IP (Ion Plating) and PVD (Physical Vapor Deposition) are both advanced surface coating techniques used to enhance the durability, appearance, and functionality of materials. While they share similarities, they differ significantly in terms of process, application, and outcomes. IP is a subset of PVD, incorporating additional ion bombardment to improve adhesion and coating quality. PVD, on the other hand, is a broader category that includes various methods like sputtering and evaporation. Both techniques are environmentally friendly compared to traditional electroplating, but PVD offers greater versatility in material deposition. Below, we explore the key differences between IP and PVD plating in detail.
Key Points Explained:
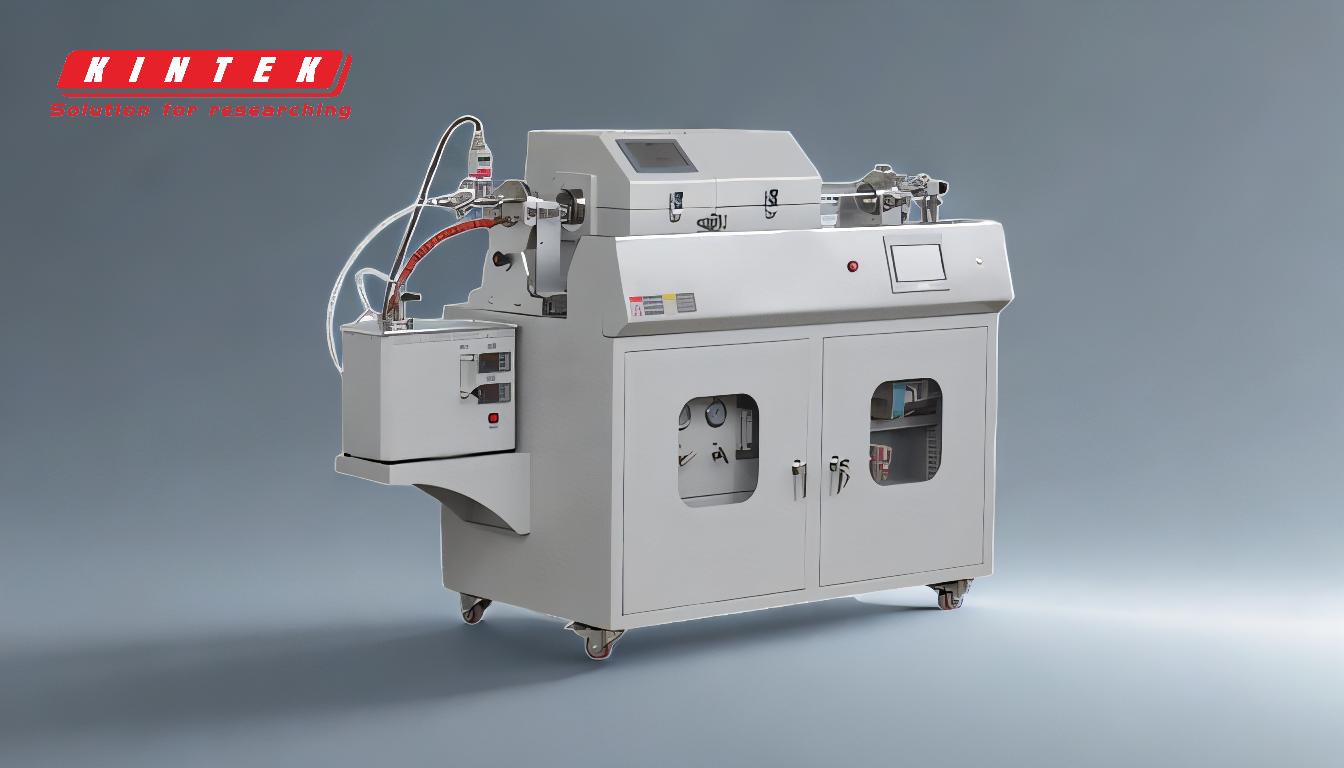
-
Process Mechanisms:
-
PVD (Physical Vapor Deposition):
- Involves vaporizing a solid material (e.g., metals, alloys, or ceramics) in a vacuum chamber and depositing it onto a substrate as a thin film.
