Sintering is a critical process in the production of ceramics, significantly influencing their mechanical, thermal, and structural properties. During sintering, ceramic materials are heated to temperatures below their melting point in a controlled atmosphere, causing powder particles to bond through diffusion. This process leads to densification, shrinkage, and the formation of a strong, cohesive structure. The sintering process also affects grain size, pore size, and grain boundary distribution, which in turn determine the material's strength, durability, and conductivity. However, challenges such as warping, sagging, and defects can arise during sintering, necessitating precise control of temperature, cooling rates, and initial grain size. Understanding these effects is crucial for optimizing ceramic properties and ensuring high-quality end products.
Key Points Explained:
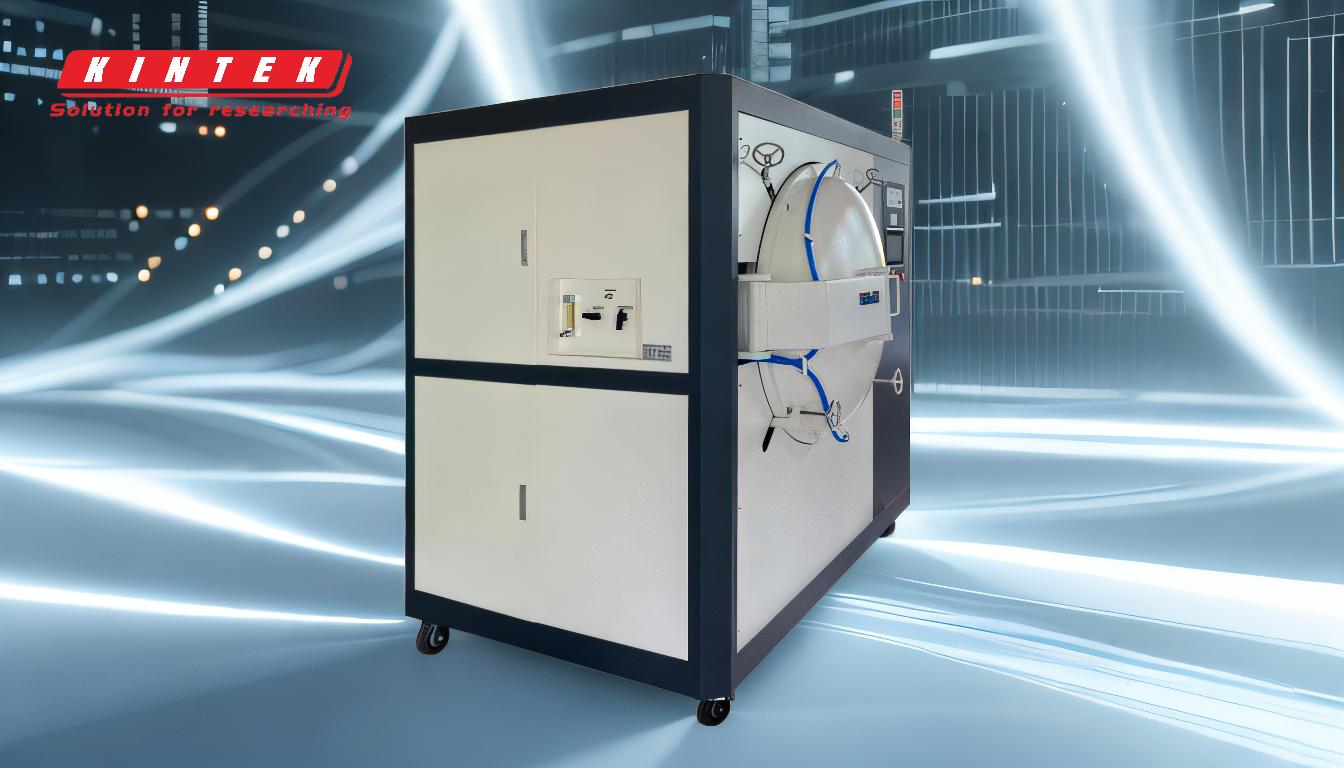
-
Sintering Process Overview:
- Sintering involves heating a "green" ceramic part in a controlled atmosphere to temperatures below its melting point. This causes powder grains to bond through diffusion, enhancing the material's mechanical properties.
- The process results in shrinkage, which determines the final dimensions of the part. The cooling rate can be adjusted to fine-tune properties such as strength and durability.
-
Densification and Microstructural Changes:
- During sintering, pores in the "green compact" diminish or close up, leading to densification. This improves the material's mechanical properties, such as strength and toughness.
- The process directly affects grain size, pore size, and grain boundary distribution in the microstructure. These factors influence the material's overall performance.
-
Controlled Variables:
- Key variables during sintering include temperature and initial grain size. Temperature affects vapor pressure, which in turn influences properties like strength and conductivity.
- Precise control of these variables is essential to achieve desired material characteristics and avoid defects.
-
Challenges During Sintering:
- Common issues include warping due to gravity or friction and sagging of parts. These can lead to defects in the final product, such as uneven dimensions or structural weaknesses.
- Proper design of the sintering furnace and careful monitoring of the process can mitigate these challenges.
-
Thermal and Chemical Reactions:
- In the sintering ore layer, fuel burns, releasing heat that melts minerals. As the combustion layer moves and cold air passes through, molten material cools and crystallizes, forming a mesh structure.
- This process involves solidification, crystal formation, and oxidation of low-cost oxides, contributing to the final material properties.
-
Material Migration and Grain Boundary Movement:
- Under high temperatures and a suitable atmosphere, powder particles in ceramics undergo material migration and grain boundary movement. Over time, this leads to densification and the formation of a strong porcelain body.
- These changes are critical for achieving the desired mechanical and thermal properties in the final ceramic product.
By understanding these key aspects of the sintering process, manufacturers can optimize the properties of ceramic materials and produce high-quality components. For more information on the equipment used in this process, check out the sintering furnace.
Summary Table:
Aspect | Effect of Sintering |
---|---|
Densification | Pores diminish, improving strength and toughness. |
Shrinkage | Determines final dimensions; controlled cooling enhances strength. |
Grain Size & Pores | Influences mechanical, thermal, and structural properties. |
Controlled Variables | Temperature and initial grain size affect vapor pressure, strength, and conductivity. |
Challenges | Warping, sagging, and defects require precise control of sintering conditions. |
Thermal/Chemical Changes | Solidification, crystal formation, and oxidation contribute to final material quality. |
Optimize your ceramic production with precise sintering techniques—contact our experts today!