Induction heating and resistance heating are two distinct methods of generating heat, each with unique mechanisms and applications. Induction heating relies on electromagnetic induction to generate heat directly within a conductive material, using alternating currents to create eddy currents that produce heat internally. This method is contactless, rapid, and precise, making it ideal for applications requiring localized heating or contamination-free environments. Resistance heating, on the other hand, generates heat by passing an electric current through a resistive material, which then conducts heat to the target object. This method is often used in applications where consistent and uniform heating is required. Below, the key differences and principles of these two heating methods are explained in detail.
Key Points Explained:
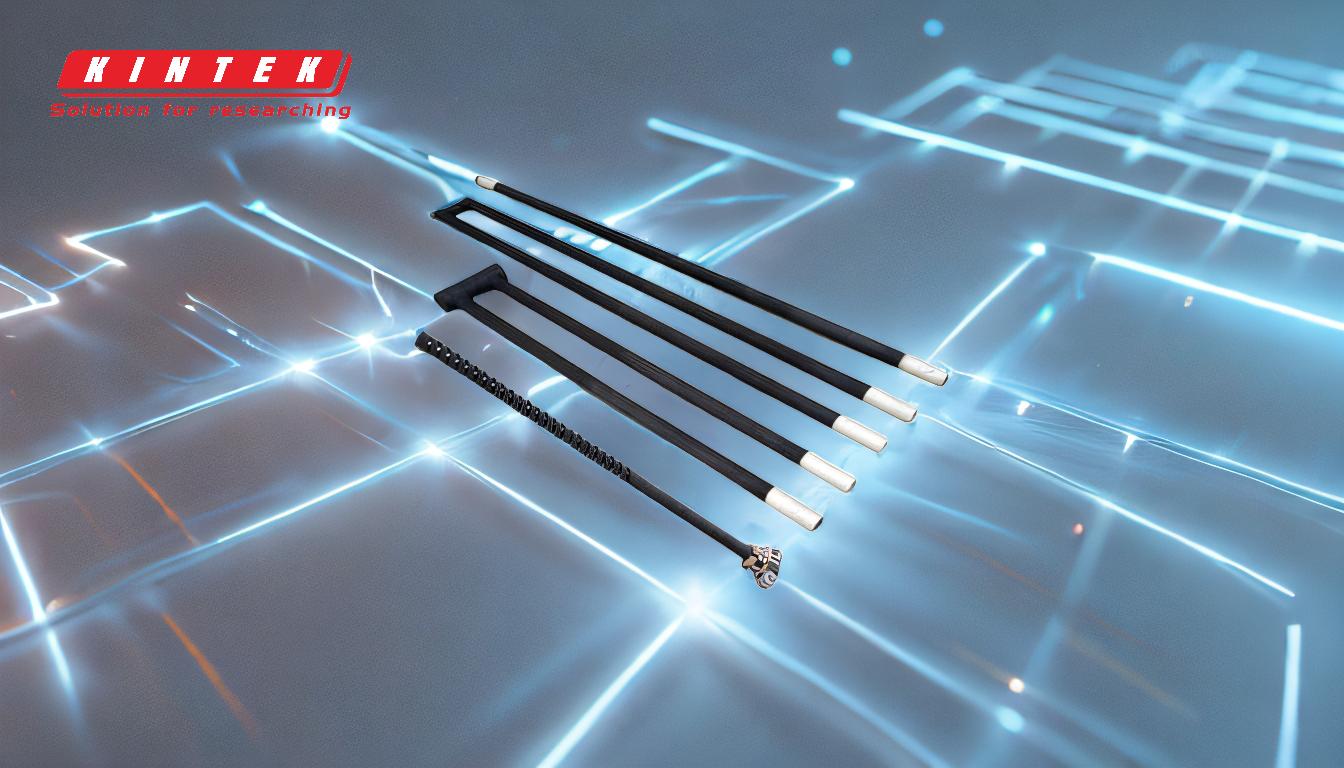
-
Mechanism of Heat Generation:
-
Induction Heating:
- Heat is generated internally within the conductive material through electromagnetic induction.
