Physical and chemical deposition are two distinct methods used to create thin films or coatings on substrates, each with unique processes, mechanisms, and applications. Physical vapor deposition (PVD) relies on physical processes such as evaporation, sputtering, or sublimation to transfer material from a solid source to a substrate. In contrast, chemical vapor deposition (CVD) involves chemical reactions between gaseous precursors and the substrate to form a solid film. The key differences lie in the source materials, reaction mechanisms, and the nature of the deposition process. CVD often requires higher temperatures and involves complex chemical reactions, while PVD operates at lower temperatures and focuses on physical transformations. Both methods have specific advantages and are chosen based on the desired film properties, substrate compatibility, and application requirements.
Key Points Explained:
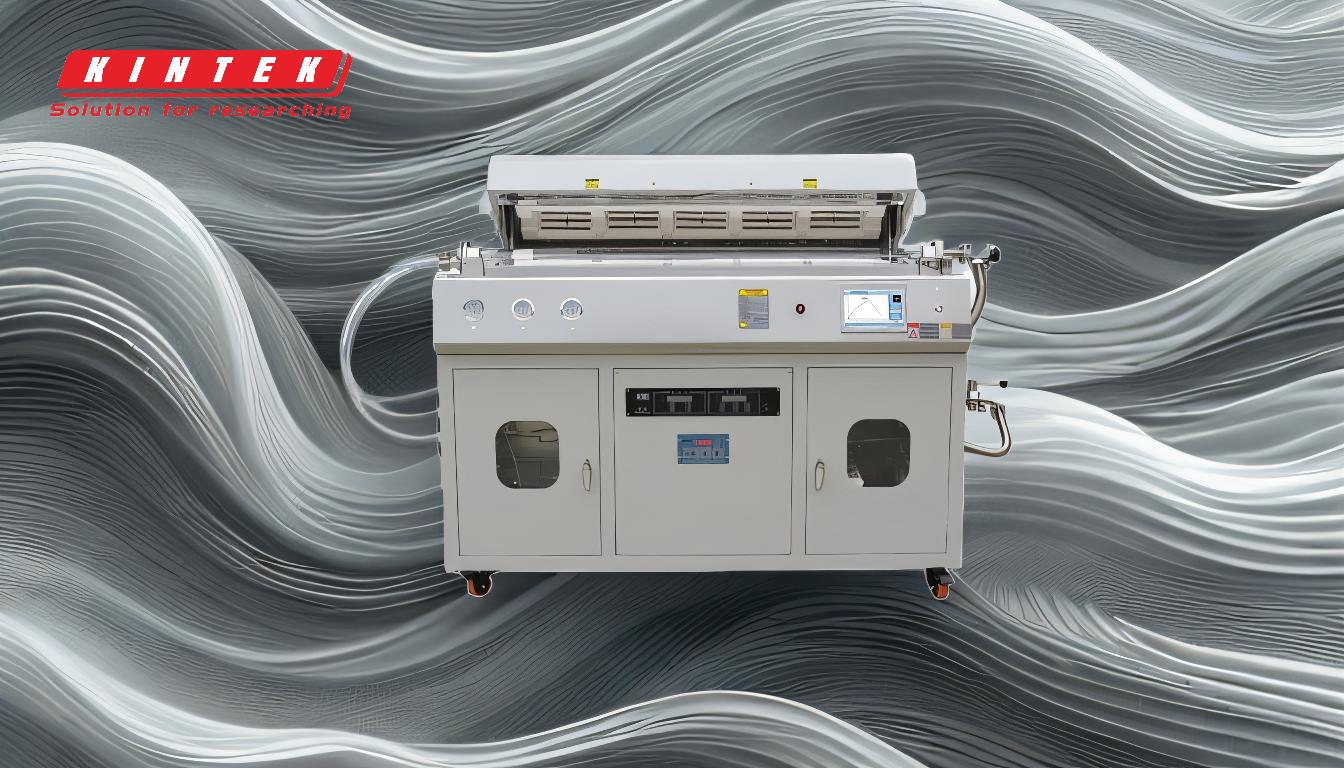
-
Source Materials:
- PVD: Uses solid materials (targets) that are vaporized through physical processes like evaporation, sputtering, or sublimation. The vaporized atoms or molecules then condense onto the substrate to form a thin film.
