Sputtering and e-beam (electron beam) deposition are both physical vapor deposition (PVD) techniques used to create thin films, but they differ significantly in their mechanisms, applications, and operational characteristics. Sputtering involves the ejection of atoms from a target material through momentum transfer from bombarding ions, while e-beam deposition uses a focused electron beam to evaporate the target material, which then condenses on the substrate. Both methods have unique advantages and limitations, making them suitable for different applications in industries such as semiconductors, optics, and coatings.
Key Points Explained:
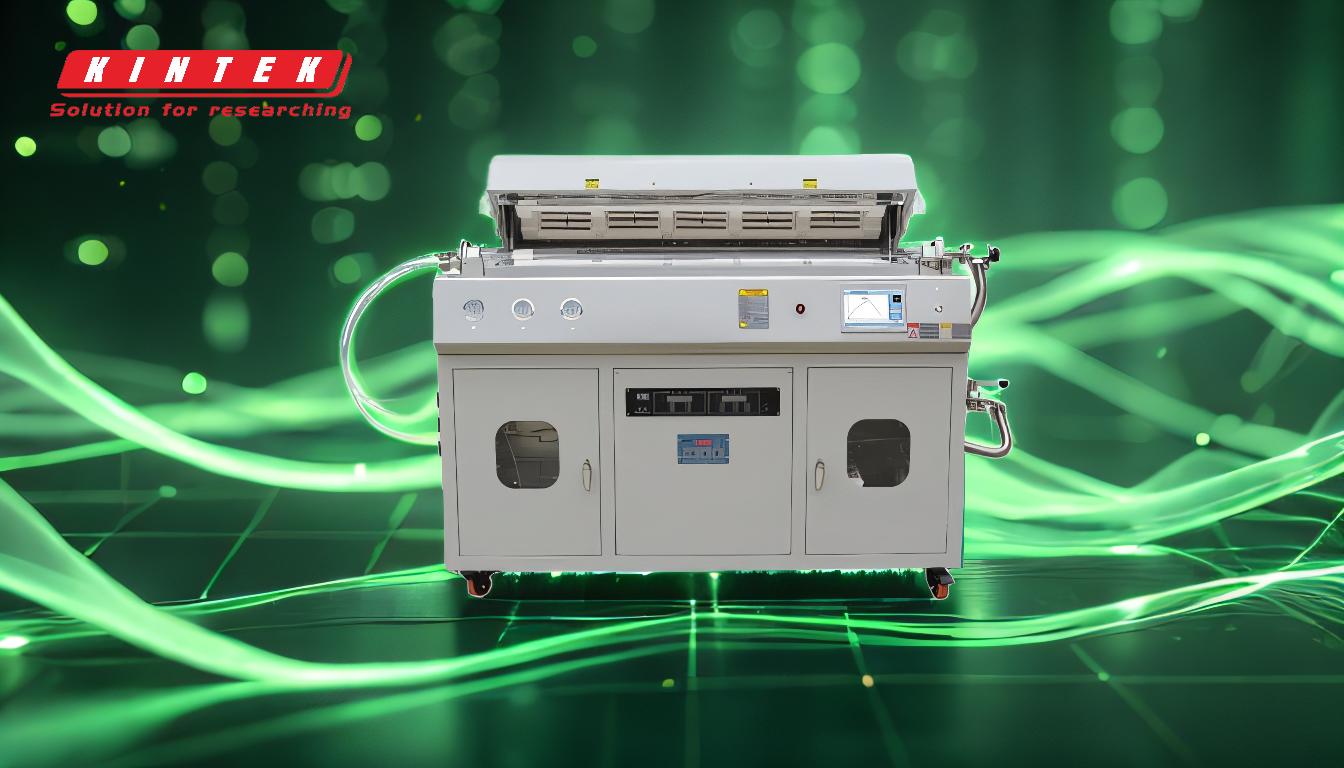
-
Mechanism of Sputtering vs. E-Beam Deposition:
- Sputtering: In sputtering, a gaseous ion (often argon) bombards the target material, causing atoms to be ejected due to momentum transfer. These ejected atoms then deposit onto the substrate to form a thin film. The process does not involve melting the target material.
- E-Beam Deposition: In e-beam deposition, a high-energy electron beam is focused on the target material, heating it to the point of evaporation. The evaporated material then condenses on the substrate to form a thin film. This method relies on thermal energy rather than momentum transfer.
-
Material Compatibility:
- Sputtering: Sputtering is versatile and can deposit a wide range of materials, including metals, alloys, and ceramics. It is particularly effective for materials with high melting points, as it does not require the target to melt.
- E-Beam Deposition: E-beam deposition is more suitable for materials with lower melting points or those that can be easily evaporated. It is less effective for materials with very high melting points or those that decompose under high heat.
-
Film Quality and Uniformity:
- Sputtering: Sputtering typically produces films with excellent uniformity and adhesion. The process allows for precise control over film thickness and composition, making it ideal for applications requiring high-quality, consistent coatings.
- E-Beam Deposition: While e-beam deposition can produce high-purity films, it may struggle with uniformity, especially for large-area substrates. The process can also introduce impurities if the target material is not sufficiently pure.
-
Deposition Rate:
- Sputtering: The deposition rate in sputtering is generally slower compared to e-beam deposition. This is due to the nature of the momentum transfer process, which is less efficient in terms of material removal.
- E-Beam Deposition: E-beam deposition typically offers higher deposition rates, as the electron beam can rapidly heat and evaporate the target material. This makes it more suitable for applications requiring rapid coating.
-
Operational Complexity and Cost:
- Sputtering: Sputtering systems are generally more complex and expensive to operate due to the need for a vacuum environment and precise control of ion bombardment. However, they offer greater flexibility in terms of material compatibility and film properties.
- E-Beam Deposition: E-beam deposition systems are simpler in design but require high-power electron guns and sophisticated cooling systems to manage the heat generated. The operational costs can be high due to the energy consumption and maintenance of the electron beam source.
-
Applications:
- Sputtering: Sputtering is widely used in the semiconductor industry for depositing thin films of metals, dielectrics, and semiconductors. It is also used in optical coatings, magnetic storage media, and decorative coatings.
- E-Beam Deposition: E-beam deposition is commonly used in the production of optical coatings, such as anti-reflective coatings, and in the deposition of high-purity metals and alloys. It is also used in research and development for creating specialized thin films.
In summary, while both sputtering and e-beam deposition are essential techniques in thin film deposition, they differ in their mechanisms, material compatibility, film quality, deposition rates, operational complexity, and applications. The choice between the two methods depends on the specific requirements of the application, including the type of material to be deposited, the desired film properties, and the operational constraints.
Summary Table:
Aspect | Sputtering | E-Beam Deposition |
---|---|---|
Mechanism | Momentum transfer from bombarding ions ejects target atoms. | High-energy electron beam evaporates the target material. |
Material Compatibility | Versatile; works with metals, alloys, and ceramics, especially high-melting-point materials. | Best for materials with lower melting points or those easily evaporated. |
Film Quality | Excellent uniformity and adhesion; precise control over thickness and composition. | High-purity films, but may struggle with uniformity on large substrates. |
Deposition Rate | Slower due to momentum transfer process. | Faster due to rapid heating and evaporation of the target material. |
Operational Complexity | More complex and expensive; requires vacuum and precise ion control. | Simpler design but requires high-power electron guns and cooling systems. |
Applications | Semiconductors, optical coatings, magnetic storage, and decorative coatings. | Optical coatings, high-purity metals, and specialized thin films. |
Need help choosing the right thin film deposition method? Contact our experts today for personalized guidance!