's skill and the consistency of the flame application.
- Induction Brazing: Produces highly consistent and repeatable joints due to the controlled and automated nature of the process.
-
Equipment and Setup:
- Flame Brazing: Requires relatively simple equipment, such as a gas torch and regulators, making it more accessible for small-scale operations.
- Induction Brazing: Involves more complex and expensive equipment, including induction coils and power supplies, which may require a higher initial investment.
-
Environmental and Safety Considerations:
- Flame Brazing: Involves open flames, which can pose safety hazards and require proper ventilation to manage fumes and combustion byproducts.
- Induction Brazing: Generally safer, as there are no open flames or combustion gases. It also produces fewer emissions, making it more environmentally friendly.
By understanding these differences, equipment and consumable purchasers can make informed decisions about which brazing method best suits their specific application needs. Flame brazing offers simplicity and versatility, while induction brazing provides precision, efficiency, and consistency, particularly for high-volume or precision-critical applications.
Summary Table:
Aspect | Flame Brazing | Induction Brazing |
---|---|---|
Heat Source | Gas flame (oxy-acetylene or propane) | Electromagnetic induction |
Precision | Less precise, manual control | Highly precise, controlled heating |
Speed | Slower, especially for larger joints | Faster, ideal for high-volume production |
Energy Efficiency | Less energy-efficient, continuous flame required | More energy-efficient, minimal heat loss |
Applications | Suitable for larger, irregular, or less conductive materials | Ideal for smaller, precise components in conductive materials |
Joint Quality | Varies based on operator skill | Consistent, repeatable, and automated |
Equipment | Simple setup (gas torch, regulators) | Complex setup (induction coils, power supplies) |
Safety | Open flames, requires ventilation | Safer, no open flames or combustion gases |
Need help choosing the right brazing method for your application? Contact our experts today!