Regeneration and reactivation of carbon are terms often used interchangeably, but they refer to specific processes aimed at restoring the adsorption capacity of activated carbon. Regeneration involves thermally or chemically treating the carbon to remove adsorbed contaminants, while reactivation typically refers to a more intensive thermal process that not only removes contaminants but also restores the carbon's porous structure. Both processes aim to extend the life of activated carbon, making it reusable and cost-effective. Understanding the nuances between these processes is crucial for selecting the right method based on the type of contaminants and the desired outcome.
Key Points Explained:
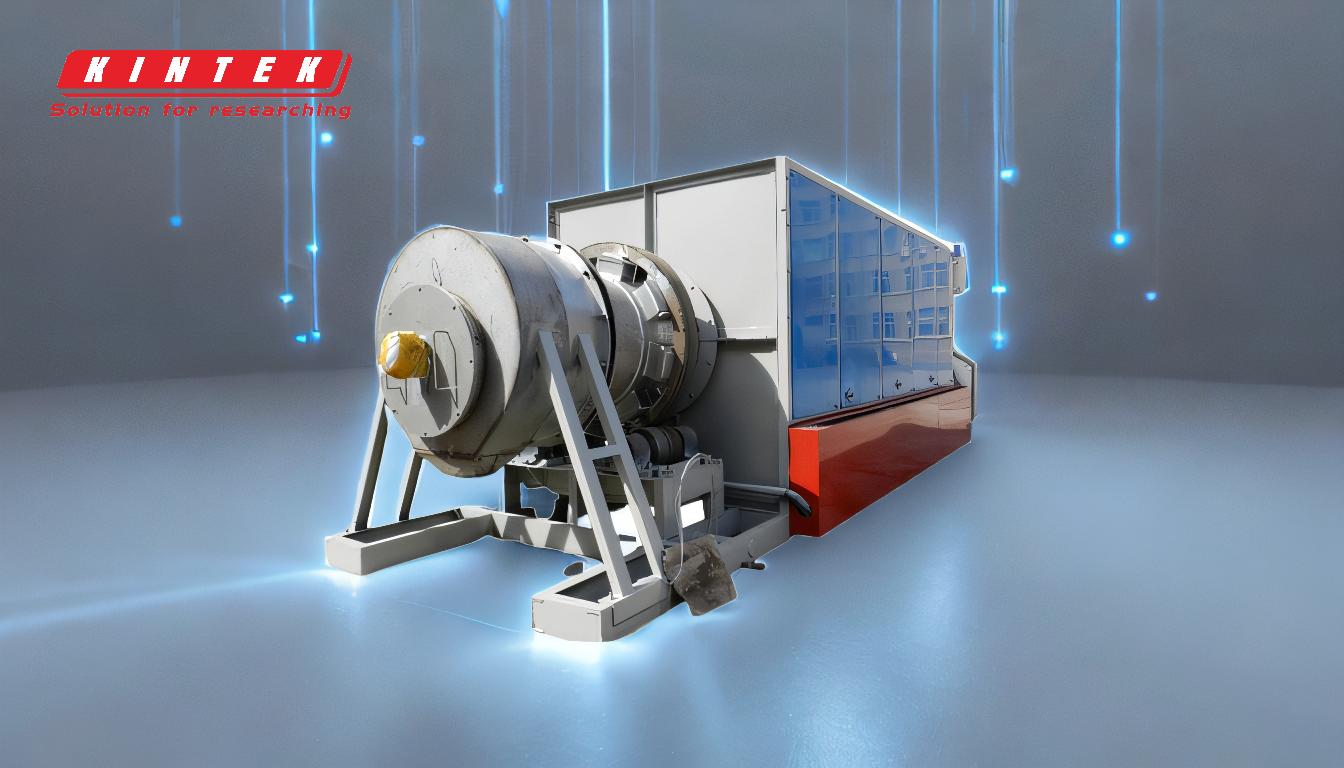
-
Definition of Regeneration:
- Regeneration is a process where adsorbed contaminants are removed from activated carbon, typically through thermal or chemical means.
- The goal is to restore the carbon's adsorption capacity without significantly altering its physical structure.
- This process is often used when the contaminants are volatile or can be easily decomposed at high temperatures.
-
Definition of Reactivation:
- Reactivation is a more intensive thermal process that not only removes adsorbed contaminants but also restores the carbon's porous structure.
- This process involves heating the carbon to very high temperatures (often above 700°C) in the presence of steam or other oxidizing agents.
- Reactivation is typically used when the carbon's pores are clogged or when the contaminants are more stubborn and require higher temperatures for removal.
-
Key Differences:
- Temperature: Regeneration usually occurs at lower temperatures (200-400°C), while reactivation requires much higher temperatures (700-900°C).
- Process Intensity: Reactivation is more intensive and can restore the carbon's adsorption capacity more effectively, but it may also lead to some loss of carbon mass.
- Outcome: Regeneration may not fully restore the carbon's original adsorption capacity, whereas reactivation aims to bring the carbon back to near-original performance.
-
Applications:
- Regeneration: Suitable for applications where the contaminants are less complex and can be removed at lower temperatures, such as in water treatment or air purification.
- Reactivation: Ideal for more challenging applications, such as in the chemical or pharmaceutical industries, where the carbon may be exposed to more complex or heavy contaminants.
-
Economic and Environmental Considerations:
- Cost: Regeneration is generally less expensive than reactivation due to the lower energy requirements.
- Environmental Impact: Reactivation, while more effective, may have a higher environmental impact due to the higher energy consumption and potential for carbon loss.
- Sustainability: Both processes contribute to the sustainability of activated carbon use by extending its life and reducing the need for new carbon production.
-
Process Selection Criteria:
- Type of Contaminants: The nature of the adsorbed contaminants will influence whether regeneration or reactivation is more appropriate.
- Desired Carbon Performance: If near-original performance is required, reactivation may be the better choice.
- Operational Constraints: Factors such as available equipment, energy costs, and environmental regulations may also play a role in the decision-making process.
By understanding these key points, a purchaser or user of activated carbon can make informed decisions about whether to opt for regeneration or reactivation, depending on their specific needs and constraints.
Summary Table:
Aspect | Regeneration | Reactivation |
---|---|---|
Temperature | 200-400°C | 700-900°C |
Process Intensity | Less intensive, removes contaminants | More intensive, restores porous structure and removes contaminants |
Outcome | Partially restores adsorption capacity | Restores near-original adsorption capacity |
Applications | Water treatment, air purification | Chemical, pharmaceutical industries |
Cost | Lower cost due to lower energy requirements | Higher cost due to higher energy consumption |
Environmental Impact | Lower environmental impact | Higher environmental impact due to energy use and potential carbon loss |
Sustainability | Extends carbon life, reduces need for new production | Extends carbon life, reduces need for new production |
Need help choosing the right process for your activated carbon? Contact our experts today!