Brazing and soldering are both metal-joining processes that use a filler material to bond components without melting the base metals. The primary difference lies in the temperature at which they are performed. Brazing occurs at higher temperatures, typically above 840°F, and results in joints that are as strong as the base materials. It is commonly used in industries such as cookware, automotive, and HVAC systems. Soldering, on the other hand, is performed at lower temperatures, below 840°F, and is often used for electrical connections and delicate work. Both processes are valuable but serve different applications based on strength requirements and thermal considerations.
Key Points Explained:
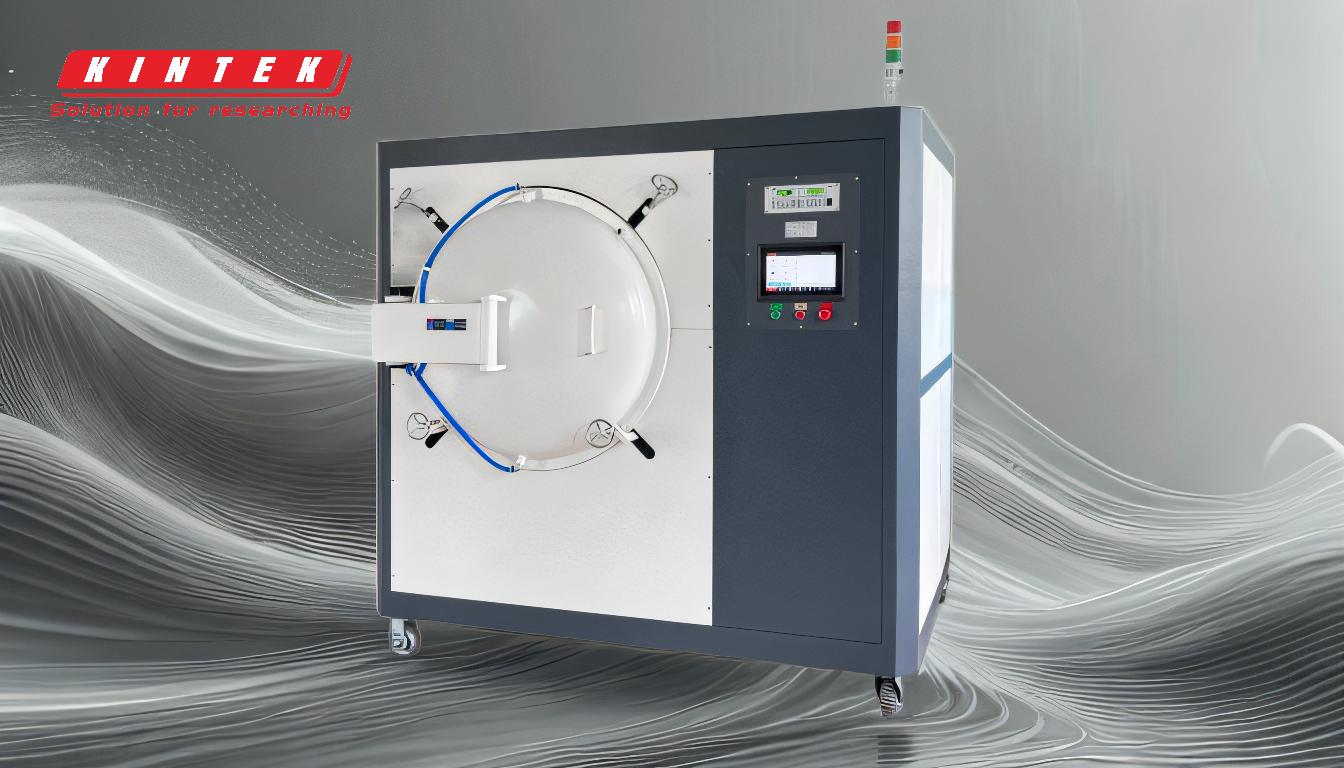
-
Temperature Range:
- Brazing: Operates at higher temperatures, typically above 840°F (450°C). This higher temperature allows the filler metal to flow more easily and create stronger bonds.
- Soldering: Performed at lower temperatures, below 840°F (450°C). This makes it suitable for delicate materials and components that cannot withstand high heat.
-
Strength of Joints:
- Brazing: Produces joints that are as strong as the base metals being joined. This is due to the higher temperatures and the metallurgical bonding that occurs.
- Soldering: Creates joints that are generally weaker compared to brazed joints. However, soldered joints are sufficient for applications where high strength is not a critical requirement, such as in electronics.
-
Applications:
- Brazing: Widely used in industries that require strong, durable joints, such as cookware, automotive, and HVAC systems. It is also used in the construction of heat exchangers and other high-stress components.
- Soldering: Commonly used in electrical and electronic applications, where the primary requirement is a reliable electrical connection rather than mechanical strength. It is also used in plumbing and jewelry making.
-
Filler Materials:
- Brazing: Typically uses filler metals such as silver, copper, and aluminum alloys. These materials have high melting points and provide strong, durable bonds.
- Soldering: Uses filler metals like tin-lead alloys, silver, and other low-melting-point materials. These fillers are chosen for their ability to flow at lower temperatures and create reliable electrical connections.
-
Process Complexity:
- Brazing: Generally requires more precise control of temperature and may involve more complex setups, such as the use of flux and controlled atmospheres to prevent oxidation.
- Soldering: Simpler and more straightforward, often requiring only a soldering iron and flux. It is easier to perform in a variety of settings, including field repairs and small-scale manufacturing.
-
Thermal Considerations:
- Brazing: The higher temperatures involved can affect the microstructure of the base metals, potentially leading to changes in their properties. This must be carefully managed to avoid compromising the integrity of the materials.
- Soldering: Lower temperatures minimize the risk of thermal damage to the base materials, making it ideal for heat-sensitive components.
In summary, while both brazing and soldering are effective metal-joining techniques, they are suited to different applications based on the required joint strength, temperature tolerance, and specific industry needs. Brazing is preferred for high-strength applications, whereas soldering is ideal for delicate and electrical work.
Summary Table:
Aspect | Brazing | Soldering |
---|---|---|
Temperature Range | Above 840°F (450°C) | Below 840°F (450°C) |
Joint Strength | As strong as base metals | Weaker than brazed joints |
Applications | Cookware, automotive, HVAC systems, heat exchangers | Electrical connections, plumbing, jewelry making |
Filler Materials | Silver, copper, aluminum alloys | Tin-lead alloys, silver, low-melting-point materials |
Process Complexity | Requires precise temperature control and may use flux/controlled atmospheres | Simpler, often using a soldering iron and flux |
Thermal Considerations | Higher temperatures may affect base metal properties | Lower temperatures minimize thermal damage to heat-sensitive components |
Need help choosing the right metal-joining process for your project? Contact our experts today!