Thick film and thin film PCBs (Printed Circuit Boards) are two distinct technologies used in the fabrication of electronic circuits, each with its own set of characteristics, advantages, and applications. Thick film PCBs typically use screen printing to apply conductive, resistive, and insulating pastes onto a substrate, which are then fired at high temperatures to form the circuit. This method is cost-effective and suitable for producing large volumes of circuits with moderate precision. Thin film PCBs, on the other hand, involve the deposition of very thin layers of conductive and insulating materials through processes like sputtering or evaporation. This technique allows for much higher precision and finer features, making it ideal for high-frequency and high-density applications. The choice between thick film and thin film PCBs depends on factors such as the required precision, circuit complexity, production volume, and cost considerations.
Key Points Explained:
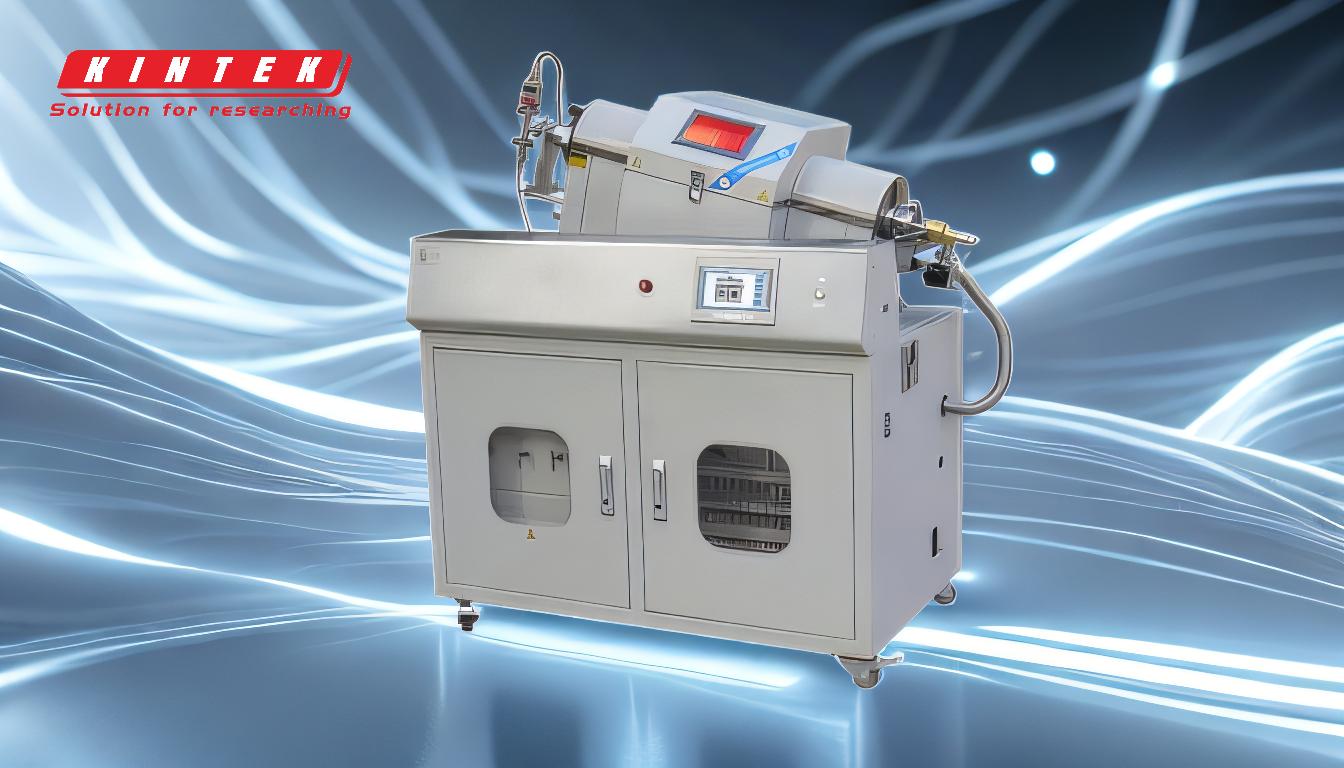
-
Manufacturing Process:
- Thick Film PCBs: These are produced using screen printing techniques where conductive, resistive, and insulating pastes are applied to a ceramic or glass substrate. The pastes are then fired at high temperatures (typically around 850°C) to form the circuit. This process is relatively simple and cost-effective, making it suitable for large-scale production.