- CVD: Utilizes gaseous precursors that chemically react or decompose on the substrate surface to form a solid film. The gaseous precursors are often introduced into a reaction chamber under controlled conditions.
-
Deposition Mechanisms:
-
PVD: Involves physical processes such as:
- Evaporation: Heating the target material until it vaporizes.
- Sputtering: Bombarding the target with ions to eject atoms or molecules.
- Sublimation: Direct transition of the target material from solid to vapor. These processes do not involve chemical reactions.
-
CVD: Relies on chemical reactions, such as:
- Decomposition of gaseous precursors on the substrate surface.
- Reactions between multiple gaseous precursors to form a solid film. These reactions are often thermally or plasma-activated.
-
PVD: Involves physical processes such as:
-
Temperature Requirements:
- PVD: Typically operates at lower temperatures compared to CVD, making it suitable for temperature-sensitive substrates.
- CVD: Often requires higher temperatures to facilitate chemical reactions, although plasma-enhanced CVD (PECVD) can lower the temperature requirements by using plasma to activate the precursors.
-
Film Properties:
- PVD: Produces films with high purity and excellent adhesion. The process is ideal for creating dense, uniform coatings with precise control over thickness.
- CVD: Can produce films with complex compositions and structures, including organic and inorganic materials. The chemical reactions allow for the creation of films with unique properties, such as high conformality and step coverage.
-
Applications:
- PVD: Commonly used for decorative coatings, wear-resistant coatings, and semiconductor applications. It is also used in optical coatings and thin-film solar cells.
- CVD: Widely used in the semiconductor industry for creating dielectric layers, conductive layers, and protective coatings. It is also used in the production of graphene, carbon nanotubes, and other advanced materials.
-
Process Complexity:
- PVD: Generally simpler and more straightforward, with fewer variables to control. The process is often faster and more cost-effective for certain applications.
- CVD: More complex due to the involvement of chemical reactions, requiring precise control over parameters such as temperature, pressure, and gas flow rates. This complexity allows for greater versatility in film properties and applications.
-
Equipment and Techniques:
- PVD: Techniques include thermal evaporation, electron-beam evaporation, magnetron sputtering, and arc vapor deposition. The equipment is designed to handle solid targets and create a vacuum environment.
- CVD: Techniques include atmospheric pressure CVD (APCVD), low-pressure CVD (LPCVD), and plasma-enhanced CVD (PECVD). The equipment is designed to handle gaseous precursors and often includes systems for gas delivery, reaction chambers, and exhaust management.
By understanding these key differences, equipment and consumable purchasers can make informed decisions about which deposition method is best suited for their specific needs, whether it involves creating high-purity coatings, complex material structures, or temperature-sensitive applications.
Summary Table:
Aspect | PVD | CVD |
---|---|---|
Source Materials | Solid targets (evaporation, sputtering, sublimation) | Gaseous precursors (chemical reactions) |
Deposition Mechanisms | Physical processes (evaporation, sputtering, sublimation) | Chemical reactions (decomposition, precursor reactions) |
Temperature | Lower temperatures, suitable for sensitive substrates | Higher temperatures, reduced with plasma-enhanced CVD (PECVD) |
Film Properties | High purity, excellent adhesion, dense coatings | Complex compositions, high conformality, step coverage |
Applications | Decorative coatings, wear-resistant coatings, semiconductors | Semiconductor dielectric layers, graphene, carbon nanotubes |
Process Complexity | Simpler, fewer variables, faster, cost-effective | More complex, precise control of temperature, pressure, gas flow |
Equipment | Thermal evaporation, magnetron sputtering, arc vapor deposition | APCVD, LPCVD, PECVD with gas delivery and reaction chambers |
Need help choosing the right deposition method for your application? Contact our experts today!