The effect of heating rate on the sintering mechanism of alumina nanoparticles is significant and multifaceted. A high heating rate can lead to insufficient sintering within the material, causing uneven densification and differences in sintering degrees across the blank. This results in a high-temperature melting peak and increased crystallinity. Conversely, controlled heating rates, such as those achieved with microwave heating, can promote uniform and rapid sintering, enhancing densification and reducing sintering time. The heating rate directly influences the densification process, particle rearrangement, and porosity elimination, with smaller particles and homogeneous compositions further improving sintering outcomes.
Key Points Explained:
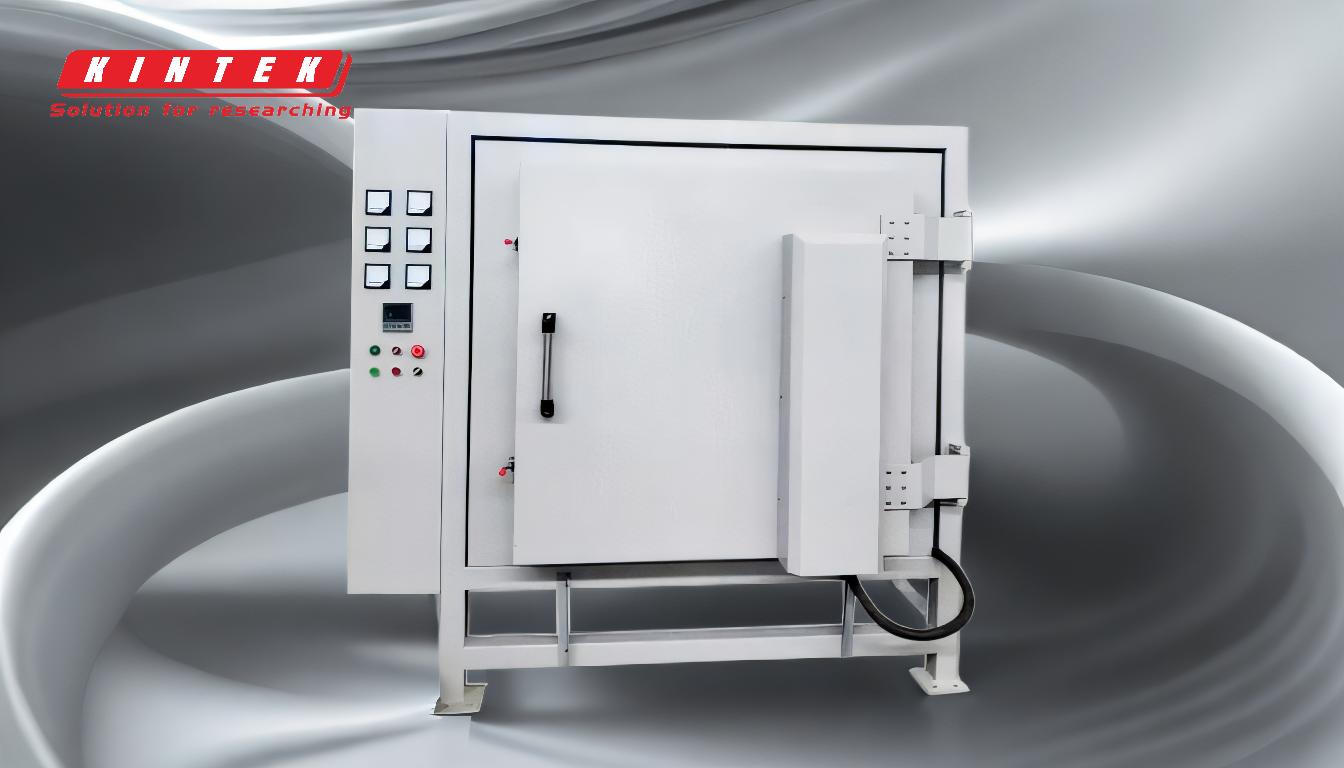
-
Insufficient Sintering at High Heating Rates:
- When the heating rate is too high, the internal regions of the alumina nanoparticle blank may not achieve sufficient sintering. This is because the rapid heating does not allow enough time for the particles to rearrange and bond properly.
- The result is a material with inconsistent sintering degrees across different areas, leading to structural weaknesses and potential defects.
-
Uneven Densification:
- High heating rates can cause significant differences in sintering degrees between the surface and the interior of the blank. The surface may sinter more quickly due to direct exposure to heat, while the interior remains under-sintered.
- This uneven densification can lead to a high-temperature melting peak, where the material begins to melt before achieving full densification, and high crystallinity, which may not be desirable for certain applications.
-
Microwave Heating Advantages:
- Microwave heating offers rapid and uniform heating, which can significantly shorten the sintering time. This method ensures that heat is distributed evenly throughout the material, promoting consistent sintering across the entire blank.
- The uniform heating provided by microwaves helps to avoid the issues associated with high heating rates, such as insufficient sintering and uneven densification.
-
Influence of Heating Rate on Densification:
- The heating rate is a critical factor in the densification process. A controlled heating rate allows for better particle rearrangement and the elimination of porosity, leading to a more densely sintered material.
- High heating rates can disrupt this process, leading to incomplete densification and the retention of porosity, which can compromise the material's mechanical properties.
-
Impact of Particle Size and Composition:
- Smaller particles and homogeneous compositions are more conducive to effective sintering. Smaller particles have a higher surface area to volume ratio, which promotes faster and more uniform sintering.
- Homogeneous compositions ensure that all particles sinter at similar rates, reducing the risk of uneven densification and improving the overall quality of the sintered material.
-
Temperature and Pressure Considerations:
- While the heating rate is crucial, it must be considered alongside other factors such as temperature and pressure. Temperature determines the kinetics of the sintering process and the final material properties, while pressure can enhance particle rearrangement and eliminate porosity.
- A balanced approach that considers all these factors is essential for achieving optimal sintering results in alumina nanoparticles.
In summary, the heating rate plays a pivotal role in the sintering mechanism of alumina nanoparticles. High heating rates can lead to insufficient sintering and uneven densification, while controlled heating rates, such as those achieved with microwave heating, can promote uniform and rapid sintering. The interplay between heating rate, particle size, composition, temperature, and pressure must be carefully managed to achieve the desired material properties and structural integrity.
Summary Table:
Key Factor | Impact on Sintering |
---|---|
High Heating Rate | - Insufficient sintering, uneven densification, and structural weaknesses. |
Controlled Heating Rate | - Uniform densification, reduced sintering time, and improved material properties. |
Microwave Heating | - Rapid, uniform heating for consistent sintering and enhanced densification. |
Particle Size | - Smaller particles promote faster and more uniform sintering. |
Homogeneous Composition | - Ensures uniform sintering rates and reduces uneven densification. |
Temperature & Pressure | - Critical for kinetics, particle rearrangement, and porosity elimination. |
Optimize your alumina nanoparticle sintering process—contact our experts today for tailored solutions!