Heat treatment, while essential for improving the mechanical properties of metals, comes with several disadvantages depending on the method used. Ordinary atmospheric heat treatment often results in surface oxidation, a harsh working environment, and limited applicability. Controlled atmosphere heat treatment, on the other hand, involves complex equipment, high costs, technical challenges, and risks like hydrogen embrittlement. Additionally, it can lead to rough surfaces, lack of surface metal elements, and difficulties in gas management. Understanding these drawbacks is crucial for selecting the appropriate heat treatment method for specific applications.
Key Points Explained:
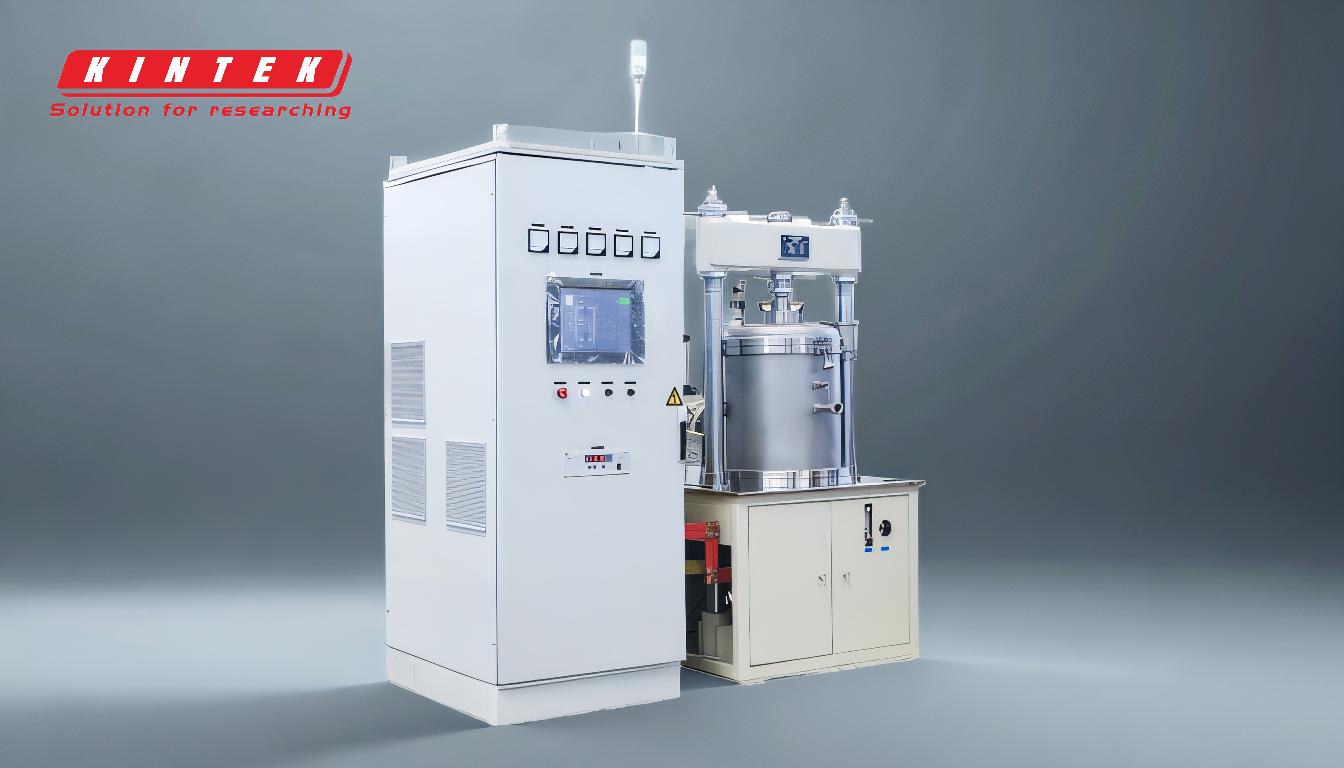
-
Disadvantages of Ordinary Atmospheric Heat Treatment:
- Oxide Film Formation: The presence of oxygen in the atmosphere leads to the formation of an oxide layer on the workpiece surface, which can affect the material's appearance and performance.
- Harsh Processing Environment: The high temperatures and exposure to atmospheric conditions can create a challenging and potentially hazardous working environment.
- Narrow Usage: This method is not suitable for all types of materials or applications, limiting its versatility.
-
Disadvantages of Controlled Atmosphere Heat Treatment:
- Complex Equipment: The machinery required for controlled atmosphere heat treatment is sophisticated and requires precise control over the environment.
- High Initial Investment: The cost of setting up and maintaining the equipment is significant, making it less accessible for smaller operations.
- High Technical Requirements: Skilled operators are needed to manage the complex processes and ensure quality outcomes.
- Risk of Hydrogen Embrittlement: Certain steel types are susceptible to hydrogen embrittlement when treated in atmospheres with high hydrogen content, which can compromise the material's integrity.
- Inability to Treat Certain Materials: Non-ferrous metals and some other materials cannot be effectively treated using controlled atmosphere methods.
-
Surface Quality Issues:
- Rough and Non-Bright Surfaces: Controlled atmosphere heat treatment often results in workpieces with less desirable surface finishes, which may require additional processing.
- Lack of Surface Metal Elements: The process can lead to a depletion of certain metal elements on the surface, affecting the material's properties.
-
Equipment and Operational Challenges:
- Corrosion of Electric Heating Elements: The harsh conditions within the heat treatment environment can lead to the erosion of critical components like heating elements.
- Gas Usage and Recovery: Managing the gases used in the process, including their recovery and treatment, presents significant logistical and technical challenges.
Understanding these disadvantages helps in making informed decisions about the heat treatment processes, balancing the benefits against the potential drawbacks to achieve the desired material properties and performance.
Summary Table:
Heat Treatment Method | Key Disadvantages |
---|---|
Ordinary Atmospheric | - Oxide film formation |
- Harsh processing environment
- Limited applicability | | Controlled Atmosphere | - Complex equipment
- High initial investment
- Risk of hydrogen embrittlement
- Rough surfaces | | Surface Quality Issues | - Rough and non-bright surfaces
- Lack of surface metal elements | | Operational Challenges | - Corrosion of heating elements
- Gas management difficulties |
Need help selecting the right heat treatment method? Contact our experts today for tailored solutions!