Hot pressing and isostatic pressing are both advanced manufacturing techniques used to densify materials, but they differ significantly in their methods, applications, and outcomes. Hot pressing involves applying uniaxial pressure and heat simultaneously to a material, typically in a mold, to achieve densification. In contrast, isostatic pressing, including hot isostatic pressing (HIP) and cold isostatic pressing (CIP), applies uniform pressure from all directions using a fluid medium, often at elevated temperatures. HIP is particularly effective in eliminating porosity and improving mechanical properties, making it ideal for high-performance applications. Warm isostatic pressing, a variant of HIP, operates at intermediate temperatures and is used for specific material processing needs. The choice between these methods depends on factors like material type, desired density, complexity of the part, and cost considerations.
Key Points Explained:
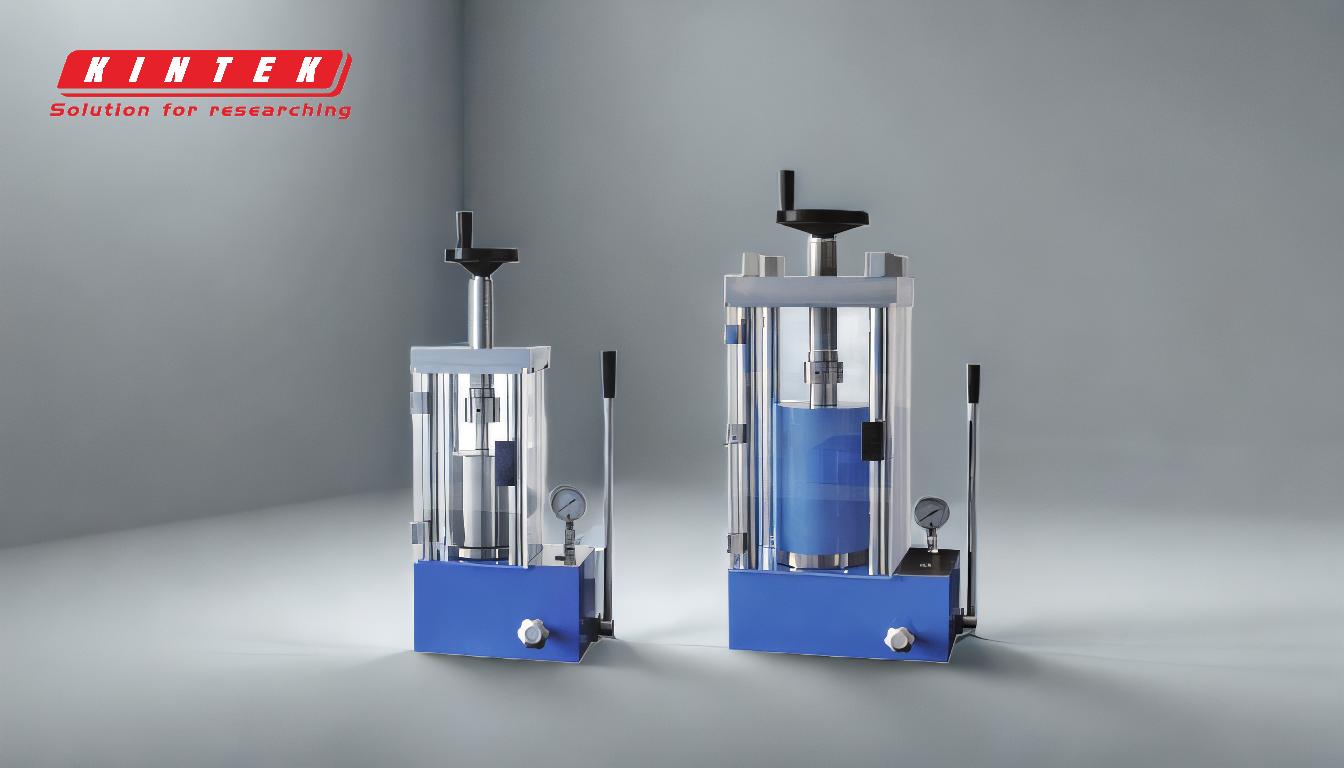
-
Hot Pressing:
- Hot pressing involves applying uniaxial pressure and heat simultaneously to a material, usually in a mold.
- This method is effective for achieving densities ranging from 65% to 99%, depending on the material.
- It is commonly used for simpler shapes and materials that do not require uniform density throughout the part.
- The process is less expensive than HIP but may result in less uniform density and mechanical properties.
-
Isostatic Pressing:
- Isostatic pressing applies uniform pressure from all directions using a fluid medium, which can be either liquid or gas.
- This method is divided into two main types: Cold Isostatic Pressing (CIP) and Hot Isostatic Pressing (HIP).
- CIP is used for producing large and complex parts where the initial cost is justified, while HIP is conducted at high temperatures and is particularly effective in eliminating porosity and improving mechanical properties.
-
Hot Isostatic Pressing (HIP):
- HIP utilizes elevated temperature and isostatic gas pressure to eliminate porosity and increase density in metals, ceramics, polymers, and composite materials.
- The process yields a more consistent product with densities exceeding 99%, making it ideal for high-performance applications.
- HIP is more costly than conventional hot pressing but offers significant advantages, including improved mechanical properties, reduced scrap, and the ability to repair internal porosity defects.
-
Warm Isostatic Pressing:
- A warm isostatic press operates at intermediate temperatures, usually heated to the temperature of the liquid medium first.
- The heated liquid medium is continuously injected into the sealed pressing cylinder, which is equipped with a heat generator for accurate temperature control.
- This method is suitable for specific material processing needs where intermediate temperatures are required.
-
Applications and Advantages:
- Hot pressing is suitable for simpler shapes and materials that do not require uniform density, making it cost-effective for certain applications.
- Isostatic pressing, particularly HIP, is ideal for complex shapes and high-performance materials, offering advantages such as increased product density, improved mechanical properties, and longer service life.
- The choice between these methods depends on the material type, desired density, complexity of the part, and cost considerations.
In summary, while both hot pressing and isostatic pressing are used to densify materials, they differ in their methods and applications. Hot pressing is more cost-effective for simpler shapes, whereas isostatic pressing, especially HIP, offers superior density and mechanical properties for complex and high-performance applications. Warm isostatic pressing provides a middle ground, operating at intermediate temperatures for specific material processing needs.
Summary Table:
Aspect | Hot Pressing | Isostatic Pressing |
---|---|---|
Pressure Application | Uniaxial pressure (one direction) | Uniform pressure from all directions (using fluid medium) |
Temperature | Simultaneous heat and pressure | Elevated temperatures (HIP) or room temperature (CIP) |
Density Achieved | 65% to 99%, depending on material | Exceeds 99% (HIP), ideal for high-performance applications |
Cost | Less expensive | More expensive, especially HIP |
Applications | Simpler shapes, cost-effective for certain materials | Complex shapes, high-performance materials, and porosity elimination |
Advantages | Cost-effective, suitable for simpler shapes | Uniform density, improved mechanical properties, longer service life |
Need help choosing the right pressing method for your materials? Contact our experts today for personalized advice!