- Thin Film PCBs: These are manufactured using advanced deposition techniques such as sputtering or evaporation. These methods allow for the deposition of very thin layers (often in the nanometer range) of conductive and insulating materials onto a substrate. This process requires more sophisticated equipment and is more expensive, but it offers higher precision and the ability to create very fine features.
-
Precision and Feature Size:
- Thick Film PCBs: The screen printing process used in thick film technology limits the minimum feature size and line width that can be achieved. Typically, the minimum line width is around 100-150 microns, which is sufficient for many applications but not for high-density circuits.
- Thin Film PCBs: Thin film technology can achieve much finer features, with line widths as small as 10 microns or less. This makes thin film PCBs suitable for applications requiring high precision and high-density interconnections, such as in RF (Radio Frequency) and microwave circuits.
-
Material Properties:
- Thick Film PCBs: The materials used in thick film technology are typically a combination of metal oxides and glass frits. These materials are chosen for their ability to withstand high firing temperatures and provide good adhesion to the substrate. However, the electrical properties of thick film materials are generally not as good as those of thin film materials.
- Thin Film PCBs: Thin film technology allows for the use of high-purity metals and dielectrics, which offer superior electrical properties. For example, thin film resistors can have much lower temperature coefficients of resistance (TCR) and better stability over time compared to thick film resistors.
-
Applications:
- Thick Film PCBs: Due to their lower cost and simpler manufacturing process, thick film PCBs are commonly used in consumer electronics, automotive applications, and industrial controls. They are also used in hybrid circuits where a combination of thick film and discrete components is required.
- Thin Film PCBs: Thin film technology is used in applications where high precision and performance are critical. This includes RF and microwave circuits, sensors, and high-frequency digital circuits. Thin film PCBs are also used in medical devices and aerospace applications where reliability and performance are paramount.
-
Cost Considerations:
- Thick Film PCBs: The cost of producing thick film PCBs is generally lower due to the simpler manufacturing process and the use of less expensive materials. This makes thick film technology more attractive for high-volume production where cost is a significant factor.
- Thin Film PCBs: The higher precision and advanced materials used in thin film technology result in higher production costs. However, the superior performance and reliability of thin film PCBs can justify the higher cost in applications where these attributes are essential.
-
Thermal and Mechanical Properties:
- Thick Film PCBs: Thick film materials are generally more robust and can withstand higher mechanical stress and thermal cycling. This makes them suitable for applications where the PCB may be subjected to harsh environmental conditions.
- Thin Film PCBs: Thin film materials, while offering superior electrical properties, may be more susceptible to mechanical stress and thermal cycling. However, the use of advanced substrates and encapsulation techniques can mitigate these issues.
In summary, the choice between thick film and thin film PCBs depends on the specific requirements of the application, including the need for precision, performance, cost, and environmental durability. Thick film technology is well-suited for cost-effective, high-volume production, while thin film technology is ideal for high-performance, high-precision applications.
Summary Table:
Aspect | Thick Film PCBs | Thin Film PCBs |
---|---|---|
Manufacturing Process | Screen printing with conductive, resistive, and insulating pastes, fired at ~850°C. | Advanced deposition techniques (sputtering/evaporation) for nanometer-thin layers. |
Precision | Minimum line width: 100-150 microns. | Minimum line width: 10 microns or less. |
Materials | Metal oxides and glass frits with moderate electrical properties. | High-purity metals and dielectrics with superior electrical properties. |
Applications | Consumer electronics, automotive, industrial controls, hybrid circuits. | RF/microwave circuits, sensors, medical devices, aerospace. |
Cost | Lower cost, suitable for high-volume production. | Higher cost, justified for high-performance applications. |
Durability | Robust, withstands mechanical stress and thermal cycling. | Susceptible to stress but mitigated with advanced substrates and encapsulation. |
Need help choosing the right PCB technology for your project? Contact us today for expert guidance!