- An alternating current in a coil creates a transient magnetic field, inducing eddy currents in the conductive material.
- These eddy currents generate heat due to the material's electrical resistance.
-
Resistance Heating:
- Heat is generated externally by passing an electric current through a resistive element (e.g., a coil or wire).
- The resistive element heats up due to its inherent resistance, and this heat is then transferred to the target object via conduction.
-
Induction Heating:
-
Contact vs. Non-Contact Heating:
-
Induction Heating:
- Non-contact method: Heat is induced directly within the material without physical contact.
- Ideal for applications where contamination or physical contact with the heating source is undesirable.
-
Resistance Heating:
- Contact method: Heat is generated in a separate resistive element and then transferred to the target object.
- Requires physical contact or proximity between the heating element and the object being heated.
-
Induction Heating:
-
Speed and Precision:
-
Induction Heating:
- Rapid heating: Heat is generated directly within the material, allowing for quick temperature rises.
- Precise control: Heating can be localized to specific areas or depths by adjusting the frequency of the alternating current.
-
Resistance Heating:
- Slower heating: Heat transfer depends on conduction, which can be slower compared to induction heating.
- Less precise: Heating is typically more uniform and less localized, making it suitable for applications requiring consistent temperatures.
-
Induction Heating:
-
Applications:
-
Induction Heating:
- Used in processes like induction soldering, induction sintering, and surface hardening.
- Ideal for applications requiring rapid, localized heating or where contamination must be avoided (e.g., in vacuum environments).
-
Resistance Heating:
- Commonly used in electric furnaces, space heaters, and industrial heating systems.
- Suitable for applications requiring uniform and consistent heating over larger areas.
-
Induction Heating:
-
Energy Efficiency:
-
Induction Heating:
- Highly efficient for localized heating, as energy is directly converted into heat within the target material.
- Minimal energy loss compared to resistance heating, especially in applications requiring rapid heating.
-
Resistance Heating:
- Efficient for uniform heating but may experience energy losses due to heat transfer through conduction.
- Less efficient for localized heating compared to induction heating.
-
Induction Heating:
-
Equipment Design:
-
Induction Heating:
- Typically involves a coil and a power supply to generate alternating currents.
- The heating element (coil) and the target material are separate, allowing for flexible and versatile designs.
-
Resistance Heating:
- Involves a resistive element (e.g., a coil or wire) and a power supply.
- Often designed as a two-piece system, where the heater and the target object are distinct components.
-
Induction Heating:
-
Environmental Considerations:
-
Induction Heating:
- Cleaner process: No open flames or external heat sources, reducing the risk of contamination.
- Suitable for vacuum or controlled environments where contamination must be minimized.
-
Resistance Heating:
- May involve external heat sources or open flames, depending on the design.
- More prone to contamination in sensitive environments.
-
Induction Heating:
By understanding these key differences, equipment and consumable purchasers can make informed decisions about which heating method best suits their specific needs, whether it be for rapid, localized heating or consistent, uniform heating.
Summary Table:
Aspect | Induction Heating | Resistance Heating |
---|---|---|
Mechanism | Heat generated internally via electromagnetic induction | Heat generated externally by passing current through a resistive element |
Contact | Non-contact method, ideal for contamination-free environments | Contact method, requires physical contact or proximity |
Speed & Precision | Rapid and precise, suitable for localized heating | Slower and less precise, ideal for uniform heating |
Applications | Induction soldering, sintering, surface hardening | Electric furnaces, space heaters, industrial heating |
Energy Efficiency | Highly efficient for localized heating | Efficient for uniform heating, less efficient for localized heating |
Equipment Design | Coil and power supply, flexible designs | Resistive element and power supply, two-piece system |
Environmental Impact | Cleaner, suitable for vacuum or controlled environments | Prone to contamination in sensitive environments |
Still unsure which heating method is best for your application? Contact our experts today for personalized advice!