- Techniques include sputtering, evaporation, and arc vaporization.
- The process is purely physical, relying on high temperatures and vacuum conditions.
-
IP (Ion Plating):
- A specialized form of PVD that incorporates ion bombardment during the deposition process.
- Ions are used to clean and activate the substrate surface, improving adhesion and coating uniformity.
- Combines physical vaporization with chemical reactions, making it a hybrid process.
-
PVD (Physical Vapor Deposition):
-
Material Versatility:
-
PVD:
- Can deposit a wide range of materials, including metals (e.g., gold, titanium), alloys, and ceramics.
- Suitable for applications requiring high wear resistance and aesthetic finishes.
-
IP:
- Primarily used for metals and alloys, with a focus on improving adhesion and coating density.
- Less versatile in terms of material options compared to PVD.
-
PVD:
-
Coating Properties:
-
PVD:
- Produces coatings that are less dense and less uniform compared to IP.
- Faster application but may require post-processing for improved adhesion.
-
IP:
- Results in denser, more uniform coatings due to ion bombardment.
- Enhanced adhesion and durability, making it ideal for high-stress applications.
-
PVD:
-
Environmental Impact:
-
PVD:
- Environmentally friendly, as it does not release harmful chemicals into the atmosphere.
- Does not require clear top coats, reducing the risk of tarnishing or corrosion.
-
IP:
- Similar environmental benefits to PVD, with no harmful emissions.
- The ion bombardment process may require additional energy, but it remains a clean technology.
-
PVD:
-
Applications:
-
PVD:
- Widely used in industries such as automotive, aerospace, jewelry, and electronics.
- Ideal for decorative finishes, wear-resistant coatings, and corrosion protection.
-
IP:
- Commonly used in high-performance applications, such as cutting tools, medical devices, and precision components.
- Preferred for coatings requiring exceptional adhesion and durability.
-
PVD:
-
Cost and Efficiency:
-
PVD:
- Generally faster and more cost-effective for large-scale production.
- Suitable for applications where coating uniformity is less critical.
-
IP:
- More expensive due to the additional ion bombardment step.
- Slower process but delivers superior coating quality, justifying the higher cost for critical applications.
-
PVD:
-
Durability and Performance:
-
PVD:
- Offers excellent wear resistance and corrosion protection.
- Coatings are durable but may require thicker layers for high-stress applications.
-
IP:
- Provides superior durability and wear resistance due to the denser, more adherent coatings.
- Ideal for applications where long-term performance is critical.
-
PVD:
In summary, while both IP and PVD plating are advanced coating techniques, they cater to different needs and applications. PVD is more versatile and cost-effective, making it suitable for a wide range of industries. IP, on the other hand, excels in high-performance applications where coating adhesion and durability are paramount. Understanding these differences is crucial for selecting the right technique based on specific project requirements.
Summary Table:
Aspect | PVD (Physical Vapor Deposition) | IP (Ion Plating) |
---|---|---|
Process Mechanisms | Vaporizes solid materials in a vacuum; includes sputtering, evaporation, and arc vaporization. | Combines PVD with ion bombardment for better adhesion and coating uniformity. |
Material Versatility | Deposits metals, alloys, and ceramics; highly versatile. | Primarily used for metals and alloys; less versatile. |
Coating Properties | Less dense and less uniform coatings; faster application. | Denser, more uniform coatings with enhanced adhesion and durability. |
Environmental Impact | Environmentally friendly; no harmful emissions. | Similar to PVD; clean technology with no harmful emissions. |
Applications | Automotive, aerospace, jewelry, electronics (decorative and wear-resistant coatings). | High-performance applications like cutting tools, medical devices, and precision components. |
Cost and Efficiency | Faster and more cost-effective for large-scale production. | More expensive due to ion bombardment; slower but superior quality for critical uses. |
Durability | Excellent wear resistance and corrosion protection; thicker layers for high-stress applications. | Superior durability and wear resistance; ideal for long-term performance. |
Need help choosing the right coating technique for your project? Contact our experts today for personalized guidance!