The difference between injection molding and pressure molding lies in their processes, mechanisms, and applications. Injection molding involves injecting molten material into a mold cavity under high pressure, where it cools and solidifies into the desired shape. Pressure molding, on the other hand, uses a combination of heat and pressure to shape materials, often without the need for injecting molten material. Both methods are widely used in manufacturing, but their suitability depends on the material, design complexity, and production requirements.
Key Points Explained:
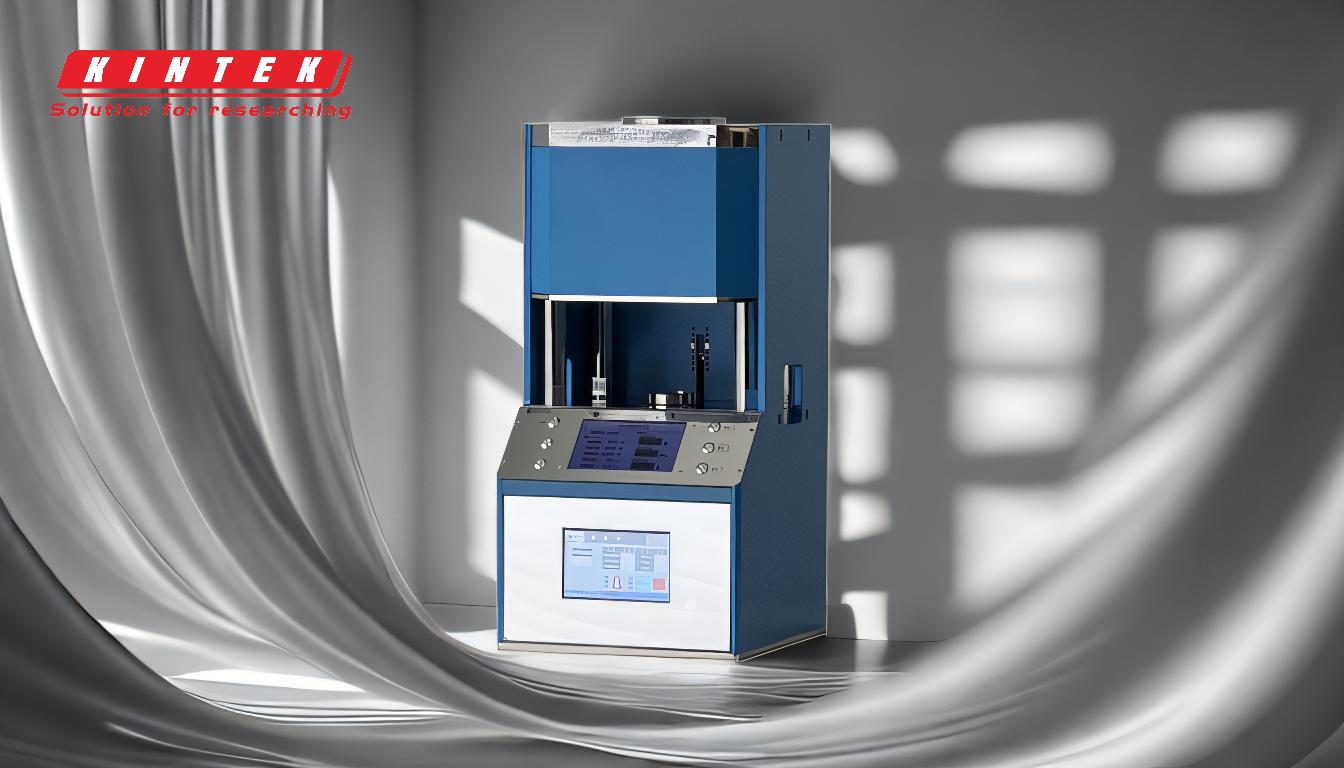
-
Process Mechanism:
- Injection Molding: This process involves melting a material (typically plastic) and injecting it into a mold under high pressure. The material fills the mold cavity, cools, and solidifies to form the final product. It is a highly automated and efficient process suitable for high-volume production.
- Pressure Molding: This method applies heat and pressure to a material (often thermosetting plastics or composites) to shape it into a mold. Unlike injection molding, the material is not necessarily melted but is softened and formed under pressure. It is often used for materials that require curing or setting under pressure.
-
Material Suitability:
- Injection Molding: Best suited for thermoplastics, which can be melted and reshaped multiple times. Common materials include polyethylene, polypropylene, and ABS.
- Pressure Molding: Ideal for thermosetting materials, which undergo a chemical change during molding and cannot be remelted. Examples include phenolic resins and epoxy composites.
-
Design Complexity:
- Injection Molding: Capable of producing highly complex and intricate parts with fine details. It is suitable for parts with thin walls, undercuts, and complex geometries.
- Pressure Molding: Better suited for simpler shapes and larger parts. It is often used for components that require high strength and durability, such as automotive parts or electrical insulators.
-
Production Volume:
- Injection Molding: Highly efficient for large-scale production due to its automation and fast cycle times. It is cost-effective for producing thousands or millions of identical parts.
- Pressure Molding: Typically used for lower to medium production volumes. It is more labor-intensive and has longer cycle times compared to injection molding.
-
Tooling and Equipment:
- Injection Molding: Requires specialized equipment, such as injection molding machines and precision molds. The initial setup cost is high, but the per-unit cost decreases with volume.
- Pressure Molding: Utilizes presses and molds designed to withstand high pressure and heat. The equipment is generally less complex than injection molding machines, but the molds may still require significant investment.
-
Applications:
- Injection Molding: Commonly used in industries such as automotive, consumer goods, medical devices, and electronics for producing parts like housings, containers, and gears.
- Pressure Molding: Often employed in industries requiring high-strength components, such as aerospace, electrical, and heavy machinery. Examples include circuit breakers, insulators, and structural parts.
In summary, the choice between injection molding and pressure molding depends on the material, design requirements, production volume, and application. Injection molding is ideal for high-volume, complex parts made from thermoplastics, while pressure molding is better suited for high-strength, durable components made from thermosetting materials.
Summary Table:
Aspect | Injection Molding | Pressure Molding |
---|---|---|
Process Mechanism | Melts and injects material into a mold under high pressure. | Uses heat and pressure to shape materials without injecting molten material. |
Material Suitability | Best for thermoplastics (e.g., polyethylene, polypropylene). | Ideal for thermosetting materials (e.g., phenolic resins, epoxy composites). |
Design Complexity | Suitable for complex, intricate parts with fine details. | Better for simpler shapes and larger, high-strength components. |
Production Volume | High-volume production with fast cycle times. | Lower to medium production volumes with longer cycle times. |
Tooling and Equipment | Requires specialized machines and precision molds. | Uses presses and molds designed for high pressure and heat. |
Applications | Automotive, consumer goods, medical devices, electronics. | Aerospace, electrical, heavy machinery for high-strength parts. |
Need help choosing the right molding process for your project? Contact our experts today!