Laser melting and sintering are two distinct processes used in additive manufacturing and material processing, differing primarily in how they combine materials. Laser melting involves heating a material to its melting point, turning it into a liquid state, and then solidifying it to form a solid structure. In contrast, sintering uses heat and pressure to fuse particles together without reaching the material's melting point, allowing for bonding at lower temperatures. Laser melting is ideal for creating dense, high-strength parts, while sintering is better suited for producing porous or complex geometries. Both processes have unique advantages depending on the application, material, and desired properties of the final product.
Key Points Explained:
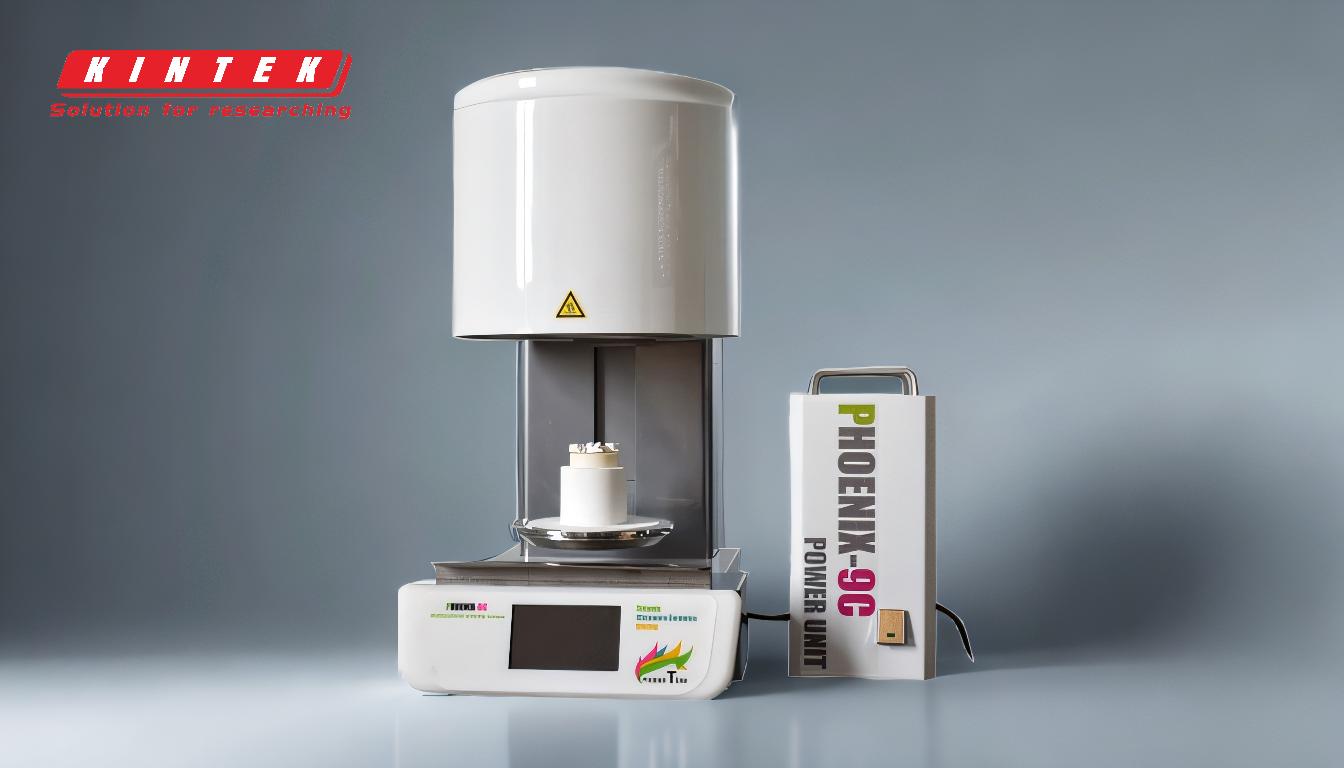
-
Definition and Process Differences:
- Laser Melting: Involves heating a material to its melting point, turning it into a liquid, and then solidifying it to form a solid structure. This process is often used in additive manufacturing to create dense, high-strength parts.
- Sintering: Uses heat and pressure to fuse particles together without reaching the material's melting point. This allows for bonding at lower temperatures, making it suitable for materials with high melting points or for creating porous structures.
-
Temperature Requirements:
- Laser Melting: Requires the material to reach its melting point, which is typically a higher temperature. This ensures complete liquefaction of the material.
- Sintering: Occurs at temperatures just below the material's melting point, allowing particles to bond without liquefying. This makes it more energy-efficient and suitable for materials that are difficult to melt.
-
Material Properties and Applications:
- Laser Melting: Produces dense, high-strength parts with minimal porosity. It is ideal for applications requiring high mechanical strength, such as aerospace or medical implants.
- Sintering: Creates parts with controlled porosity or complex geometries. It is often used in applications like filters, bearings, or lightweight structural components.
-
Additive Manufacturing Context:
- Laser Melting: Commonly used in processes like Selective Laser Melting (SLM) or Direct Metal Laser Sintering (DMLS), where a laser fully melts the powder to create solid layers.
- Sintering: Used in Selective Laser Sintering (SLS), where the laser partially melts or fuses powder particles to build layers without full liquefaction.
-
Advantages and Limitations:
-
Laser Melting:
- Advantages: High density, excellent mechanical properties, and the ability to work with a wide range of materials.
- Limitations: Higher energy consumption, slower production rates, and potential for thermal stress or distortion.
-
Sintering:
- Advantages: Lower energy consumption, ability to process high-melting-point materials, and suitability for creating porous or complex structures.
- Limitations: Lower density and mechanical strength compared to melted parts, and potential for incomplete bonding.
-
Laser Melting:
-
Cost and Production Considerations:
- Laser Melting: Generally more expensive due to higher energy requirements and slower production rates. It is less suited for mass production but ideal for high-value, low-volume parts.
- Sintering: More cost-effective for mass production and suitable for creating parts with specific functional properties, such as porosity or lightweight designs.
By understanding these key differences, manufacturers and purchasers can choose the appropriate process based on the material, desired properties, and application requirements.
Summary Table:
Aspect | Laser Melting | Sintering |
---|---|---|
Process | Heats material to melting point, solidifies to form dense structures. | Uses heat and pressure to fuse particles without melting. |
Temperature | Requires reaching the material's melting point. | Occurs below the melting point, energy-efficient. |
Material Properties | Produces dense, high-strength parts with minimal porosity. | Creates porous or complex geometries with controlled porosity. |
Applications | Ideal for aerospace, medical implants, and high-strength components. | Used for filters, bearings, and lightweight structural components. |
Advantages | High density, excellent mechanical properties, versatile material use. | Lower energy consumption, suitable for high-melting-point materials. |
Limitations | Higher energy use, slower production, potential thermal stress. | Lower density, potential for incomplete bonding. |
Cost | More expensive, suited for high-value, low-volume parts. | Cost-effective for mass production and functional properties. |
Need help choosing between laser melting and sintering for your project? Contact our experts today!