Muffle furnaces and induction furnaces are both used for high-temperature applications but differ significantly in their heating mechanisms, design, and applications. Muffle furnaces use electrically heated refractory elements within a solid metal container, allowing them to achieve higher temperatures and power densities. They are commonly used in laboratories for small-scale, batch processes like heat treatment and elemental analysis. In contrast, induction furnaces rely on electromagnetic fields to heat materials directly, making them more suitable for industrial applications like metal melting. The key differences lie in their heating methods, temperature ranges, and operational scales.
Key Points Explained:
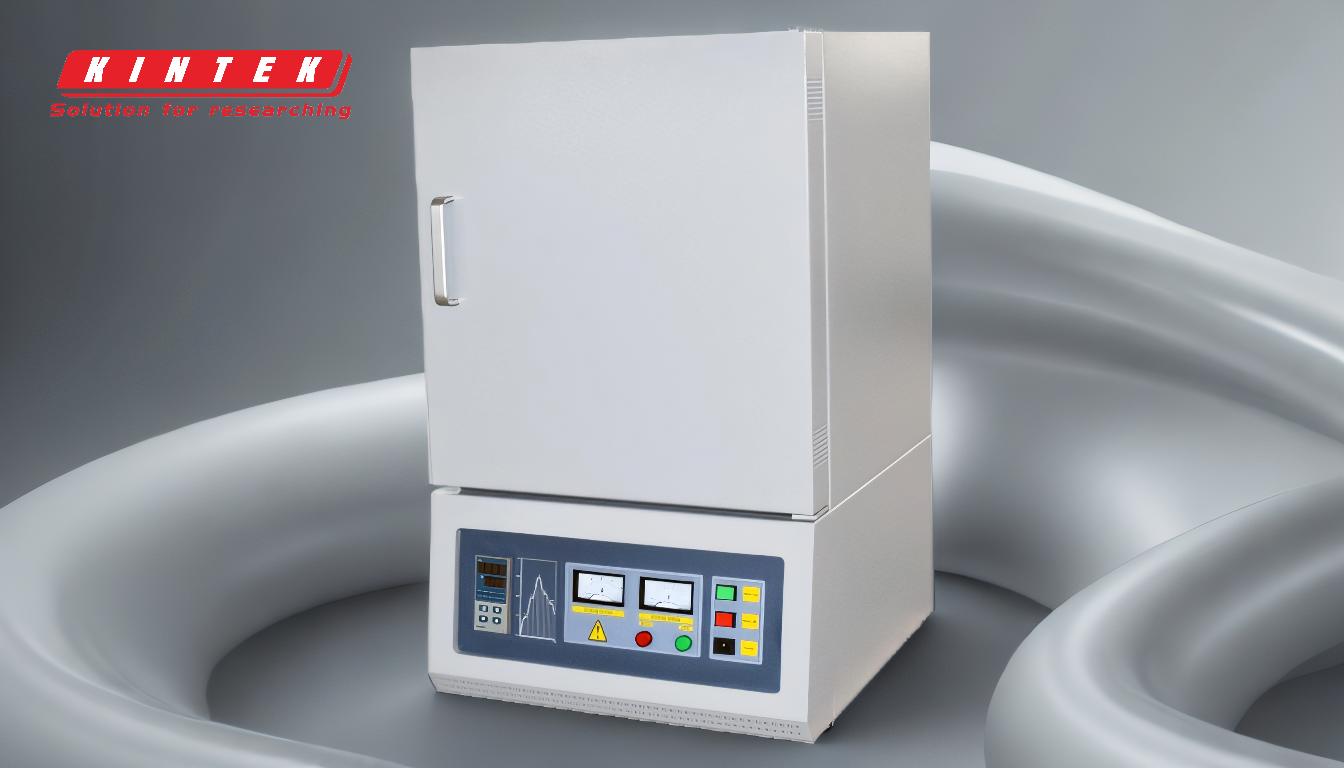
-
Heating Mechanism:
- Muffle Furnace: Uses electrically heated refractory elements within a solid metal container. The heat is transferred to the material indirectly through the walls of the container.
- Induction Furnace: Utilizes electromagnetic fields to generate heat directly within the material. This method is more efficient for heating conductive materials like metals.
-
Temperature Range and Power Density:
- Muffle Furnace: Can operate at higher temperatures and with greater power densities compared to induction furnaces. This makes them suitable for applications requiring extreme heat, such as sintering and elemental analysis.
- Induction Furnace: Typically operates at lower temperatures and is more efficient for processes like metal melting, where precise temperature control is crucial.
-
Design and Application:
- Muffle Furnace: Designed for small-scale, batch processes, often used in laboratories. Features include programmable temperature control and data acquisition capabilities. They are ideal for applications like heat treatment of small steel samples and detecting elements in coal.
- Induction Furnace: Generally larger and used in industrial settings for continuous processes. They are more suited for high-volume production tasks, such as metal casting and alloy production.
-
Operational Scale:
- Muffle Furnace: Best for discontinuous, batch processes in controlled environments. They offer quick heating and good temperature consistency, making them ideal for research and small-scale production.
- Induction Furnace: Designed for continuous, large-scale industrial operations. They are more efficient for high-throughput processes and can handle larger volumes of material.
-
Control and Automation:
- Muffle Furnace: Often equipped with advanced control systems, including programmable temperature settings and data logging. This allows for precise control over the heating process, which is essential for laboratory experiments and small-scale production.
- Induction Furnace: Can be operated manually or automatically, with a focus on maintaining consistent temperatures over long periods. This is crucial for industrial processes where continuous operation is required.
-
Material Compatibility:
- Muffle Furnace: Suitable for a wide range of materials, including metals, ceramics, and organic compounds. The indirect heating method allows for uniform heating without direct contact with the heat source.
- Induction Furnace: Primarily used for conductive materials like metals. The direct heating method is highly efficient for these materials but may not be suitable for non-conductive substances.
In summary, while both muffle and induction furnaces are used for high-temperature applications, their differences in heating mechanisms, temperature capabilities, and operational scales make them suitable for distinct purposes. Muffle furnaces excel in laboratory settings for precise, small-scale processes, whereas induction furnaces are better suited for industrial, high-volume metal processing tasks.
Summary Table:
Feature | Muffle Furnace | Induction Furnace |
---|---|---|
Heating Mechanism | Electrically heated refractory elements | Electromagnetic fields |
Temperature Range | Higher temperatures | Lower temperatures |
Applications | Laboratories, small-scale processes | Industrial, metal melting |
Operational Scale | Batch processes | Continuous, high-volume production |
Material Compatibility | Metals, ceramics, organics | Primarily conductive materials |
Need help choosing the right furnace for your application? Contact our experts today!