The effect of pressure on sputtering is significant and multifaceted. Pressure influences the motion of sputtered ions, the energy distribution of source atoms, and the overall quality of the deposited film. At higher pressures, ions collide with gas atoms, leading to diffusive motion and a random walk before deposition, which can improve coverage but reduce energy. Lower pressures allow for high-energy ballistic impacts, enhancing film density and adhesion. Pressure also affects the mean free path of ions, which in turn impacts the sputtering yield and the uniformity of the deposited film. Understanding and controlling pressure is crucial for optimizing sputtering processes.
Key Points Explained:
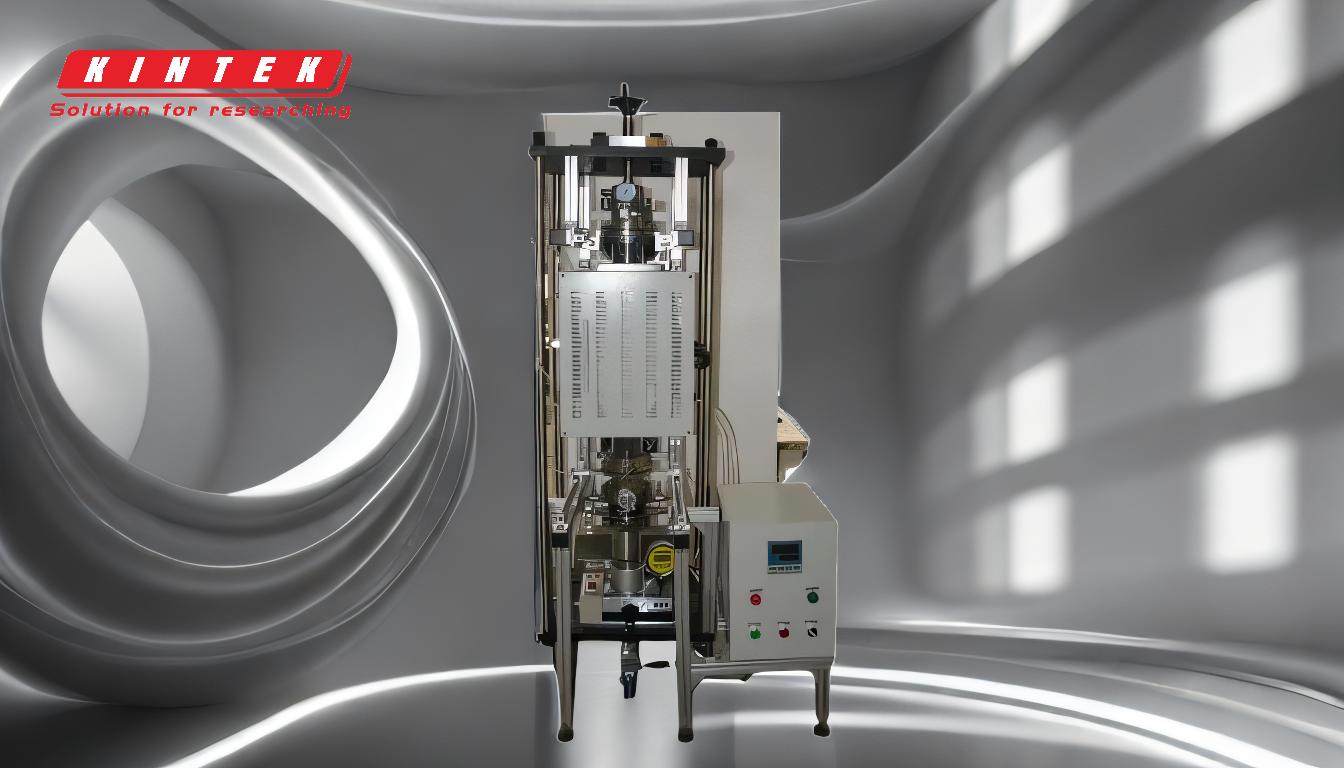
-
Influence of Pressure on Ion Motion:
- Higher Pressure: At higher gas pressures, sputtered ions collide with gas atoms, which act as a moderator. This causes the ions to move diffusively, undergoing a random walk before condensing on substrates or vacuum chamber walls. This results in lower energy deposition and can improve coverage over complex geometries.
- Lower Pressure: Lower pressures allow for high-energy ballistic impacts. Ions travel with minimal collisions, maintaining their energy and direction, which can lead to denser and more adherent films.
-
Energy Distribution and Mean Free Path:
- Mean Free Path: Pressure governs the mean free path of ions, which is the average distance an ion travels before colliding with another particle. Higher pressures reduce the mean free path, leading to more frequent collisions and energy loss.
- Energy Distribution: The energy distribution of source atoms is influenced by pressure. Higher pressures result in a broader energy distribution due to increased collisions, while lower pressures result in a narrower, higher-energy distribution.
-
Sputtering Yield and Deposition Quality:
- Sputtering Yield: The sputtering yield, or the number of target atoms ejected per incident ion, is affected by pressure. Higher pressures can reduce the sputtering yield due to energy loss from collisions, whereas lower pressures can enhance it by maintaining ion energy.
- Film Quality: The quality of the deposited film, including its density, adhesion, and uniformity, is influenced by pressure. Lower pressures generally result in higher-quality films due to the higher energy of deposited ions.
-
Process Control and Optimization:
- Pressure as a Decisive Parameter: Pressure is a critical parameter in sputter deposition processes. It should be carefully controlled and specified, along with deposition temperature, to achieve desired film properties.
- Adjustability: By adjusting the background gas pressure, the process can range from high-energy ballistic impacts to low-energy thermalized motion, allowing for tailored deposition conditions based on the application.
-
Practical Implications:
- Coverage and Uniformity: Higher pressures can improve coverage over complex substrates due to the diffusive motion of ions. However, this can come at the cost of reduced film density and adhesion.
- Energy and Directionality: Lower pressures enhance the energy and directionality of sputtered ions, leading to better film density and adhesion but potentially worse coverage over complex geometries.
In summary, pressure plays a crucial role in determining the behavior of sputtered ions, the energy distribution of source atoms, and the quality of the deposited film. Understanding and controlling pressure is essential for optimizing sputtering processes to achieve desired film properties for specific applications.
Summary Table:
Aspect | Higher Pressure | Lower Pressure |
---|---|---|
Ion Motion | Diffusive motion, random walk, improved coverage, lower energy deposition | High-energy ballistic impacts, denser and more adherent films |
Mean Free Path | Reduced mean free path, more collisions, energy loss | Longer mean free path, fewer collisions, higher energy |
Energy Distribution | Broader energy distribution due to increased collisions | Narrower, higher-energy distribution |
Sputtering Yield | Reduced yield due to energy loss from collisions | Enhanced yield due to maintained ion energy |
Film Quality | Lower density and adhesion, better coverage over complex geometries | Higher density, adhesion, and uniformity, but potentially worse coverage |
Optimize your sputtering process for superior film quality—contact our experts today!