The effect of pyrolysis temperature on bio-oil is significant, as it directly influences the yield, quality, and composition of the bio-oil. At low temperatures (below 450°C) with slow heating rates, pyrolysis primarily produces biochar, while at high temperatures (above 800°C) with rapid heating rates, the main product is gases. Bio-oil is maximized at intermediate temperatures (around 500°C) with high heating rates, where yields of 60-70 wt% can be achieved. The quality of bio-oil is also affected by factors such as feedstock properties, residence time, and condenser design. Understanding these relationships is crucial for optimizing bio-oil production for specific applications.
Key Points Explained:
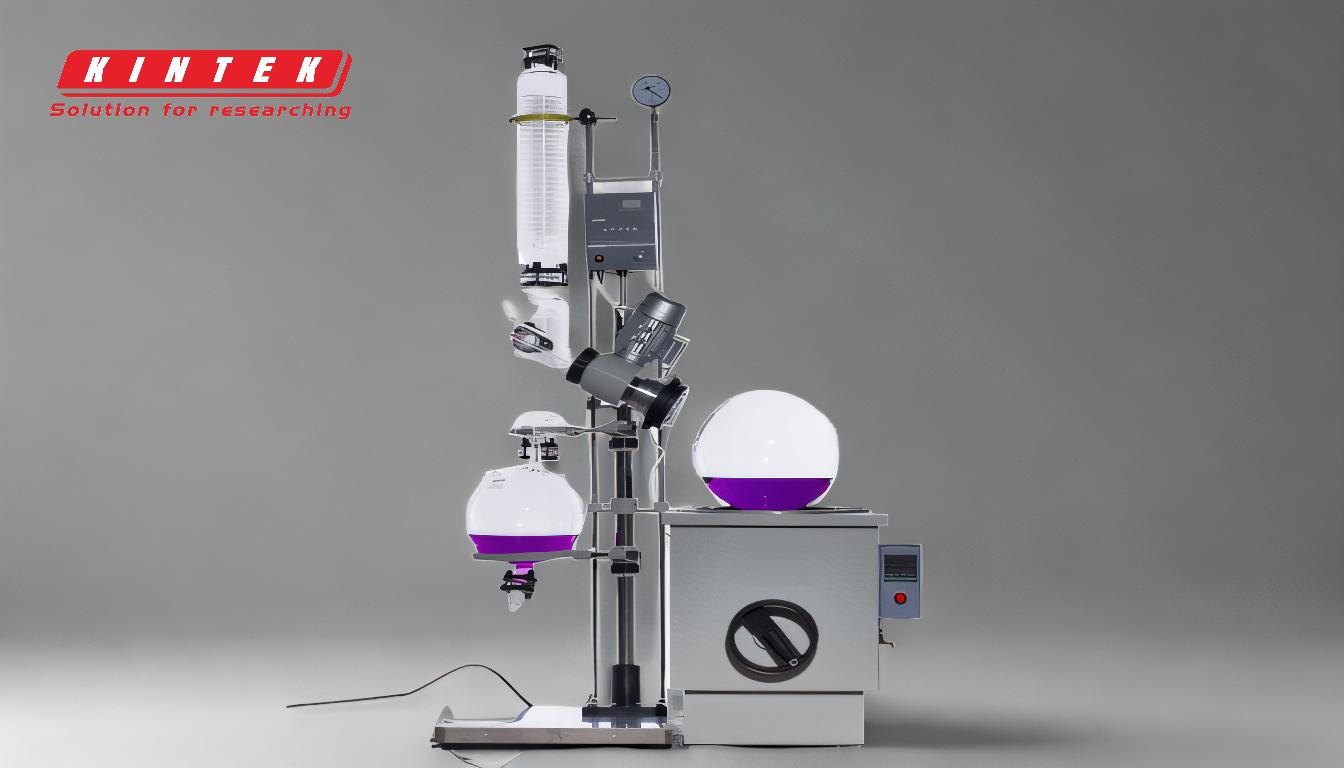
-
Temperature and Product Distribution:
- Low Temperatures (<450°C): At these temperatures, pyrolysis primarily yields biochar. The slow heating rates allow for more carbonization and less fragmentation of the biomass, leading to a solid residue rich in carbon.
- Intermediate Temperatures (~500°C): This is the optimal range for bio-oil production. High heating rates (around 1000°C/s) ensure rapid decomposition of biomass into liquid products, maximizing bio-oil yields (60-70 wt%).
- High Temperatures (>800°C): At these temperatures, pyrolysis mainly produces gases. The rapid heating rates and high temperatures cause extensive breakdown of biomass into smaller molecules, resulting in gaseous products.
-
Heating Rate and Bio-Oil Yield:
- High Heating Rates: Fast pyrolysis, characterized by high heating rates (1000°C/s), is essential for maximizing bio-oil yield. The rapid heating prevents secondary reactions that could degrade the bio-oil into gases or char.
- Slow Heating Rates: These favor the formation of biochar, as the biomass has more time to undergo carbonization rather than rapid decomposition into liquids or gases.
-
Feedstock Properties:
- The composition of the feedstock (e.g., moisture content, fixed carbon, volatile matter) significantly impacts bio-oil yield and quality. For instance, biomass with high volatile matter content tends to produce more bio-oil.
- Specific feedstocks, like coffee grounds, have been shown to yield up to 59% bio-oil at 550°C, demonstrating the importance of feedstock selection in optimizing bio-oil production.
-
Residence Time and Condenser Design:
- Residence Time: Shorter residence times in the pyrolysis reactor are preferred for bio-oil production to minimize secondary reactions that can degrade the oil.
- Condenser Design: The design of the condenser can influence the quality and yield of bio-oil. Multistage condensers, for example, can separate bio-oil into different fractions, each with distinct properties.
-
Bio-Oil Quality:
- The quality of bio-oil (e.g., viscosity, acidity, stability) is highly dependent on pyrolysis conditions. Intermediate temperatures and high heating rates generally produce bio-oil with better properties for fuel and chemical applications.
- The variability in bio-oil properties across different condenser stages highlights the need for careful process design to achieve the desired product quality.
-
Optimization for Industrial Applications:
- Understanding the relationship between pyrolysis temperature, heating rate, and feedstock properties is crucial for scaling up bio-oil production. Industrial processes must be tailored to maximize yield and quality while minimizing costs.
- Case studies, such as the pyrolysis of coffee grounds at 550°C, provide valuable insights into optimizing conditions for specific feedstocks and applications.
In summary, pyrolysis temperature plays a pivotal role in determining the yield and quality of bio-oil. Intermediate temperatures (~500°C) with high heating rates are optimal for bio-oil production, while feedstock properties, residence time, and condenser design further influence the process. These factors must be carefully controlled to produce bio-oil suitable for various industrial applications.
Summary Table:
Factor | Impact on Bio-Oil |
---|---|
Low Temperatures (<450°C) | Produces biochar due to slow heating rates and carbonization. |
Intermediate (~500°C) | Maximizes bio-oil yield (60-70 wt%) with high heating rates (1000°C/s). |
High Temperatures (>800°C) | Yields gases due to rapid heating and extensive biomass breakdown. |
Feedstock Properties | High volatile matter increases bio-oil yield; specific feedstocks like coffee grounds optimize production. |
Residence Time | Shorter times minimize secondary reactions, preserving bio-oil quality. |
Condenser Design | Multistage condensers improve bio-oil separation and quality. |
Ready to optimize your bio-oil production? Contact our experts today for tailored solutions!