Hot pressing and cold pressing are two distinct techniques used in metallurgy, each with unique processes and applications. Hot pressing combines compaction and sintering at elevated temperatures within a single chamber, making it suitable for materials that require high-density consolidation and enhanced mechanical properties. In contrast, cold pressing involves compaction at room temperature, with sintering performed separately in a furnace. This method is often used for simpler shapes and materials that do not require the high temperatures of hot pressing. Below, we explore the key differences and applications of these techniques.
Key Points Explained:
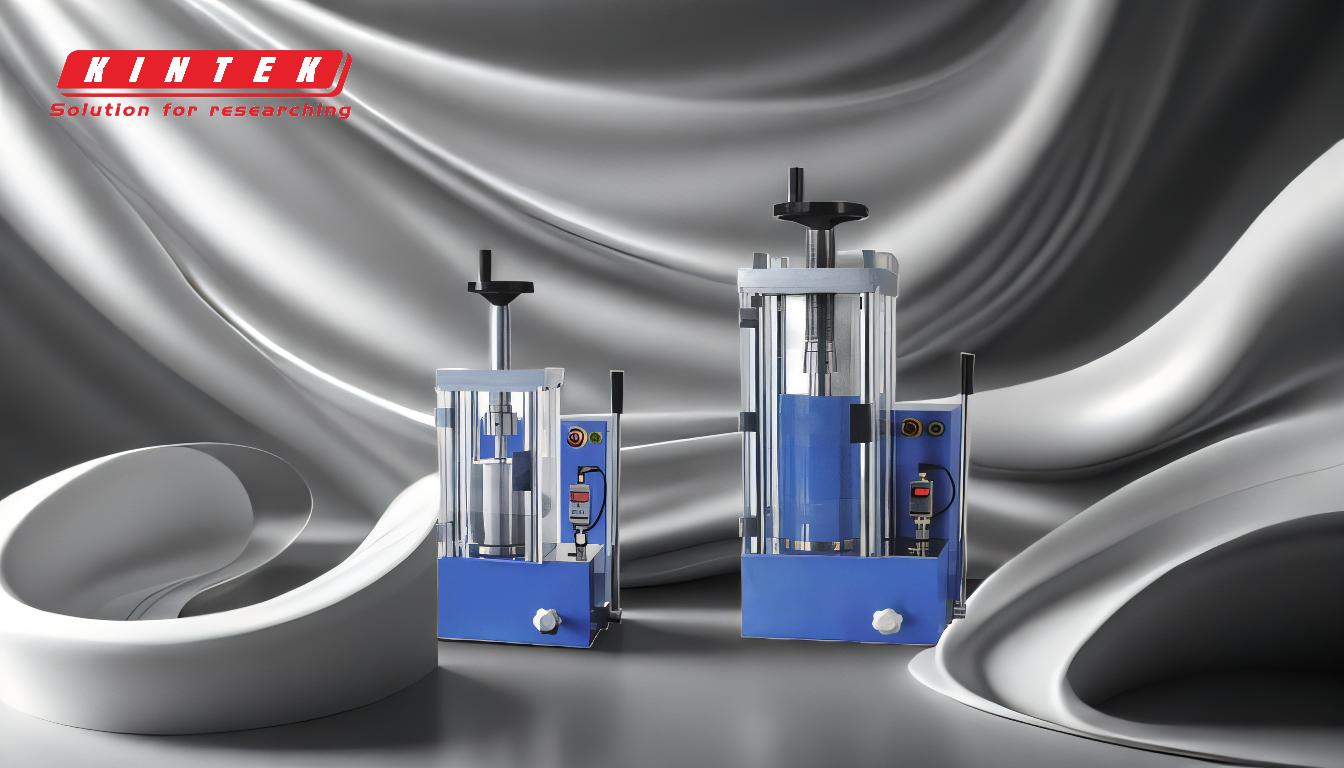
-
Temperature Application:
- Hot Pressing: Utilizes elevated temperatures during the compaction process, often ranging from 500°C to 2000°C, depending on the material. This heat facilitates both compaction and sintering simultaneously, leading to denser and stronger final products.
- Cold Pressing: Operates at room temperature during compaction. Any heat applied is minimal, such as for burning off lubricants, and sintering is conducted separately in a furnace.
-
Process Integration:
- Hot Pressing: Combines compaction and sintering into a single step, reducing the overall processing time and energy consumption. This integration is particularly beneficial for complex materials that require high-density consolidation.
- Cold Pressing: Requires a two-step process where compaction and sintering are performed separately. This method is simpler and often used for materials that do not require the high temperatures of hot pressing.
-
Material Suitability:
- Hot Pressing: Ideal for materials that need high-density consolidation and enhanced mechanical properties, such as ceramics, refractory metals, and advanced composites. The elevated temperatures help in achieving better bonding and reduced porosity.
- Cold Pressing: Suitable for simpler shapes and materials that do not require high temperatures, such as certain metals and alloys. It is often used in applications where cost and simplicity are prioritized over high performance.
-
Equipment Requirements:
- Hot Pressing: Requires specialized equipment, such as a hot press machine, capable of withstanding high temperatures and pressures. These machines are more complex and expensive compared to cold pressing equipment.
- Cold Pressing: Utilizes simpler and less expensive equipment, as it does not need to withstand high temperatures. The primary requirement is a press capable of applying sufficient pressure for compaction.
-
Applications:
- Hot Pressing: Commonly used in the production of advanced materials, such as cutting tools, aerospace components, and electronic substrates. The high temperatures and pressures enable the creation of materials with superior properties.
- Cold Pressing: Often employed in the manufacturing of simpler components, such as automotive parts, household items, and certain types of bearings. It is also used in powder metallurgy for producing near-net-shape parts.
In summary, the choice between hot pressing and cold pressing depends on the specific requirements of the material and the desired properties of the final product. Hot pressing offers the advantage of combining compaction and sintering in a single step, making it suitable for high-performance materials, while cold pressing is a simpler and more cost-effective method for less demanding applications.
Summary Table:
Aspect | Hot Pressing | Cold Pressing |
---|---|---|
Temperature | Elevated (500°C to 2000°C) | Room temperature |
Process Integration | Compaction and sintering in one step | Compaction and sintering performed separately |
Material Suitability | High-density materials (ceramics, refractory metals, composites) | Simpler shapes and materials (metals, alloys) |
Equipment | Specialized, high-temperature and pressure-resistant | Simpler and less expensive |
Applications | Cutting tools, aerospace components, electronic substrates | Automotive parts, household items, bearings |
Need help choosing the right pressing technique for your materials? Contact our experts today!